Military embedded computing on the verge of revolutionary new changes
The aerospace and defense embedded computing industry is on the cusp of some of the biggest changes in more than a decade, as board and backplane speeds are increasing, board dimensions are about to expand by including a new size, and small-form-factor embedded computing architectures are poised to move to credit-card-sized modules.
The VITA open-standards organization, which oversees the leading design standards for much of the world's embedded computing industry, is near finishing the most influential change since the VITA 65 OpenVPX standard was ratified in 2010.
Changes revolve around the emerging VITA 100 standard, expected to be ratified in early 2026, which has the potential to double I/O board and backplane connector speeds over OpenVPX, breathe new life into 3U and 6U embedded computing architectures, and add a new 4U standard board size to accommodate the relatively large sizes of state-of-the art microprocessors, field-programmable gate arrays (FPGAs), general-purpose graphics processing units (GPGPUs), and other high-performance components.
Yet these revolutionary changes to military embedded computing are not only about VITA 100. Designers of extremely small embedded computing designs for unmanned vehicles, handheld devices, manpack systems, and other lightweight designs are looking ahead to the VITA 74 VNX+ standard to determine how this standard's credit card-sized boards will influence extreme small-form-factor embedded computing.
VITA 100
The VITA 100 suite of standards, in development now, is an evolution to OpenVPX, VPX, and related mechanical standards while embracing a paradigm shift in technology and capability with at least double the pin density, speed, and power for electrical contacts.
The in-progress VITA 100 standard is expected to be ratified in early 2026, with some of the first VITA 100-compliant products expected to hit the market in late 2026 or early 2027. The VITA 100 baseline standard outlines the essential electrical and system architecture for the VITA 100 ecosystem. The VITA 100 working group is developing the draft standard document.
"Open VPX has reached the limit of its ability to pump data through the backplane," says Mark Littlefield, director of embedded products at Elma Electronic in Fremont, Calif. "Everybody has accepted that the RT 3 connector of Open VPX has reached its limit."
To help move embedded computing technology forward, VITA 100 is likely to put in place high-density connectors that roughly will double the throughput of OpenVPX connectors between boards and backplanes. "VITA 100 will double the pins on the backplane over the VITA 46 connector to provide twice as many high-speed connects," explains Aaron Frank, senior product manager at the Curtiss-Wright Corp. Defense Solutions segment in Ashburn, Va.
The improvements that VITA 100 promises are "getting the backplane to catch up," Frank says. What used to processing power-limited, now becomes I/O-limited. This will help get more data to and from the modules. This is the biggest area where we customers struggle with," Frank continues. "As we move to data center applications like artificial intelligence into embedded computing, they are hitting the bottlenecks of where OpenVPX is today." The I/O-doubling capabilities of the VITA 100 connectors will apply to all VITA-based embedded computing modules.
"VITA 100 will be a worthwhile next-generation platform," says Elma's Littlefield. "The Schedule is aggressive; they want it done and approved by ANSII by the end of next year. They could do it if they can keep the momentum up, but it is a lot of work for everyone involved."
New form factor
While VITA embedded computing standards typically call either for 3U- and 6U-size circuit boards -- with 3U the most prevalent -- the future VITA 100 standard also may accommodate a 4U-size card to fit modern high-performance processors.
VITA 100 will use the typical 3U and 6U size board formats, but a 4U size may be implemented, as well, which is new for the VITA and even the PICMG community," says Justin Moll, vice president of sales and marketing at Pixus Technologies Corp. in Waterloo, Ontario. "Driving to 4U mainly are concerns with the newer chipsets coming out for applications that you may not have the space and I/O that you need to achieve in a 3U card," Moll says, adding that some future high-performance applications that won't fit on a 3U, may find a solution in 4U, and not need to move all the way up to 6U.
If the future VITA 100 standard does accommodate 4U card size -- no guarantee of that yet -- "it will be the customer's performance demands will require it," Moll says. "They will want to have as compact an enclosure as possible, but want this higher-level performance that only can be achieved in that 4U size. There will be enough volumes in key programs that will drive that market."
It's unlikely that a standards body like VITA would embrace a whole new board form factor like 4U -- unless the market unequivocally was demanding it. "Today's electronics are getting more powerful, and chips are becoming larger," says Curtiss-Wright's Frank.
Components and FPGAs, GPUs, and processors are getting really big," points out Elma's Littlefield. The Ice Lake processor supports four banks of memory, but there isn't enough space for that on a 3U card. Then 4U is attractive to buy space for these big components."
Power consumption and thermal management also play into the equation. "There also is a big desire for high-power densities," Littlefield says. "with 4U we can get to 150 Watts per slot with air-flow-through cooling; conduction cooling is limited to 100 Watts. GPUs and FPGAs are big power-hungry components, and developers eventually want to see 200 Watts per slot, and there's no way we can do that on 3U."
Any move to a 4U board form factor would involve growing pains, experts say. "When you look at VITA 100, because the connector gets bigger with more pins, and the data throughput is 4 times what the Open VPX connector offers, the form factor changes to 4U," says Ken Grob, director of embedded technologies at Elma Electronic. "Then we need to go back and change all the reference backplanes, and development platforms will have to be updated."
So if implemented, how would the new 4U form factor influence the long-term viability of 3U and 6U cards? "I think 3U will be around for many decades; not every project is going to need the special requirements that a 4U board would facilitate," says Pixus's Moll. "I would expect it will be several years before 4U really will take off, and 3U will be the predominant size for a long time to come."
As for the 4U's influence on 6U embedded computing cards, 6U will certainly have its place as a subset of applications, but its use will remain smaller than 3U," Moll continues. Simply from a board real estate option, there are still a lot of applications where that 6U size is a must, such as applications that have a lot of RF or optical interfaces, or a combination of chip set options that require the real estate, like radar applications and C4ISR."
VNX+ standard
Another recent standard of note in the aerospace and defense embedded computing industry is VITA 90 VNX+, a credit card-size board that is designed to meet the growing needs for improved size, weight, and power consumption (SWaP) VNX+ uses a rugged, low cost, and fast serial fabric interconnect based plug-in module.
VNX+, while not offering the performance of VITA 100 3U, 4U, or 6U modules, primarily is for extremely small applications like smart missiles and uncrewed vehicles, in which 3U cards simply are too large. "I wouldn't call VNX+ a big impact yet, but it's coming really soon," says Elma's Littlefield.
How might the smaller VNX+ bode for 3U module demand? "I don't think the impact of VNX+ will be significant on dampening the 3U market, says Pixus's Moll. "If VNX+ takes off, it will be for applications that absolutely demand very small size, such as smaller UAVs, robotics, etc. The performance you get out of 3U OpenVPX is indispensable."
Adds Curtiss-Wright's Frank, "VNX+ has size and power limits that restrict its use to smaller entry-level processing systems. We are finding that consolidation of SWaP, they want to do more in less space, rather than less in less space. VNX+ has a place in the market, but not in high-performance high-density applications."
SOSA
The big topic in the military embedded computing industry of the past few years has been the Sensor Open Systems Architecture (SOSA), which seeks to enable rapid, affordable, cross-platform best practices for systems, software, hardware, electrical, and mechanical engineering. SOSA is intended to reduce development and integration costs for military capabilities and reduce time to field, and encapsulates fundamentals of the Modular Open Systems Approach (MOSA) design approach to develop embedded computing solutions for military applications that involve a unified set of sensor capabilities.
The Open Group in San Francisco, which administers the SOSA standard, published the Technical Standard for SOSA Reference Architecture, Edition 1.0, in fall 2021, and published the Technical Standard for SOSA Reference Architecture, Edition 2.0, Version 2 (Snapshot 2) in March 2024.
The latest SOSA snapshot includes features to expand support for electronic attack, signals intelligence, synthetic aperture radar, and infrared sensors applications like security services.
SOSA 2.0 also includes standards such as Modular Open Radio Frequency Architecture (MORA) V2.5 and Vehicle Integration for C4ISR/EW Interoperability (VICTORY) V1.10 to refine guidelines for SOSA module and interface functions to help enable interchangeable components for sensing.
The latest snapshot also addresses additional chassis connectors and the use of high-speed Ethernet and high-density fiber connectivity; software and hardware; electrical-mechanical interfaces; and business use-cases.
The snapshot provides guidance of what will become the technical standard for SOSA Reference Architecture, Edition 2.0, and was published to make public the direction of how SOSA is evolving.
A copy of the Technical Standard for SOSA Reference Architecture, Edition 2.0, Version 2 (Snapshot 2) is available online at https://publications.opengroup.org/standards/sosa/s241?.
For the most part, SOSA doesn't aim at creating a new standard, but instead seeks to incorporate as many accepted industry standards as possible, so as to avoid re-inventing the wheel and to use standards with which industry designers already are familiar. SOSA, for example, has adopted the OpenVPX standard of the VITA Open Standards, Open Markets trade association in Oklahoma City. SOSA has begun adopting the U.S. Army's Vehicle Integration for C4ISR/EW Interoperability (VICTORY) standard, industry experts say, and is expected to adopt additional standards in the future.
The spirit of SOSA reflects a desire to develop new standards only when necessary, and rely instead on established standards. "The SOSA mandate is to adopt, adapt, and develop," says Dominic Perez, chief technology officer at Curtiss-Wright Defense Solutions. "If they don't have to create something new, then don't, if they can pull in from existing standards. When it doesn't fit the use case, then they want to adapt and modify those existing standards."
The SOSA Consortium aims to create a common framework for moving electronics and sensor systems to an open-systems architecture based on key interfaces and open standards established by industry and government consensus to support aerospace and defense applications for manned and unmanned surface vessels, submarines, aircraft, land vehicles, and spacecraft. The goal is to reduce development and integration costs and reduce time to field new sensor capabilities.
"We are seeing continued adoption of SOSA in the market place, as part of MOSA adoption, flowing from the platform integrator through the primes, board suppliers, and systems suppliers," says Curtiss-Wright's Frank.
It's difficult to talk about military embedded computing these days without discussing SOSA. "A very significant portion of VITA-based opportunities have SOSA-aligned requirements," says Pixus's Moll. "That means that typically the speeds are 100 Gigabit Ethernet or faster, and they are supposed to have a SOSA-aligned chassis manager."
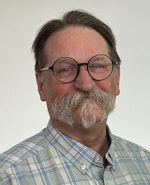
John Keller | Editor-in-Chief
John Keller is the Editor-in-Chief, Military & Aerospace Electronics Magazine--provides extensive coverage and analysis of enabling electronics and optoelectronic technologies in military, space and commercial aviation applications. John has been a member of the Military & Aerospace Electronics staff since 1989 and chief editor since 1995.