Air Force to turn over 0.14-micron MMIC technology to industry for advanced radar
WRIGHT-PATTERSON AFB, Ohio, 25 April 2013. U.S. Air Force researchers would like to transfer a submicron microwave chip manufacturing process to industry, and establish a domestic open foundry able to meet the needs of the U.S. Department of Defense (DOD).
The Air Force Research Laboratory at Wright-Patterson Air Force Base, Ohio, released a solicitation late last week (FOA-RQKM-2013-0003) for the Monolithic Microwave Integrated Circuit (MMIC) Supplier Producibility program that seeks to transfer Air Force-developed MMIC technology to industry.
The MMIC Supplier Producibility program will move to industry the Air Force developed 0.14-micron aluminum gallium nitride (AlGaN) and gallium nitride (GaN) on silicon carbide (SiC) submicron chip manufacturing process of MMIC chips.
The program will involve process transfer and optimization, establishing a manufacturing baseline, and fabricating a pilot lot of wafers. Fabrication focuses on decreasing part variation and increasing part yield and reliability. The program will finish with a validation lot of wafers.
The domestic open foundry must be able to fabricate designs from all DOD sources at a competitive price, Air Force officials say. The company chosen to carry out the program must concentrate on yield and reliability, while reducing the cost for RF power amplifiers, low-noise amplifiers, and high-frequency switches.
The reason for transferring Air Force-developed submicron MMIC fabrication to industry revolves around future advanced radar systems design, officials say.
Future active electronically scanned array (AESA) radar sensors are being designed with gallium nitride MMIC devices to improve power-added efficiency and enable multifunction sensor arrays to operate at relatively wide bandwidth, Air Force researchers explain.
GaN devices operate at much higher temperatures and voltages compared to gallium arsenide (GaAs) and indium phosphide (InP) MMIC devices, officials say. Still, GaN MMIC devices are expensive and there are only a limited number of open foundries in the U.S. able to provide wafer fabrication for fabless design houses at a competitive price.
The 0.14-micron gate process developed at the Air Force Research Lab today is not available at a production open foundry. This program, therefore, seeks to develop a source to increase the availability and reduce the cost of GaN fabrication services.
The Air Force is looking for a contractor to identify any missing equipment necessary to implement the 0.14-micron AlGaN/GaN on SiC manufacturing process into their facility, as well as buy and install any capital equipment.
The company that wins the MMIC Supplier Producibility contract must develop a process transfer plan, coordinate meetings, and develop a process design kit (PDK).
After that, the contractor must provide the PDK to a non-affiliated fabless design house, which will design a circuit and device mask to help establish a manufacturing baseline.
The program is on a fast track, such that Air Force officials say they expect to award a contract by this July. Funding this year will be about $500,000; $1.5 million in 2014; $1.75 million in 2015, and $1.2 million in 2016. Only one contract is expected.
Companies interested should respond by email no later than 20 May 2013 to the Air Force's Jennifer Elkins at [email protected]. For questions or concerns contact Elkins by email or by phone at 937-656-9880.
More information is online at https://www.fbo.gov/spg/USAF/AFMC/AFRLWRS/FOA-RQKM-2013-0003/listing.html.
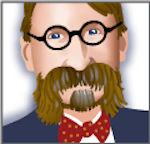
John Keller | Editor
John Keller is editor-in-chief of Military & Aerospace Electronics magazine, which provides extensive coverage and analysis of enabling electronic and optoelectronic technologies in military, space, and commercial aviation applications. A member of the Military & Aerospace Electronics staff since the magazine's founding in 1989, Mr. Keller took over as chief editor in 1995.