The world of radiation-hardened space electronics essentially falls into two camps: traditional space, which features the most costly, reliable, and long-lasting electronic components; and so-called “new space,” which capitalizes on commercially developed components adapted for space with low costs and limited life cycles in mind.
Traditional space has a relatively short list of suppliers, who have been in the radiation-hardened high-reliability electronics business for a long time. Historically it has been a small-but-stable market in which cost rarely is a driving concern, and high-reliability, longevity, and radiation hardness are driving factors.
New space, however, is a very different and quickly evolving animal. It seeks to lower costs, quicken design cycles, and capitalize on some of the latest electronic technologies, yet avoid any kind of over-design that could increase costs and slow development. New space components are designed to be just good enough for the intended application, and can feature relatively short life cycles.
New space represents an exploding market for future generations of large satellite constellations operating in low-Earth orbit (LEO), which hold the promise of blanketing the Earth’s surface with wireless voice and data communications, access to the Internet, and new kinds of Earth-observing sensor data.
Those involved in new space rarely are over-concerned with component longevity and flawless performance, because the relatively low costs of this market allow for on-orbit spare satellites. If one spacecraft fails or degrades, another one is ready to take its place.
Overall, these factors make for a volatile space electronics market that is more cost-sensitive than ever before, is experimenting with limited-life-cycle components in large constellations with on-board spare satellites, and yet with enduring need for long-term reliability and radiation hardness — especially in the higher orbits.Traditional space
Several companies specializing in radiation-hardened electronics have been in business for years. This market involves high-end systems for national defense, long-term NASA space missions, and high-revenue telecommunications.
Traditional space involves long-established government standards like the Defense Logistics Agency’s MIL-PRF-38535 — the U.S. military specification that establishes performance and verification requirements of single-die integrated circuit devices.
Although demand today has become relatively soft, applications still exist for the most radiation-hardened electronics parts, despite their typically high costs, lag in technology, and long wait times. The market for large expensive satellites that must operate in high geosynchronous orbits (GEO) is stable, but not growing, says Anthony Jordan, senior director of business development for Cobham Advanced Electronic Systems in Colorado Springs, Colo.
“The GEO market is soft, and has been so for the past couple of years,” Jordan says. “My sense is there is a little instability in the market where people don’t want to invest in a GEO satellite if these large constellations are going to work,” says Joseph Benedetto, president and CEO of VPT Components in Lawrence, Mass.
For the time being, however, the traditional space electronics industry is not seeing big changes — at least not yet. “The space market in general is incremental advancing,” Benedetto says. “There is a lot of discussion of new space small satellites, but that is not having a lot of impact on the traditional space market. All in all, we are not seeing any huge changes in the industry on what actually are selling.”
VPT specializes in some of the most stringently qualified space components, such as discrete components like transistors, diodes, and metal oxide silicon field effect transistors (MOSFETs). “Everything is qualified to JAN and JAN-S — the highest classification,” Benedetto says.Established suppliers
Among other providers of these parts for traditional space, which are designed from the ground-up to be radiation hardened, are the BAE Systems Electronic Systems segment in Manassas, Va., and the Honeywell Inc. Radiation Effects Center of Excellence in Clearwater, Fla.
The government also still needs systems that are hardened for weapons effects, such as the SBIRS [Space-Based Infrared Surveillance] system to monitor for weapons launches. The upcoming Global Positioning System (GPS) program to update the nation’s navigation satellites also will electronic components able to survive and operate through nuclear events.
Traditional space, despite its adherence to established designed and technologies, however, is not immune to modern electronics trends. Traditional space still faces increasing needs for ever-smaller and more power-efficient electronics, as well as demands for increasing amounts of on-board processing and high-performance computing.
“Where we used to see a lander or a rover, now we treat them as robots,” says Cobham’s Jordan. “We don’t want that human intervention because there is such a time lag. We just want them to go out and do their jobs and make decisions based on what they just saw and just sampled. Now we are talking about deep learning, machine learning, and artificial intelligence.”
This growing demand for capability — in applications typically that have involved technologies that lag behind the state of the art — put traditional space electronics suppliers in a squeeze; now they must provide the best of both worlds. “We are seeing more demand for higher-performance systems, neural networks at the FPGA [field-programmable gate array] or microprocessor level,” Jordan says. It’s all based on the results you need, and your power budget.”
This translates into demand for high-reliability radiation parts with the latest technologies. “We need more processors per square inch,” Jordan says. “We need A/D converters and D/A converters because I want sensors to be as close to the compute engine as possible — especially on digital communications payloads.”
The challenge extends beyond processing and data conversion, and includes power products. “We are seeing new product development focused on additional and improved power products, more distributed power, and more power-hungry components,” VPT’s Benedetto says. “10 years ago we saw more power management at the input level, and now we see it distributed so that power moves to the components and point-of-load regulators. We’re converting the power locally, rather than at one point on the spacecraft.”New space
In today’s space market, so-called new space is where the real action is. New space describes future large constellations of relatively low Earth orbit satellites with built-in redundancy and on-orbit spares to recover from spacecraft and system failures with few problems and at low costs.
Suppliers for new space applications often start with commercial off-the-shelf parts and alter them to enable the parts to tolerate the radiation and space environment for a limited amount of time, in the interests of relative low costs and access to some of the latest generations of computer technologies.
“We position ourselves as radiation-tolerant equipment for spacecraft in low-Earth orbit, and for launch vehicles that won’t be up there for too long,” explains Jerry Festa, program manager for space systems at the Curtiss-Wright Defense Solutions Aerospace Instrumentation segment in Newtown, Pa.
The challenges of today’s radiation-hardened components have discouraged spacecraft designers, and served as barriers to entry for traditional ruggedized COTS vendors like Curtiss-Wright.
“Radiation-hardened equipment has been expensive, and a lot larger than commercial technology,” Festa says. The space market, he says, “has kind of gone away from that — not for most of the critical systems, but for things that are not mission-critical, like instrumentation that could be lost momentarily, and no cause loss of life or loss of the mission.”
As for the future of traditional space, “the majority of those large GEO satellites are going to go away, replaced by large LEO satellite constellations,” Festa says. “You see it now, as people like Space-X are planning their constellations.”
Even traditional rad-hard electronics suppliers like Cobham are entering the new space market. Cobham is introducing the LeanREL family of radiation-hardened microprocessors, microcontrollers, memory, and interface integrated circuits (ICs) for small satellite and non-traditional spacecraft applications.
LeanREL ICs are for space-flight, military, and aerospace applications that need to operate and survive in harsh environments while remaining cost competitive.
Based on the same QML pedigree and silicon as the company’s HiRel solutions, Cobham’s LeanREL ICs can enable cost savings of as much as 60 percent, depending on quantities, to extend mission durations beyond that of typical off-the-shelf ICs and speed-up time to market for space applications through rapid prototyping.
Modified COTS for space
Curtiss-Wright offers design approaches that can accommodate space applications economically and with modern technology. “Where customers are worried about single-event upsets, we have a rad-hard backplane that goes on the back of stacks of data-acquisition modules,” Festa says. It has radiation-hardened components, but the modules are COTS. If you have an upset, the current usually spikes, and we monitor for that. The customer can program those limits, and the backplane resets the power to clear the latchup. The modules can survive as many as 120 latchups with no degradation.”
Mercury Systems in Phoenix takes a similar approach for the company’s space-qualified solid-state drives (SSDs) for data storage. “We use all components that are rad-tolerant by design, put them into the drives, and then build a space version of the product,” says Bob Lazaravich, director of secure storage at Mercury Systems.
Built-in redundancy is a key part of Mercury’s space design approach. “In space you need triple-redundancy to make sure it works for as long as possible,” Lazaravich says. “We use an FPGA that has all the gates triple-redundant.” The FPGA is the RTG4 from Microchip Technology Inc. in Chandler, Ariz. “That is the heart of our space drives now, Lazaravich says.”
Another step that Mercury has taken toward the space market is eliminating microprocessors entirely in their solid-state drives. “There is no C code at all on or drives,” Lazaravich says. “That adds an order of magnitude more reliability because you don’t have all those code bugs that can take years to detect and fix. Instead, we use VHDL code and tables to run our FPGAs.”
Would Mercury’s solid-state drives be appropriate for use in demanding geosynchronous orbits? Probably not; those environments do not represent the company’s target market — at least not today. “Right now we concentrate on terrestrial radiation environments and low-Earth orbit,” Lazaravich says. “We do resistance to 30 or 40 kilorads total dose for most of our boards. We will work out to other orbits and deep-space missions as we have customers serving those areas.”Radiation tolerant
Microchip also is eying the radiation-tolerant new space market. In April the company introduced an Arm microprocessor-based microcontroller that combines the low cost and large ecosystem of COTS technology with space-qualified versions that have scalable levels of radiation performance.
Microchip, with its recent acquisition of Microsemi, provides radiation-hardened and radiation-tolerant solutions ranging from high-performance FPGAs, precise frequency and timing solutions with space-grade oscillators, mixed-signal integrated circuits, isolated DC-DC converter modules, custom power supplies, hybrid and solutions, MOSFETs, diodes, transistors, and RF components.
The latest electronics design trends in new space applications are expected to endure for years to come. “Satellites have been getting smaller and smaller — and small satellites, rather than just being university experiments, have become much more capable,” says Anton Quiroz, CEO of Apogee Semiconductor LLC in Ache, Texas. “Not only government agencies, but also different prime contractors, are building more capable small satellites.”
Apogee is taking a multi-prong approach to keeping costs down for radiation-tolerant parts. “What makes semiconductors expensive is where you design and build them; the processes where you would build power and analog components are not inherently rad-hard,” Quiroz says. “We partnered with a commercial process foundry, and built a process design kit in that foundry.”
The kit is called TalRad, which is short for transistor adjusted layout for radiation. “We are building automated back-end systems to do 100 percent testing that the industry would like to see, and keep costs down by keeping touch points down,” Quiroz says.
Apogee focuses on analog, power, and mixed-signal devices for space applications. It’s been a great couple of years,” he says. “Demand for small satellites is continuing to grow, and I don’t see any signs of that slowing.”
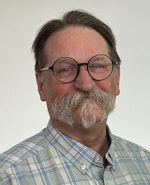
John Keller | Editor-in-Chief
John Keller is the Editor-in-Chief, Military & Aerospace Electronics Magazine--provides extensive coverage and analysis of enabling electronics and optoelectronic technologies in military, space and commercial aviation applications. John has been a member of the Military & Aerospace Electronics staff since 1989 and chief editor since 1995.