One stubborn constant of nearly every electronics design is the biproduct of heat. It's nearly impossible to use power efficiently enough to eliminate waste heat altogether. Enhancing efficiency can help reduce waste heat -- but only to a degree.
Today's new generations of powerful general-purpose processors, general-purpose graphics processing units (GPGPUs), field-programmable gate arrays (FPGAs), and other components notorious for heat generation make the challenge of removing excess heat from electronics more dire and urgent with each passing year.
Neglecting heat removal in electronics can have consequences ranging from reduced processor performance to outright system failure if internal components start to burn or melt. In fact, we've seen predictions that electronics cooling and thermal management challenges have the potential to bring Moore's Law to a screeching halt. Moore's law is the observation that the number of transistors in a dense integrated circuit doubles about every two years.
As a result, systems designers have devised several new proprietary and industry-standard approaches for dealing with growing levels of electronics heat.
Knowing the environment
"The environment is the most important part of thermal management, and we have to design to what we can handle in the environment," explains David Jedynak,Testing and computer modeling of expected operating environments are key parts of anticipating electronics cooling requirements, points out Jens Weyant, vice president of product development at Advanced Cooling Technologies (ACT) in Lancaster, Pa. Sometimes, he says, the thermal models just aren't right.
Many embedded computing designers rely on thermal-management standards set down by the VITA Open Standards, Open Markets industry trade association in Oklahoma City. Among these are VITA 48.1, 48.5, and 48.8 for air cooling, VITA 48.2 for conduction cooling, and VITA 48.4 for liquid cooling. These standards, and others, Weyant contends, suggest test and modeling environments that might not provide an accurate picture.
"The VITA specs suggests applying a constant temperature model," Weyant says. "That is fine for lower-heat-flux applications and uniform heat loads in a uniform heat sink, but when the overall heat load is driven by a single component, you have a concentrated heat load. By modeling it that way, you could design yourself into a corner and give yourself problems at testing."
The problem is a constant temperature model does not account sufficiently for hot spots from high-performance processors or other hot components. "When you apply a constant temperature boundary condition, the model assumes the heat can be removed uniformly from that surface, but when you have a concentrated heat load, that thermal bottleneck is pretty important."
Perhaps a more accurate thermal modeling approach involves looking beyond individual embedded computing models to the whole picture of the computing enclosures. "You need to capture what the chassis is doing, if you can, with modeling some kind of resistance -- even if it's just an estimate," Weyant says. "The second step is to get an accurate representation of the wedgelock clamp or card retainer, which is where most of the heat goes off the card. That resistance can be overly-simplified, which can mislead true performance."
Electronic systems designers are concerned with size, weight, and power consumption (SWaP), how long they want their systems to last in severe conditions, and how much computing power they need to get the job done. "Our customers want something that will work in the environment; that's what they start with," says Curtiss-Wright's Jedynak. "It comes down to an issue of performance, SWaP, and reliability."
Piloted aircraft, for example, can have demanding requirements, yet also hold some advantages based on their operating environments. "If you are in a pod under a wing moving really fast, there is a lot of air there for free," Jedynak continues. "If your fan goes down, there are so many other moving parts, that the minute anything goes wrong, you are landing anyway."
Aircraft systems designers must deal with altitudes, air densities, and air temperatures, Jedynak points out. The trick is to balance different aspects flight, from the runway to maximum altitudes. "The air at altitude is quite cold to start with, but when the air pressure drops, there is less air density to carry away the heat. The real problems come when the platform is sitting on the runway on the hottest day of the year."
Applications and thermal management
So why is there so much heat in today's electronics? A big part of the answer involves advanced data processors, which include general-purpose processors like the latest-generation Intel Xeon and Core i7 general-purpose processors, GPGPUs like the NVIDIA HGX A100 and AMD EPYC, and FPGAs like the Xilinx Virtex-7 and Microchip PolarFire. Even though these processors operate with high efficiency, their huge performance makes them among the biggest heat producers in embedded computing designs.
Companies that use these kinds of components "are pushing the limits of that embedded computing system," says ACT's Weyant. "They must deal with hot chassis temperatures, very high power, and have low temperature rise to work with. They most likely are using advanced heat spreaders, and doing things on the chassis side to reduce temperature."
Embedded computing specialist General Micro Systems Inc. (GMS) in Rancho Cucamonga, Calif., is providing high-performance rackmount computer servers for the U.S. Navy P-8A Poseidon maritime patrol and surveillance aircraft, which has heavy-duty sensor-processing demands for target detection and tracking, as well as for situational awareness.
For this application GMS uses the company's Titan Intel scalable server processors. "These are very high-wattage processors, and although bigger than the processor inside your laptop, they have a very high heat density, or Watts per square inch," explains GMS Chief Technology Officer Chris Ciufo. "When you have processors that dissipate a lot of power, like a scalable Intel Xeon, it can be up to 100 Watts."
The GMS Titan computer servers aboard the P-8A aircraft are running the Navy's Minotaur computer software to fuse together aircraft sensors, ranging from dropped and towed sonobuoys, and the infrared sensors and visible-light cameras that are displayed on the P-8A's operator consoles. "Our Titan servers interface with a variety of the sensors, and Minotaur runs on these servers," Ciufo says.
Thermal management solutions
So, how to deal with these high levels of heat in modern electronics? ACT engineers, for example, have developed a special circuit card wedge lock called the Isothermal Card Edge (ICE)-Lok. "It looks like a typical card wedge lock, and expands in two directions, as opposed to typical wedge locks that expand in only one direction, says ACT's Weyant.
"We can contact more area on the card, and bypass metal-to-metal resistances in the clamp. It gives us lower thermal resistances and twice the contact area," Weyant says. It is proprietary, and we have some patents."
Standard wedge locks, he explains, have wedges at one angle that slide against each other. Instead, ACT's ICE-Lok, which is made of aluminum with standard coatings, has a complex slide that expands in two directions. "It's not a big deviation from traditional wedge locks, and hopefully does not require a redesign in upgrades," Weyant says.
"We have done quite a bit of testing; we measure the surface where the heat enters the card. We are about 30 percent less heat across that joint, as opposed to standard off-the-shelf wedge locks. It is a nice addition to a heat pipe embedded card."
GMS takes inspiration from open-systems design guidelines like the VITA standards, but seeks to refine the company's design approaches to fit individual system requirements. "From a GMS standpoint, we watch the standards. At times we indicate where we are complying with VITA standards, but we have evolved those standards further into our systems when we think we have a better idea," Ciufo says. "We improve on them as we see fit."
The thermal-management baseline of the GMS Titan rugged computer servers aboard the Navy P-8A aircraft is VITA 48. "We applied what we learned there to our Titan 1U and 2U rack-mount servers, which are 100 percent conduction-cooled, but air is sucked through the servers from the front panel to the rear panel to cool the conduction cooled modules inside," Ciufo explains.
"We took our knowledge of conduction cooling, and have heat sinks and heat plates and other baffling on them, to where when air is sucked through these conduction-cooled servers, that air blows across conducted-cooled surfaces and effectively we have a conduction-cooled server, but that just happens to have air flowing through it. We were inspired by the VITA standards, but we do not claim compliance," Ciufo says.
GMS engineers also deviate from the VITA standards by using vapor-phase cooling inside the Titan servers. "We have big hunks of metal that look like top-side heat sinks," Ciufo says. "Inside are fluids that use vapor phase cooling -- like how a heat pipe works, which moves heat from one part of the conduction cooled assembly to another part, and that heat is given up into the air flow. Our vapor-phase cooling is on custom-made metal structures, which is very effective at evening-out heat over a large structure. It moves heat from one area to another to dissipate more heat into the air flow."
Vapor cooling exists in a closed environment, in which fluid boils in hot areas, turns to vapor, and condenses. "We are taking that technology, and embedding it into our six- and eight-slot ATR chassis, which is available in 3U and 6U OpenVPX versions. Heat pipes move the heat from each card edge channel on the right and left sides of the cards, which give up their heat from the processor to the card edge, to the chassis sidewall, and that's where we will have heat pipes to move the heat to the back of the chassis where the fans are. The fans will cool a radiator device, and it continues in a closed-loop pattern."
This approach is an advanced cooling technique for hot-spot cooling that removes more heat than with passive chassis or air flowing by in an open chassis," Ciufo continues. "We also have inlet air and outlet air on the back of the chassis for avionics bays and ground vehicles. Cool air in, and hot air out, is all done in the back of the chassis."
There's more in store for GMS embedded computing chassis in the future as company engineers make a switch from metal to carbon fiber for selected applications. "We are going to build these chassis out of carbon fiber, which has superior energy transfer," Ciufo says. "It is much more conductive than standard aluminum alloy, so we can dissipate more heat." Carbon fiber also is more lightweight than aluminum alloy by 10 to 15 percent, he says.
GMS designers also are expanding on their company's established RuggedCool thermal-management technology to move heat away from hot components like processors. "Rather than using a heat sink on top of the hot components, we use a structure that has metals, a spring, and viscous materials," Ciufo says. "It improves the heat transfer from the top or bottom of the processor better than a gap pad by a factor of two or 10 degrees from processors to heat sink.
Now GMS is ready to introduce a similar technology called Diamond RuggedCool, which uses a diamond material in the middle of the RuggedCool assembly, to increase thermal transfer and decrease thermal resistance by an additional 10 degrees Celsius from the processor to the heat sink.
Curtiss-Wright, on the other hand, essentially relies on the VITA thermal-management specs, yet keeps possibilities open to approaches that involve even wax that melts when exposed to heat, and hardens when heat levels drop, Jedynak says.
Thermal industry standards
"The VITA standards give a good idea of what is available," says Ivan Straznicky, chief technology officer of advanced packaging at Curtiss-Wright. " It's enough headroom in liquid flow through to meet our projected needs in the next one to five years."
Straznicky points out that the VITA standards are the incumbents: VITA 48.1 air cooled; VITA 48.2 conduction cooled; VITA 48.5 air flow by cooling and 48.8 are air flow through cooling; and VITA 48.4 liquid flow through cooling.
"For VPX modules, those standards probably account for 90 to 95 percent of today's designs," Straznicky says. "The mix will be different over the next five years, with less of the air and conduction cooling, and more of the air flow through cooling."
The Sensor Open Systems Architecture (SOSA) design guidelines, which are widely accepted by the U.S. military, has narrowed thermal-management cooling standards down, with VITA 48.2 conduction-cooled systems; VITA 48.4 liquid flow-through cooling, and VITA 48.8 air flow through cooling.
One emerging industry standard for electronics cooling, which could be formally proposed by next year, and be ready for adoption as early as 2024, is called Fluid Flow Through (FFT) cooling, which takes the complexity of air- and liquid-flow-through and puts it only at the chassis level, Straznicky says.
"You could use convection-cooled modules, and design the chassis with air- or liquid flow-through. It will allow you to separate the two, and provide really good thermal management at a more reasonable cost than a lot of air flow through or liquid flow through modules," Straznicky says.
Who's who in embedded computing thermal management
Abaco Systems
Huntsville, Ala
https://www.abaco.com
Advanced Cooling Technologies Inc. (ACT)
Lancaster, Pa.
https://www.1-act.com
Advanced Thermal Solutions Inc.
Norwood, Mass.
https://www.qats.com
Aitech Defense Systems Inc.
Chatsworth, Calif.
https://aitechsystems.com
Atrenne Computing Solutions, a Celestica company
Brockton, Mass.
https://www.atrenne.com
Behlman Electronics Inc.
Hauppauge, N.Y.
https://www.behlman.com
Boyd Corp.
Lancaster, Pa.
https://www.boydcorp.com/thermal/two-phase-cooling.html
Crane Aerospace & Electronics
Lynnwood, Wash.
http://www.craneae.com
Crystal Group Inc.
Hiawatha, Iowa
https://www.crystalrugged.com
Curtiss-Wright Defense Solutions
Ashburn, Va.
https://www.curtisswrightds.com
Data Device Corp.
Bohemia, N.Y.
https://www.ddc-web.com
Elma Electronic
Fremont, Calif.
https://www.elma.com
Extreme Engineering Solutions (X-ES) Inc.
Verona, Wis.
https://www.xes-inc.com
General Micro Systems Inc.
Rancho Cucamonga, Calif.
https://www.gms4sbc.com
Kontron America Inc.
San Diego, Calif.
https://www.kontron.com
Meggitt Defense Systems Inc.
Irvine, Calif.
https://meggittdefense.com
Mercury Systems Inc.
Andover, Mass.
https://www.mrcy.com
Milpower Source Inc.
Belmont, N.H.
https://milpower.com
Parker Hannifin Corp. Aerospace Group
Alexandria, Va.
https://www.parker.com
Vicor Corp.
Andover, Mass.
https://www.vicorpower.com
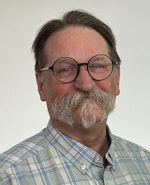
John Keller | Editor-in-Chief
John Keller is the Editor-in-Chief, Military & Aerospace Electronics Magazine--provides extensive coverage and analysis of enabling electronics and optoelectronic technologies in military, space and commercial aviation applications. John has been a member of the Military & Aerospace Electronics staff since 1989 and chief editor since 1995.