Today's technological revolution in space, ranging from long-term harsh-environment military space applications to commercial space telecommunications and internet access, is driving new trends in electronics components that can withstand varying levels of radiation.
Radiation-hardened and radiation-tolerant electronics are designed or upscreen-tested to withstand the effects of ionizing radiation such as gamma rays and cosmic rays, which can disrupt or damage electronic circuits. These components are crucial not only for orbital space, but also for space exploration, nuclear power plants, and particle accelerators.
Radiation-hardened and radiation-tolerant electronics typically share several different traits, such as shielding, redundance, rad-hard-by-design components, and testing and upscreening.
Shielding made from materials like lead, tungsten, or other heavy metals can protect sensitive components from radiation, while redundant systems and circuits often are built into radiation-hardened electronics to ensure continued operation even if parts of the system suffer disruption or damage from radiation.
Some space applications -- especially those in high-Earth orbits for long-duration military missions, require components that are specially manufactured for heavy resistance to radiation-induced damage. This can involve different materials or designs compared to commercial-grade components, which can be time-consuming and very expensive to design. Rad-hard-by-design electronics typically are more expensive than commercial-grade components because of the specialized design, manufacturing, and materials involved.
Extensive testing under simulated radiation can help verify the performance and reliability not only of radiation-hardened electronics, but also of commercial-grade parts that can be designed into space systems.
When designing or specifying radiation-hardened or radiation-tolerant parts for space, systems designers must consider factors like total ionizing dose (TID), single-event effects (SEE), and displacement damage dose (DDD) to make electronic components that play a vital role in ensuring the reliability and functionality of electronic systems in harsh radiation environments.
Orbiting satellites for intelligence, surveillance, reconnaissance, and communications make up the bulk of today's space electronics market, with narrow but important slivers of the market going to long-term military missions, systems designed to operate through nuclear explosions, and for land-based nuclear power monitoring and control.
New space
The biggest part of today's radiation-hardened and radiation-tolerant applications involves so-called "New Space," or commercial applications for telephone service, Internet access, and streaming data for video and sophisticated sensor applications. These services typically come from commercial satellite constellations composed of spacecraft typically expected to survive in space only for a short time, such as five years.
New-space applications pose big rad-hard design challenges because they are extremely cost-sensitive, so require
just the right amount of radiation hardening for their specific orbits and expected lifetimes. Excess capability increases costs, yet not enough rad-hard capability risks unanticipated on-orbit failures, which can require additional rocket launches to provide replacement spacecraft.
There's always risk involved in New Space applications, as well as a delicate balancing act between rad-hard components, upscreened commercial off-the-shelf (COTS) components, and pure commercial-grade parts.
"We need to meet the spec, but not overdo the spec," says Timothée Dargnies, chief executive officer of rad-hard supplier 3D Plus in Buc, France. "We maintain the level of radiation that the customer needs, but we bring a lot more capability to help compete with pure COTS for space applications that last three to four years," Dargnies says.
3D Plus covers the entire spectrum of the radiation-hardened electronics market, Dargnies says, but doesn't find the job any easier because of New Space competition from pure-COTS electronic components. "We are seeing bigger and bigger competition from the COTS market, from New Space, to commercial, to military applications."
Often the problem comes from a lack of available rad-tolerant parts on the market, which can force spacecraft designers to use pure-COTS. "Because of sensors and processing, designers don't find pure rad-hard parts that fit their requirements, so they use commercial parts," Dargnies says. "It's getting harder and harder to compete with pure COTS."
In response, 3D Plus seeks to add value not available with pure COTS parts. "We can package everything inside of a smaller package," he says. "We are building components to put in more features and capability, and in the future we will bring new products that are easy to use from the outside, but complex from the inside, to bring more features and capability to our customers."
The difference between electronic parts designed for New Space and pure-COTS components is the reason that Apogee Semiconductor in Plano, Texas, originally entered the space market. "We started this in 2017 to go after New Space market," says Anton Quiroz, chief revenue officer at Apogee. "We saw a big gap between commercial semiconductors and radiation-hardened semiconductors in price and performance."
New Space risks also can involve a willingness to chance suffering a potentially catastrophic radiation-induced event that is unlikely to happen, such as a cosmic ray hit from distant stars, Quiroz says.
Even so-called inexpensive short-duration cubesats can risk cosmic ray hits coming into Earth orbit from stars, Quiroz points out. "New Space also has the galactic cosmic rays coming from stars," he says. "They are heavier and I think of them like sniper shots; those can happen as a probabilistic event in space. The further you are out in space, the more likely that is to happen."
Test and upscreening
One way to specify commercially developed electronic components for space applications is lot-by-lot upscreening of the parts to demonstrate they can withstand space radiation for a given amount of time. Several public and private test laboratories exist that can simulate the kinds of environments that commercial parts will encounter in space.
Where upscreening for single-event effects are concerned, parts designers typically rely on three labs: The Texas A&M University Cyclotron Institute in College Station, Texas; the Lawrence Berkeley National Laboratory in Berkeley, Calif.; and the National Superconducting Cyclotron Laboratory at Michigan State University in East Lansing, Mich.
At these facilities, technicians show semiconductors with heavy-ion particles at rates that customers choose to simulate their expected space environments most closely. "Depending on the facility, you can pick whatever element you want to hit, and the energy level you're looking for," says Apogee's Quiroz. "They bombard the device to make sure there are no anomalous events."
Other public and private labs are available to screen test for total ionizing dose, as well as for exposure to neutron displacement damage.
Rad-hard market trends
Just a few years ago it was popular among space electronic systems designers to use pure-COTS parts as frequently as possible, with the promise of readily available spacecraft replacements. After some bad experiences, however, some spacecraft designers are starting to rethink their original assumptions.
We're starting to notice people looking at designing for more radiation resilience for low-Earth orbit (LEO)," says Apogee's Quiroz. LEO is getting so crowded, and medium-Earth orbit (MEO) has harsher radiation environments. This is leading to people to use more radiation-tolerant parts instead of pure commercial and doing some testing."
Even designers of short-duration cubesats are giving radiation-hardened parts a second look. "Even the companies that started as building commercial cubesats, they are getting questions about higher radiation levels," Quiroz says. "They are trying to figure out how to get those more radiation resilient."
Recent trends also saw much of the nation's space electronics parts fabricated outside U.S. borders, yet that may be starting to change, Quiroz says. "Semiconductors over past decade has seen a lot of off-shoring, but now we're trying to bring some back. We are in desperate need of U.S. plastic packaging facilities, because most of that has gone overseas -- specifically to China. There have been a few government solicitations to bring packaging back, but is under the umbrella of advanced packaging. We don't know how to do that cost effectively in the U.S."
Radiation-hardened products
Radiation-hardened electronics specialists are bringing out several new products in response to current space market trends. 3D Plus is offering space-qualified systems-in-module with high-capacity sensors that integrate different electronic parts into a package, such as solid-state memory, sensors, field-programmable gate arrays (FPGAs), discrete power, and analog parts.
The company also has started offering components that company officials call companion parts. These are SRAM-based powerful FPGAs that also need circuitry to mitigate the radiation effects in the SRAM cells. The companion chip fits next to the FPGA to provide the features that the customer needs, Dargnies says.
"We are moving from component supplier to a function and systems provider, by taking-on subfunctions that nobody wants to deal with, as a function. The customer always needs more computing performance, capacity, density, and radiation performance," Dargnies says.
Apogee Semiconductor is helping space systems designers blend COTS electronic components with some rad-hard parts in robust systems in a family of parts called RelBridge. "The idea is to give customers a bridge between using less radiation-hardened parts, but in a more robust system, Quiroz says.
"You take out the critical components, like the watchdog timer, which is a failsafe for the satellite," Quiroz says "We developed a stand-alone voter for our customers who are walking the tightrope between cost and reliability. You have three microcontrollers performing the same function, and before doing something critical to the satellite, two of the three have to agree. Otherwise, which components do you trust to do arbitration or voting? We have a single-event-immune voter, which is more cost-effective way of handling triple-mode redundancy, which costs less than rad-hard microcontrollers."
Rad-hard projects
This spring U.S. military researchers chose the Northrop Grumman Corp. Aerospace segment in Redondo Beach, Calif., and RadiaBeam Technologies LLC in Santa Monica, Calif., to develop new testing methods for radiation-induced single-event effects (SEE) of high-reliability next-generation electronics.
Northrop Grumman won an $18.1 million contract in April, and RadiaBeam won a $10.6 million for Advanced Sources for Single-event Effect Radiation Testing (ASSERT) project of the U.S. Defense Advanced Research Projects Agency (DARPA) in Arlington, Va. The 4.5-year ASSERT program seeks develop new capabilities for SEE testing of 3D heterogeneously integrated (3DHI) electronic components and circuits, and transform today's radiation-hardened electronics design process to enable rapid deployment of next-generation electronics for space and nuclear warfare applications.
Goals for Northrop Grumman and RadiaBeam include generating energetic particles with penetration as deep as 5 millimeters in silicon with high-radiation-relevant linear energy transfers and beam diameters of less than 0.2 microns. Northrop Grumman and RadiaBeam engineers will take-on one ASSERT program technical area for 3DHI radiation-hardened technologies which addresses two technical challenges: deep penetration depths in 3DHI components with space-radiation linear energy transfers; and charge tracks with fine spatial resolution. Proposals must respond to both technical challenges.
Radiation effects threaten electronic systems from three main natural sources: galactic cosmic rays; charged particles trapped by planetary magnetic fields; and solar particle events.
Emerging advanced electronics are complex and integrated than previous generations, and can combine digital, analog, and optical functions using 3D topologies and several material types. 3D components are expected to reach several millimeters in vertical extent with a complexity and level of integration that will make it difficult, if not impossible, to de-package and disaggregate into parts to perform radiation testing using current heavy-ion sources.
SEE testing of integrated components will require an irradiation source that provides a combination of multi-millimeter penetration depths, space-radiation-relevant linear energy transfers, and fine spatial resolution and control to provide the linear and angular precision necessary to probe sensitive areas and to isolate faults.
Current SEE testing is unable to meet all of these requirements simultaneously, necessitating new sources to qualify next-generation microelectronics for nuclear and space applications that require high reliability in radiation environments.
The process of testing with ion beams is slow and laborious, and problems worsen with the increasing complexity of electronics. As a result, ASSERT sources must be compact and cost-effective so they can be incorporated into the development process.
In this way, radiation qualification will be integrated throughout the design and fabrication flow, with ASSERT sources providing the means to identify radiation design flaws rapidly and to facilitate swift correction and design optimizations. A key program goal is to reduce the time from design to radiation-qualified component by a factor of 10. DARPA researchers particularly are interested in technologies like short-pulse relativistic electron beams and ultrashort pulse X-rays.
Rad-hard data storage
Last fall spacecraft experts at the U.S. Air Force Research Laboratory's Space Vehicles Directorate at Kirtland Air Force Base, N.M., announced a $35 million contract to Western Digital Corp. in San Jose, Calif., next-generation radiation-hardened non-volatile memory chips as part of the Advanced Next Generation Strategic Radiation hardened Memory (ANGSTRM) project.
ANGSTRM seeks to develop a strategic rad-hard non-volatile memory device with near-commercial state-of-the-art performance by using advanced packaging and radiation-hardening techniques with state-of-the-art commercial technology for space and strategic systems. The Air Force Research lab awarded the contract on behalf of the U.S. Space Force.
Advancing strategic rad-hard non-volatile memory technologies is critical to support strategic missiles, missile defense, and military space systems, researchers say. Non-volatile memory devices retain their data even when they lose power.
Ideally, the military would have access to non-volatile memories with the performance and density of commercial state-of-the-art devices; unfortunately today's commercial technologies are not able to withstand the radiation and thermal environments where the military deploys systems. Many military systems, moreover, must use trusted on-shore electronics manufacturing.
The U.S. Space Force researchers are interested in combining radiation hardening to state-of-the-art CMOS and memory technologies to scale density beyond the levels of a single chip, and create qualified strategic rad-hard non-volatile memory for use across military space and strategic systems.
Researchers want Western Digital to develop rad-hard memories with monolithic memory densities of 4 to 16 gigabits, and with multichip module densities of 32 to 128 gigabits that will last without refresh for 10 to 15 years. These memory devices should operate with no more than 10 milliwatts of power, and operate in temperatures from -40 to 125 degrees Celsius, and eventually down to temperatures of -55 C.
Resistance to total-ionizing-dose radiation should be as low as 300 kilorads, and as high as 1,000 kilorads, with fewer than 10 to 12 single-event upset errors per bit day. Single-event latchup resistance should be more than 72 MeV-Cm2/mg, with single-event gate and dielectric rupture of 72 to 100 MeV-Cm2/mg.
Ultimately, the ANGSTRM project seeks to develop a full-scale prototype device, provide device characterization and radiation test reports, and provide a qualification plan with a path to achieve a QML-standard product.
Space optical communications
Last February the U.S. Space Development Agency (SDA) in Chantilly, Va., released a broad agency announcement (FA240124S0001) for the Systems, Technologies, and Emerging Capabilities project to develop new kinds of space-based optical communications, navigation, target tracking, and similar capabilities for the warfighter.
The project is looking for new enabling technologies in efficient beyond line-of-sight data transport and warfighter communications; advanced and alternate position, navigation, and timing (PNT); advanced target custody, warning, tracking, and defeat; and global battle management -- most of which will require radiation-hardened electronics.
SDA officials are asking for architecture studies, concepts of operations (CONOPS), modeling and simulation, system designs, key technologies, and risk-reduction prototypes related to these capabilities. Efficient beyond line-of-sight data transport and warfighter communications features capabilities that enable global access to low-latency communications and space data transport for joint warfighting systems.
These capabilities involve enabling technologies in small lightweight free-space optical communications terminals that can operate at low, medium, and geostationary orbits and handle space-to-space, space-to-air, space-to-ground, and space-to-maritime applications. In particular, SDA experts are looking for emerging capabilities to improve modem performance, increase data rate, reduce optical communications terminals acquisition time through automation, and reduce complexity and manufacturing requirements.
Enabling technologies of interest include photonic integrated circuits; small lightweight terrestrial optical communications terminals; transportable optical ground stations; and simple low-cost ways to mitigate atmospheric effects on optical links.
Companies interested should email unclassified executive summaries and abstracts no later than 1 Dec. 2024, and full proposals no later than 15 Jan. 2025, to [email protected]. Email questions or concerns to [email protected]. More information is online at https://sam.gov/opp/f34e7a9d6f9d42008c7bf2874742316b/view.
Hotlink to company list of radiation-hardening companies:
https://www.militaryaerospace.com/search?filters={"text":"radiation-hardened","type":{"value":["Company"]},"websiteSchedule":{"value":[]},"page":1}&page=1
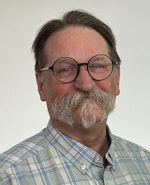
John Keller | Editor-in-Chief
John Keller is the Editor-in-Chief, Military & Aerospace Electronics Magazine--provides extensive coverage and analysis of enabling electronics and optoelectronic technologies in military, space and commercial aviation applications. John has been a member of the Military & Aerospace Electronics staff since 1989 and chief editor since 1995.