Modern missions on new and legacy military vehicles demand capable embedded computing systems and components in small form factors.
Aerospace and defense engineers are under considerable pressure to design and develop, integrate, and upgrade embedded computing systems such that they deliver ever greater capabilities in ever smaller sizes. Modern embedded computing advances enable engineers to pack robust processing power in full-featured small-form-factor (SFF) systems - and aerospace and defense program managers and end users are anxious to benefit from such innovations.
Space is at a premium in all aerospace and defense vehicles; new platforms are more compact than ever before, and legacy platforms are being infused with more and more systems, capabilities, and functionality. A marked increase in command, control, communications, computers, intelligence, surveillance, and reconnaissance (C4ISR) missions, conducted with these vehicles, is driving the demand for SFF embedded computers.
The ability to gather, process, share, and store intelligence, surveillance, and reconnaissance (ISR) data - including text, imagery, and video - is critical for real-time informed decision making, mission success, situational awareness, and safety. SFF embedded computing plays a large role in bringing these robust compute capabilities, features, and functionality to the field in ever smaller packages.
Platforms shrinking
Looking at the big picture in aerospace and defense, "we're starting to see consolidation of platforms that are traditionally expensive to maintain. They are starting to shrink in size, primarily because of the logistics associated with maintaining the platforms; the cost is high, so there is a push to make the platforms more cost-effective," says Jim Shaw, executive vice president of engineering at rugged computing specialist Crystal Group in Hiawatha, Iowa. For example, applications that historically employed "C-130s are going down to something like a Bombardier Dash 8 or a Cessna Citation. The platform size is becoming smaller, so the tube is smaller; there's less area to get content or capabilities into that tube which is, by necessity, driving the industry to seek small-form-factor solutions.
"We're seeing some shift in interest away from rackmount servers to embedded, SFF, lightweight, and extremely small size," Shaw continues. "We follow the Intel Roadmap, so we use a lot of embedded boards that are extremely small in size, and we're seeing that footprint shrink with a focus on products under 10 pounds in weight."
Crystal Group's RE1401 NUC rugged embedded computer - measuring 4.8 by 6.3 by 1.9 inches - is a reflection of that trend toward extremely compact packages, Shaw says. Aerospace customers seek even smaller embedded computers for a growing number of applications, however. "It's driving in that direction. In fact, we're seeing a lot of interest in system on chip (SoC) applications. It's really taking all the content in a CPU and motherboard and turning into mostly a CPU with all the features pushed into that silicon."
The move toward ever smaller and more powerful embedded computers in shrinking platform sizes provokes other systems-integration challenges. "Power and thermal are just as much of an issue. As a product gets smaller, there's less area to dissipate the heat; you have to be innovative and it requires a certain amount of system engineering," Shaw says. "In embedded computing, you've got big die and small boards; you have to be careful about how you package them so there are no issues with shock, vibe, and crash."
Consolidation
The sizes of embedded computing systems and components becomes so important based on what designers are putting them into: very tight spaces in fixed-wing and rotary-wing aircraft, light armored vehicles, and unmanned aircraft systems (UAS), says Aneesh Kothari, director of marketing at Systel in Sugar Land, Texas. "Space is at a premium, and systems need to be size, weight, and power (SWaP)-optimized - as small as possible but still incredibly high performance, which lends to interesting thermal design challenges."
Crystal Group, Systel, and other embedded computing companies are witnessing and delivering systems to facilitate greater hardware consolidation; they are supplanting several systems with hybrid or hyperconverged solutions. Replacing multiple big boxes with a single SFF embedded system, a growing trend, promises such benefits as cost and space savings.
"Defense customers are shifting from standalone systems to all-in-one embedded systems," Systel's Kothari explains. "What has been the case in the past is one computer doing processing, another handling storage. An embedded all-in-one approach combines video capture, processing, and storage in one package - which from a SWaP, cabling, line-replaceable unit (LRU) failure, vendor management and support, and price perspective is much more desirable.
"It's a trend we're seeing across the board: a single LRU vs. multiple systems. Now technology is at a level where an all-in-one box can eliminate four other boxes," Kothari says. As an example, Systel's EB7001 rugged SFF video capture system provides video processing, compute, encoding, and storage in one LRU.
Systel's EB7001 rugged SFF video capture system is deployed in airborne ISR applications to enhance situational awareness and for more effective target detection. The ISR work flow captures several high-definition (HD) video streams, brings them in from the sensor payload, and encodes them to the H.264 standard.
"Onboard exploitation is accomplished through the central processing unit (CPU), allowing the user to run the mission maps with synchronized metadata," Kothari describes. "Users can interrogate the encoded video and create intelligent products. The video is presented on dual displays onboard the vehicle and is distributed via various radio formats and networks to command-and-control centers. Video is also recorded and securely stored on solid-state drives (SSDs) for further review and analysis."
Many systems using SFF embedded computing components are airborne, ranging from manned aircraft cabins to unpressurized compartments, helicopter equipment bays, and unmanned vehicles, says Rodger Hosking, vice president of embedded computing specialist Pentek Inc. in Upper Saddle River, N.J.
"We are seeing numerous requests for SFF systems and for board-level products that are integrated into SFF systems," Hosking says. "Most of the applications we see require software radio signal acquisition, digital signal processing, and signal generation for communications, radar, and countermeasures."
Programs using Pentek SFF systems and board-level products include: airborne radar electronic warfare (EW) transponders; small, ruggedized wideband radio-frequency (RF) signal acquisition and recording systems; and SIGINT surveillance subsystems for unmanned aircraft. "SFF acquisition systems located near antennas and sensors can digitize signals and then deliver them over optical cables to processing systems, dramatically reducing the weight, size, cost, bandwidth restrictions, and signal degradation of copper cables," Hosking says.
Modularity and miniaturization
Demand for SFF embedded solutions is coming from applications ranging from missile defense systems and combat vehicle upgrades to aircraft modernization and new unmanned ground, air, and underwater platforms, says Mike Southworth, product manager at Curtiss-Wright Defense Solutions in Salt Lake City.
"Customer interest is piqued by the modularity and miniaturization we're achieving with rugged commercial off-the-shelf (COTS) multi-core processors, graphics, and networking technologies that come pre-validated to a host of MIL-STD and DO-160 test conditions," Southworth adds. DO-160 is the Radio Technical Commission for Aeronautics (RTCA) standard for Environmental Conditions and Test Procedures for Airborne Equipment. "With a boost in performance yet a reduction in size, weight, power consumption, and cost (SWaP-C), these rugged COTS solutions significantly help system integrators to reduce, even eliminate, traditional program non-recurring engineering (NRE) cost and technical risk."
SFF embedded systems intended as LRUs increasingly are moving to industrial computer-on-module (COM)-based form factors, such as COM Express, or stackable single-board computer architectures, like PCI Express/104, Southworth observes. "These mezzanine/stackable modules are not only cost effective, low power, and physically small, they allow systems based on them to take advantage of the latest high-performance PCI Express, Serial ATA (SATA), Ethernet, and graphics standards. I/O modules based on the even smaller Mini PCI Express standard are also increasingly hosted on system carrier boards in these SFF systems to support add-on, application-specific requirements, such as for legacy interfaces for MIL-STD-1553, CANBus, and ARINC 429."
Defense platforms involved in C4ISR upgrade efforts routinely specify these SFF systems to improve situational awareness and add mission processing capabilities to interface with vehicle and aircraft sensors, data links, and other on-board LRUs, Southworth says.
Unmanned aircraft modules
An unnamed developer of unman-ned aircraft required a rugged mission management computer for an optionally piloted airborne platform's mission system architecture, which featured capabilities for simultaneous real-time data collection from several ISR and communications sensor payloads. The integrator for the advanced intelligence gathering air system sought a robust processor subsystem to interface with the various on-board payloads and mission subsystems, including electro-optic and signals intelligence (SIGINT) sensors, avionics and communications systems, Ethernet switches, situational awareness video cameras/encoders, and network attached storage (NAS) devices.
"This device would interrogate the installed sensors and automatically configure the on-board software to manage the [sensor] payload without human intervention," Southworth explains. The platform integrator specified high-performance computing requirements, but was especially sensitive to SWaP considerations. "This translated into the mission management computer LRU needing to support the latest multi-core Intel Core i7 processing capabilities together with a high number of interfaces to the many payload, video, network, and input/output (I/O) devices that would be required for various potential manned or unmanned system configurations."
Curtiss-Wright's Parvus DuraCOR mission computer system proved suitable given its rugged, compact and modular design. "The unit's Intel Core i7-based quad-core processor provided the level of performance that the customer sought, and the open-architecture modularity enabled the relevant I/O, video, and network modules to be pre-integrated at the factory for a turnkey solution," Southworth says.
A modified COTS variant of the subsystem was integrated using rugged off-the-shelf, mini-PCI Express and PCI Express/104 modules, including: dual-redundant MIL-STD-1553 and ARINC 429 data bus interfaces, several Gigabit Ethernet network interface cards (NICs), and opto-isolated digital input/outputs. The system was also equipped with an AMD Radeon graphics processing unit (GPU) card with 3D graphics engine support for Microsoft DirectX 11 and 576 gigaflops of peak single- precision, floating-point performance. It added three additional high-definition video interfaces to the system, for a total of six, and the ability to perform general-purpose graphics processing unit (GPGPU) parallel computing.
"This integrated GPU functional- ity helped to consolidate aircraft LRUs, eliminating the need for a separate laptop computer for the pilot to view moving map information, since this could now be done through the mission management processor LRU," Southworth says. "A one-slot, removable, 2.5-inch, solid-state disk add-on segment, capable of hosting high-capacity, solid-state media, was also integrated to support removable mission data storage requirements."
The customer can deploy an integrated ISR mission processor subsystem tailored to the needs of the advanced ISR aircraft's mission system architecture, Southworth notes. "Thanks to the modularity of the subsystem architecture, the processor integrates a high number of network, video, serial, avionics, and other digital inputs/outputs tailored to support the various manned or unmanned ISR mission requirements of the platform. The customer can realize the platform's full potential, interfacing with installed sensors and auto-configuring mission software to manage the payload sensors.
"Engineers developing systems for military and aerospace programs should consider the technical, schedule, and cost advantages that leveraging rugged COTS modular subsystem technology from trusted partners can provide to fulfill contracts faster, more profitably, and with the best technically acceptable solution," Southworth advises.
Legacy upgrades
The embedded industry will move toward SFF module-based solutions on a 3U/6U baseboard for legacy systems, with the baseboard providing the required backplane interface, predicts Joe Eicher, director of global business development at Kontron America's Defense division in Poway, Calif. SFF module-based systems provide added "rugged shock-and-vibration protection at a system level, rather than with the individual boards that make up the system," he says. "Using a modular SFF approach also has benefits that apply to scalability and obsolescence management."
Kontron's COM Express module- based Cobalt compact mission computer has been deployed in ground mobile, unmanned vehicle, and rotary-wing applications that require standardized and cost-effective high-performance computing coupled with a flexible and rugged SFF system.
"Helping to cut costs and speed designs, Cobalt offers a pre-integrated series of known and established system profiles that include a storage, situational awareness, and switch-stacked server profile," Eicher says. "Customers see the value in application-ready SFF systems that offer upgradable, rugged options allowing them to leverage the attributes of a carrier board approach with the flexibility of mezzanine options, enabling them to remain competitive in this tough market."
A growing number of SWaP-constrained applications are driving greater demand for multi-core SFF embedded computing systems, Eicher explains. "Defense system developers see these platforms as much more economical than the traditional 3U and 6U system solutions, enabling them to meet tighter budgets. They also provide versatility at the board level, allowing mil/aero OEMs to streamline designs of custom layouts for components and connectors."
Building blocks
Engineers at Hughes Defense and Intelligence Systems Division (DISD) in Germantown, Md., set out to develop a small, sophisticated satellite communications (SATCOM) solution for ISR operations that could perform under a wide range of conditions, bandwidth challenges, and difficult terrain. The HM200 ruggedized mobile modem is designed to deliver high data throughput for beyond-line-of-sight (BLoS) comms-on-the-move (COTM) applications in a compact, low-power design for use across land, sea, and airborne platforms. Engineers opted to integrate the Hughes HM200 subsystem and specialized antenna connectors into Kontron's Cobalt SFF embedded computing platform.
Kontron engineers customized the company's COTS Cobalt 901 to match Hughes DISD's SATCOM system requirements. Kontron's sealed and validated IP67 embedded computer system offered Hughes engineers a wide selection of processor, storage, power, and interface options, as well as a small terminal footprint optimized for performance, harsh environments, and reduced SWaP - top priorities for Hughes to meet end user requirements.
"Adding capabilities and equipment into the same footprint presents a great challenge for developers, yet is frequently a requirement in mobile and portable system upgrades," Kontron officials say. Cobalt's scalable and modular open-standard features, integrated into a small form factor, facilitate upgrades.
The HM200 is an integrated solution providing a constant, reliable feed of critical real-time information to support a wide range of military operations, including: ISR, border patrol, search and rescue, disaster response, wildfire monitoring, oil platform communications, cellular backhaul, and airborne platforms. As an open-architecture COTS solution, it can be readily installed into a wide range of manned and unmanned, fixed- or rotary-wing platforms to deliver video, voice, and data capabilities, officials say.
"Kontron's Cobalt system ideally and cost-effectively met our needs for a scalable integrated building block architecture," says Wayne Marhefka, senior director of business development at Hughes DISD.
"Implementing new mobile broadband technology is critical for real-time situational awareness and ISR capabilities that keep military personnel one step ahead," officials say.
Slow SFF adoption
Aerospace and defense vehicles and systems are shrinking in size, certainly, but widespread adoption of SFF embedded computers has yet to be realized. Some industry veterans speculate that ancillary technologies are slowing SFF progression in mil/aero applications.
"As the electronics and packaging become more integrated and smaller, it's the external, real-world 38999 I/O connectors and the human factors (MIL-STD-1472) that are forcing SFF physical sizes to be much larger than they could be if defined by the size of the electronics by itself," says Doug Patterson, vice president of marketing and business development at Aitech Defense Systems in Chatsworth, Calif. The MIL-STD-1472F Department of Defense Design Criteria Standard: Human Engineering establishes human engineering criteria for the design and development of military systems, equipment, and facilities.
"The problem today is that no one will pay to upgrade a platform and replace all the connector harnesses, too. That's unrealistic, so SFF with other than the standard 38999 connectors is relegated to new program starts only, and those are like hen's teeth," Patterson says.
Demand for SFF embedded systems has increased exponentially among aerospace and defense customers across the board, especially for ISR applications, Systel's Kothari says. Video plays a more important role than ever in C4ISR applications, as real-time video and data have become critical for mission success, he adds.
"There is an imperative for 'eyes on the target' throughout the entire command ecosystem, which has led to increased demand for high-quality, low-latency, full motion video by military leadership," Kothari explains. Greater use of standard-definition (SD) and high-definition (HD) cameras has made video capture and encoding vital to missions conducted on numerous platforms in which space is at a premium and SWaP constraints are a vital consideration, he says. "SFF embedded systems can offer high-performance computing in a rugged, small package while still meeting military requirements for use in harsh environments, including a wide spectrum of operating temperatures, shock and vibration, electromagnetic interference/electromagnetic compatibility (EMI/EMC), dust, and water ingress protection."
A modular approach to SFF embedded computing also benefits video ISR systems and applications. "Utilizing high-speed PCI Express lanes in a modular, stackable fashion allows for highly customizable and powerful SFF solutions," Kothari says. "For extremely space-constrained platforms and applications, such as unmanned vehicles, PC/104 systems have been replaced by newer COM Express form factor boards and systems. COM Express allows for greater I/O flexibility and is more capable of handling the ever-increasing computing and graphics demands of the modern military. Another advantage, COM Express allows system integrators such as Systel to buy off-the-shelf CPU/chipset/memory technology and embed it into embedded products without worrying about chipset-level design. We can customize carrier boards to suit the application."
System designers and integrators are adopting a hybrid approach, "combining these types of standards to create highly customized and flexible systems for specific applications," Kothari says. "The application requirements are driving the overall system-level design without being hampered by rigid board-level architecture."
AI and FPGAs
The demand for SFF systems is increasing, yet continues to be fragmented and specialized, observes Dennis Smith, vice president of engineering at Themis Computer in Fremont, Calif.
"Defense computing is moving more toward the edge, requiring form factors to become smaller and increase in performance. ISR, personal radar, and soldier-level communications will drive adoption in increasing numbers, while military application-specific requirements will keep the market specialized and fragmented," Smith anticipates.
In fact, a wide variety of aerospace and defense applications employ Themis SFF systems, Smith describes. The Joint Light Tactical Vehicle (JLTV) uses Themis Computer's NanoSwitch 10- or 16- port tactical switch compliant with the Vehicular Integration for C4ISR/EW Interoperability (VICTORY) standard. The company's NanoPak SFF computer is being used in smart displays that control Army electrical generators in unmanned aerial vehicle (UAV) ground stations, while its NanoPak i7 is employed in personal radar and vehicle tracking systems.
Sensor fusion, aided by machine learning, is a key application area for SFF embedded computers. Machine learning, a type of artificial intelligence (AI) in which software algorithms iteratively learn from exposure to data and automate data analysis, is helping aerospace and defense organizations glean critical information, such as target identification, from ever-increasing data stores.
AI is being used to provide greater soldier-level decision support, requiring "not only high compute capability but also localized storage," Smith says. "Soldiers are requiring robots to take on increased responsibilities in the battlefield, such as front-end support for hazard avoidance, intelligence gathering, and in some instances combat engagement. Autonomous operation is being investigated for applications in both land and air-based vehicles. Some of these applications require increased processing clock speed, while others utilize multi-core features and need higher core count."
Customers have expressed interest in using field-programmable gate arrays (FPGAs) for increasing performance beyond a standard processor, Smith says. "FPGAs come in a variety of power and performance levels that suit integration into SFF systems," typically used for radar, SIGINT, software-defined radio, video processing, and AI.
Deep learning with GPGPUs
"Deep Learning Neural Networks using GPGPUs in small-format, self-contained enclosures are all the rage," insists Aitech's Patterson.
Computing based on deep learning models the brain's neural learning process to enable continuous learning, increased intelligence over time, and more accurate and faster results. GPGPUs excel at visual, image, and graphics output, using hundreds of cores to process several image data elements simultaneously; they combine well with deep learning to help users understand "what an image is, how to identify it, and how to move forward," Patterson describes. It fills a "market need for image processing - for object detection, tracking, classification, and threat assessment."
With so much high-resolution data being collected, limited compute power can prove detrimental in the field. Computer hardware must be able to keep pace with modern sensors; such limitations can cause users to "dumb down" sensors and could slow the real-time response essential in battlefield scenarios, Patterson cautions. "Use GPGPUs to avoid the pitfalls; parallel processing is the way to go.
"Sensor platforms contained within medium to large UAS, tactical ground vehicles, remote chemical detection and warning sensor trailers, C4ISR audio and video processing, homeland security, and border monitoring are only a small sampling of potential applications for high-performance GPGPU modules," Patterson says. GPGPU-based SFF embedded computers can also cut remote mission display computer size, weight, and cost on manned and unmanned helicopter and UAS platforms, he adds.
"There is certainly an evident trend to save weight and to try to minimize the size of the systems," says Thierry Wastiaux, senior vice president of sales at Interface Concept in Paris. "That being said, aerospace and defense customers will not compromise the safety and reliability of the systems.
"They will not take high risks to go for small form factors," Wastiaux continues. If the SFF embedded computing system uses unreliable connectors, for instance, they will not accept it. COM Express connectors, he says, do not support vibrations and temperatures well and "they are not suited for harsh environment applications.
"In many cases, customers will still need high computing power especially in radar and EW systems. In this case, high-end processors and FPGAs have to be used to ensure reaching the high-level performance of a new system with a competitive edge on the market," Wastiaux explains. "These high-performance components emit heat that must be safely extracted from the boards and systems. This can be a limiting factor to reduce size and weight."
In fact, many SFF fanless computer box designers have to limit the processing power of their systems to be able to extract the heat from the processors, Wastiaux says. "If you want several processors in parallel, separate SFF fanless boxes will not be a good solution because a lot of space and weight will be lost."
A solution, Wastiaux says, lies in the OpenVPX VITA standard, which "is exactly defined to reach a good compromise between reliability and size. For instance, 3U OpenVPX can be considered as a relatively small form factor appearing to be the best approach that is used by many defense applications."
Interface Concept has won contracts for 3U OpenVPX processor and switch boards for safety-critical systems on UAS programs led by defense primes, Wastiaux explains. Company engineers extensively use the VITA 57 small form factor for signal acquisition and optical communication in systems.
A VITA 57 standard FPGA mezzanine card (FMC) is a small mezzanine card format dedicated to signal acquisition and data transfers that is plugged on a FPGA carrier board and allows high-data throughput and very low latency. "All that is required is swapping out the FMC module and adjusting the FPGA firmware," Wastiaux says. "This standard can also be used for data communication, electrical or optical." In the case of Interface Concept's IC-OPT-FMCPa module, optical communication at rates up to 28 gigabits per second (Gb/s) are achieved with Reflex Photonics transceivers, he explains.
The future of SFF
The demand for SFF is still in its infancy given that there are no universally adopted, open systems standards for SFF in the embedded market yet, Aitech's Patterson says. "Customer interest will increase only if the functionality contained within the SFF meets the application space claim and overall functionality at a cost-effective price.Small embedded, backplane-based 3U subsystems are still fitting the needs."
SFF embedded computing technology will, nonetheless, continue to advance, and pique the interest of myriad aerospace and defense engineers. "Innovation will continue to fuel further reductions in SWaP, while delivering more performance and functionality than ever before, and at a lower acquisition cost," predicts Southworth at Curtiss-Wright Defense Solutions, which he says "will continue to leverage next-generation advanced processor, graphics, and networking technologies to solve customer problems and enable new capabilities for the warfighter."
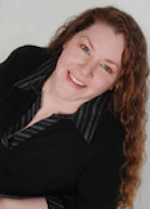
Courtney Howard | Executive Editor
Courtney, as executive editor, enjoys writing about all things electronics and avionics in PennWell’s burgeoning Aerospace and Defense Group, which encompasses Military & Aerospace Electronics, Avionics Intelligence, the Avionics Europe conference, and much more. She’s also a self-proclaimed social-media maven, mil-aero nerd, and avid avionics geek. Connect with Courtney at [email protected], @coho on Twitter, and on LinkedIn.