Lockheed Martin chooses design and development tools from The MathWorks for satellite channelizer development
NATICK, Mass., 2 May 2010.Satellite communications designers at the Lockheed Martin Corp. Space Systems segment in Denver needed design and development tools to design and test a dual-stage, satellite-based channelizer -- or bent pipe transponder. They found their solution from The MathWorks Inc. in Natick, Mass.
Many commercial communications satellites are limited to fixed-band plans that assign a bandwidth to users even if they are not using it, which is a inefficient use of communications capacity. Lockheed Martin developed the channelizer to move bandwidth on demand between users and locations.
Lockheed engineers designed and tested the channelizer using MathWorks tools for model-based design. “Simulink and Model-Based Design enabled us to visualize the operation of the system as it was running, and the model served as a golden reference for the hardware,” says Bradford Watson, staff engineer, advanced algorithm development group at Lockheed Martin Space Systems. “Additionally, EDA Simulator Link MQ proved invaluable for continuously verifying the accuracy and validity of the design and for troubleshooting any anomalous behavior observed in the hardware.”
Lockheed Martin needed to design a system that could be updated after launch, making FPGAs suitable for implementation. Designing a space-qualified system based on FPGAs was a challenge, however, because the system would be exposed to radiation in orbit, and FPGAs are highly susceptible to radiation upset.
Frequently changing requirements compounded the design challenge. “Early in the project, the band plans and the requirements for the system changed almost every day,” Watson says. “We needed a process and software tools that would enable us to implement a complex design and rapidly make changes as requirements evolved. We also needed to replace an inefficient and error-prone verification process that required importing and exporting text files and many other manual steps.”
Lockheed Martin engineers used MATLAB and Simulink to design, model, and simulate the digital channelizer. They then used EDA Simulator Link MQ and Mentor Graphics ModelSim to verify, analyze, and visualize the VHDL implementation in Simulink. Watson used MATLAB to develop algorithms for the channelizer.
As band plans changed, Watson parameterized the algorithms, enabling him to tailor variables to implement a new band plan in a matter of minutes. The ability to perform fast, iterative design changes helped to keep the project on track even in the face of ever-changing requirements.
A second Lockheed Martin engineer used Simulink to develop a hardware-like, full- system model of the digital channelizer based on the MATLAB algorithms. He used delay lines, interleavers, deinterleavers, and other blocks from Signal Processing Blockset and Communications Blockset to implement two stages of channelization and two stages of reconstruction, and to manage all the signals between them.
The team also used Simulink to build test-bench wrappers that included signal sources, such as simulated radio frequency/intermediate frequency (RF/IF) signals, and output analysis tools, such as buffered fast Fourier transform displays and spectrogram analyzers.
"The Simulink models documented the design, provided traceability, and enabled us to visualize the outputs of the system as it was operating," Watson says.
After implementing the design in VHDL, the engineers used EDA Simulator Link MQ and Mentor Graphics ModelSim to perform a final functional verification of the VHDL implementation at the bit level.
To minimize the effects of radiation upset, the system uses three identical channelizers and then "votes" on the results. Lockheed Martin engineers used EDA Simulator Link MQ to resolve complex reset condition and clocking issues in the voting system.
Watson used MATLAB to generate test vectors and post-process test results for hardware tests of the system running on Xilinx Virtex-II 2v6000 FPGAs. The digital channelizer has been successfully demonstrated in hardware, and is currently undergoing formal tests for flight certification.
This approach reduced verification time reduced by 90 percent. "Our system required precise timing. Troubleshooting our system without EDA Simulator Link MQ would have taken 10 times longer," Watson explains. "Being able to compare the implemented VHDL against the golden reference in Simulink is a real advantage."
Development time also was reduced by eight months. "With MathWorks tools and Model-Based Design I was able to focus on the algorithm work and higher-level system issues while another engineer focused on the VHDL implementation and verification," Watson says. "We had working code in four months, from start to finish, for a system requiring 5 million gates. Without MathWorks products, it would have taken us at least a year."
In addition, key algorithms reused, saving 50 percent of design effort on subsequent projects. "While the original band plan took four months to implement, we implemented two more in fewer than six weeks by reusing the existing design," Watson explains. "The channelization and reconstruction algorithms developed in MATLAB and Simulink are so flexible that I can use them anywhere. On a recent project, reusing those two functions saved 50 percent of the algorithm design effort."
For more information contact The MathWorks online at www.mathworks.com, or Lockheed Martin Space Systems at www.lockheedmartin.com/ssc.
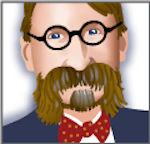
John Keller | Editor
John Keller is editor-in-chief of Military & Aerospace Electronics magazine, which provides extensive coverage and analysis of enabling electronic and optoelectronic technologies in military, space, and commercial aviation applications. A member of the Military & Aerospace Electronics staff since the magazine's founding in 1989, Mr. Keller took over as chief editor in 1995.