Modern aerospace and defense applications demand compact, high-speed, and resilient connector and cabling technologies.
The world is increasingly digital, interconnected, and driven by data. This trend, which shows no signs of slowing, is growing the demand for technologies that enable integration and connectivity - two essential characteristics of modern systems of virtually any size or scope. Current aerospace and defense projects emphasize the need for high-speed, lightweight, efficient, and resilient cables and connectors.
Smaller, lighter, faster
"The ability to acquire, process, analyze, and communicate information is important to the individual, state, and enterprise," says Ben Reed, general manager at Amphenol Fiber Systems International in Allen, Texas. "Because interconnect enables this communication, there is a continuous need for innovation to provide that link in new and evolving applications. This is particularly true given the increased demand for smaller, lighter, and faster."
High data rates are driving the introduction of optical fiber in applications where copper wire interconnect previously was sufficient, including harsh environments, Reed continues. "Fiber optics are required when data rates, distances, signal integrity, weight and security present challenges that cannot be solved with copper. Combined with a premium placed on mobility - which, by definition, often necessitates connectors - these requirements are driving innovation in fiber-optic interconnect."
When it comes to fiber-optic interconnects for harsh environments, the reliability of that connection often is the most pressing concern, Reed says. "Our customers spend significant time and capital to ensure a connection will work in their application. This often involves extensive design effort, as well as qualification either at the component or system level. Fiber-optic interconnect often is used for the most sensitive, critical signals. Ensuring the reliability of this signal is essential, especially in aerospace, defense, medical, and various industrial applications that rely on signal integrity."
Applications for harsh-environment, fiber-optic connectors and cabling include: battlefield networking, radar systems, missile defense systems, oil and gas drilling, underground mining, entertainment broadcasting, medical systems, and in-flight entertainment, to name a few, Reed says. "Anywhere that requires high data rates over significant distance or with weight, security, or electromagnetic interference (EMI) concerns can benefit from, or may require, fiber."
Aerospace and defense applications are switching from copper to fiber for high-speed transmission, space savings, and security, says Jeremy Ruff, director of business development at Amphenol Borisch Technologies and Amphenol Griffith Enterprises in Providence, R.I.
EMI protection
Relatively old Qualified Products List (QPL) solutions are not meeting EMI protection requirements, explains Eaton Interconnect and Power Communications Manager Dennis Brondi in Camarillo, Calif. "For example, MIL-DTL-55181 QPL power connectors were designed over 30 years ago when there was a much lower density of electronics equipment, including radios, and less breadth of transmission frequencies and electronics component operating frequencies that need to be protected against when compared to today's military vehicles.
"The original MIL-DTL-55181 QPL design contributes to today's EMI-protection problems because it only provides incidental shell-to-shell grounding continuity," Brondi continues. "To reduce the electrical resistance through the shell-to-shell interface, Eaton is introducing MIL-DTL-55181 power connectors with patented conductive-insert arrangements (U.S. patent #9437979 B2, published 9/6/16). Incorporating conductive inserts, instead of adding grounding pins facilitates backward compatibility with the large installed base of MIL-DTL-55181 power connectors, albeit mating receptacles, plus both need conductive inserts to facilitate lower-resistance ground paths."
Mobile missile-defense systems and artillery are key applications, requiring connectors that facilitate accelerated set-up times, provide exceptional EMI protection, and withstand high levels of shock and vibration. To meet these requirements, Eaton's MIL-DTL-38999 Series IV connectors incorporate 360-degree grounding fingers that reduce shell-to-shell electrical resistance and improve electromagnetic and radio-frequency interference (EMI/RFI) protection, Brondi says.
"Connectors must have 360- degree electromagnetic compatibility (EMC) screening, and the distance between differential electrical pairs must comply to certain rules in order to prevent cross talk, information loss, or signal degradation," says Serge Buechli, marketing manager at LEMO Connectors in Ecublens, Switzerland. LEMO provides an Ingress Protection (IP68) Push-Pull connector that complies with CAT6A, a robust solution for instrumentation, he adds.
Easing the weight burden
Weight is a key concern with virtually any aerospace and defense application, particularly when it comes to airborne and soldier-borne systems. Engineers endeavor to remove weight without sacrificing system capabilities, functionality, or availability. Even ounces can make a considerable difference.
The commercial aerospace world is pushing connector and cabling innovations faster than the military market, which is more conservative in its approach, says Mike Savage, director of product management at ITT Cannon in Irvine, Calif. "Commercial aerospace is pushing the limits more and more aggressive to drive weight out. In the commercial aerospace market, weight translates directly to dollars."
Savage is seeing growth in and is highly focused on soldier modernization, munitions, commercial in-flight entertainment (IFE), and avionics. "With commercial airplanes, weight is the biggest concern. In the military soldier modernization world, weight is everything," Savage explains.
With an emphasis on saving ounces at a time, ITT Cannon product engineers have "taken a lot of proven circular connectors and made them smaller using different materials, including high-speed friendly and lighter insulator materials," Savage says. "Stainless steel was used in the past for durability, but applications are moving to lighter materials like aluminum. We are constantly looking at new materials and processes, driving technology and innovation to make connectors perform" precisely how customers need."
One strong application area for lightweight composites is commercial aerospace. "Composite material offers significant weight savings when compared to aluminum and steel," explains Amphenol's Ruff. The company now provides composite connectors and backshells, as well as cable clamps known as P-Clamps, which not only weigh less than steel alternatives but also are easier and faster to install, he says.
Designed to disconnect
The warfighter's biggest connector concerns are weight and durability, and the biggest challenge relates to the ability to submerge electronics, connectors, and cables in 20 meters of water, Savage says. ITT Cannon offers submersible versions of the company's Nemesis connectors to meet this need.
In many cases, aerospace and defense applications need a break-away connector, Savage says. If a cable on a soldier's vest snags on a tree, for example, users want it to disconnect without damage to the connector or injury to the warfighter. Different military and aerospace systems designers want separate unmating force in break-away conditions, he says.
"Interconnects designed to disconnect include connectors with integrated release mechanisms that automatically de-mate to facilitate separation of launch vehicles from gantries, in-flight separation of propulsion stages, and separation of satellites and payload modules from propulsion stages," says Eaton's Brondi.
Eaton's umbilical connectors and in-flight disconnects, which include integrated actuators in mechanically and electrically initiated configurations, facilitate separation redundancy through any combination of mechanical lanyard release mechanisms or electrical pin-puller initiators.
Eaton's separation mechanisms incorporate non-explosive initiators that do not require the explosive material handling precautions associated with pyrotechnic initiators. The use of non-explosive initiators is beneficial for applications such as separating payloads from upper propulsion stages of space launch vehicles.
Diameter demands
"In aerospace and defense applications, there is typically a requirement that the smallest American wire gauge (AWG) that can be used is a 24 AWG stranded conductor," says Robert Moore, senior principal engineer at TE Connectivity in Redwood City, Calif. "Size and weight constraints on newer platforms have pushed that down to 26 AWG, but as the conductor size decreases, the maximum run length - for example, Ethernet - also decreases.
"In order to survive the aerospace environment, the conductor size is typically larger than what is used in commercial applications," Moore continues. It enables longer runs "as long as the AWG of the power line components allows for maximum voltage drop over a longer length and the time delay for the data pair still falls within the data standard requirement," he says.
Aerospace engineers seek small- er and smaller conductor sizes for Ethernet for satellite applications, where weight has a significant impact on launch costs, Moore explains. Cable designs sometimes conflict with the larger conductors required by the customer or application and the need to use standard commercial connectors that have been designed for small conductors and "short" runs, he adds.
"One of the biggest challenges that I have had to meet is limitations on component diameters and the ability to be compatible with a previously chosen connector," Moore says. "For the most part, it results in a slight modification to an existing construction and gives the customer a unique design." A growing number of aerospace and defense applications also call for data cables that will be reeled and de-reeled, prompting Moore and his colleagues at TE Connectivity to configure the components in the cable not to kink or break during the expected lifespan of the cable.
"The cables and connectors that we design and specify have to meet significantly more severe environments than the commercial equivalents," Moore says. "Whether it is temperature extremes, altitude extremes, high electromagnetic interference environments, fluids, or mechanical requirements, the products have to perform in those environments on a daily basis without issue, otherwise mission readiness is compromised."
Enduring the elements
Aerospace and defense connectors and cables need to withstand a wide variety of harsh environments, including extreme temperatures, shock, and vibration.
"If a connector dislodges in mud, warfighters want to be able to wipe off the front of the connector and mate it again," says ITT Cannon's Savage. For such occasions, ITT Cannon recommends changing from pin-and-socket interconnects to spring-loaded contacts on a pad to be more readily field-capable.
Traditional couplings will unmate under high stress and vibration, Savage says. For these challenging environments, ITT Cannon engineers designed the company's K-Lock coupling system, which he says is "next to impossible to unmate under high vibration."
Aircraft engines are particularly harsh environments that present cable and connector designers with unique challenges. "As aircraft engines move to higher bypass ratios to improve efficiency, it forces cables closer to the engine," Amphenol's Ruff says. "We are seeing an increased need for high/low-temp applications in space and on aircraft engines, where connectors and cables are exposed to high temperatures." Nomex braiding on cables helps address high temperatures.
Amphenol engineers recently worked with an aircraft engine manufacturer working on new engines for commercial aircraft. "On each engine, they would manually place hundreds to thousands of thermocouples to monitor the engine during test. The thermocouples could not be installed until the full engine was assembled. Placing the thermocouples took hundreds of man hours," Ruff says. "In an effort to solve this problem, we developed special thermocouple contacts and 'connectorized' the assembly. It allowed the engine to be built in sections and easily assembled/disassembled with the quick turn of a coupling nut - saving hundreds of hours in assembly and significantly accelerating the development cycle."
Providers offer connector solutions designed to help facilitate testing without sacrificing more costly equipment. ITT Cannon's Connector Savers, for example, help keep connectors on expensive equipment from wearing out quickly. During the test period, the connector is subjected to high mating and unmating, Savage says. "Customers may build and need to test a unit, but want to save the connector from multiple unmating cycles. We build a Connector Saver used only for testing that they can throw away."
Cabling and connector characteristics
Aerospace and defense customers today take into consideration a wealth of connector and cabling characteristics, in addition to size, weight, mating, materials, and EMC.
"The finish of the connector is important," ITT Cannon's Savage insists. Warfighters on the ground "can't have a shiny, bright connector; they need a matte finish dark enough to not reflect light. New plating materials and processing enables a move away from cadmium plating in soldier and avionics" applications.
The Reduction of Hazardous Substances (RoHS) directive restricting the use of hazardous substances in electrical and electronic equipment is still a concern. "A big challenge right now is getting complaint to RoHS. It is difficult to get lead out of base materials and plating materials, which are traditionally cadmium and lead," Savage says. The global military community is "still challenged with finding plating materials that perform but still hit a price point."
Accelerated schedules also influence cabling and connector selection. "Many customers are working to bring products to the market as quickly as possible," Amphenol's Ruff says. "To support this effort, we have invested in a three-dimensional (3D) printer which allows us the ability to do fit checks, build demo components such as backshells, and even cold pour molds to offer initial proof of concept assemblies within 48 hours."
Aerospace and defense organizations also are under increasing cost pressure because of competition and other factors. The use of off-the-shelf components and outsourcing produces more competition in the supply chain, Ruff adds. Amphenol's global footprint includes low-cost manufacturing locations in Mexico, India, and China.
Obsolescence management is another major concern in aerospace and defense. "Sourcing specialists continually monitor for obsolescent parts and work to identify issues before it has an impact to schedule," Ruff says. "Prior to notifying a customer, our in-house engineering team will investigate and provide equivalent alternatives when possible."
Miniaturization matters
The continuing trend toward smaller sizes is driving component miniaturization. "Miniaturization is the basis for a vast range of products and applications in areas such as defense, communications systems, homeland security, biomedical equipment, medical diagnostics, industrial, and consumer products," says LEMO's Buechli. "This kind of trend also applies to connectors, in the same way it has for integrated circuits during the last 50 years."
Smaller platform and system sizes, including the need for portability and mobility, are driving the migration from legacy MIL-DTL-38999, MIL-STD-5015, and MIL-DTL-26482 connectors to smaller, higher-density versions, such as 2M Micro-Miniature 38999, HD38999, Pegasus, and Micro-D connectors, Amphenol's Ruff explains. "New smaller connectors offer weight and space savings while maintaining the same level of performance. For example, a 2M series connector is 52 percent smaller and 72 percent lighter than its equivalent D38999 counterpart."
"Military original equipment manufacturers (OEMs) often are specifying compact form factors that connect both power and data with higher contact densities and equivalent or better performance than MIL-DTL-38999," Eaton's Brondi says. To address miniaturization requirements, Eaton micro-military circular connectors are available with as small as 0.39-inch receptacle diameters and integrated backshells.
High speed and density
"Connectors need to be designed for higher speeds," says Mike Walmsley, global product manager for aerospace and defense at TE Connectivity in Harrisburg, Pa. The VITA 46 connector was initially rated for 6.25 gigabits per second (Gb/s) but is now used in 10 Gb/s applications, he says. "As we move to 16 Gb/s and 25 Gb/s, the connector footprint and structure has to be studied and further developed to minimize sources of noise and impedance discontinuities.
"For smaller platforms, higher- density connectivity is needed - more high-speed signals, more radio-frequency (RF) lanes, and more optical links in the same module space, narrower guide hardware," Walmsley continues. With standard platforms, he says, the available space is defined and the challenge is pushing more throughput within that same physical space constraint.
Higher data rates are coming quickly in the military and aerospace market, processors are making significant gains, and applications demand faster data processing and transmission, Walmsley says. Electronic-warfare (EW) programs require high-speed digital (board-level), RF cabling, and other connectivity solutions, for example.
"Industry leaders are looking ahead two generations for data rates, and we are developing solutions now. With a widely accepted industry standard like VPX, the significant challenge is addressing the higher speeds with a solution that is backward compatible with existing architecture (same mating interface)," Walmsley adds.
"In defense, we are seeing an exciting evolution in interconnect technology. Old architecture is being upgraded with new, for higher speed and density. Open standards are being driven to reduce cost and development cycles. No longer are the old designs from 20-plus years ago being re-deployed," Walmsley says. "This invites new technologies and innovative solutions for connectivity."
Dissipative ETFE dielectric polymer helps control electrostatic discharge in wires and cables
BY Chris Yun, principal engineer of aerospace, defense, and marine at TE Connectivity
Controlling static electricity in electrical interconnection systems is essential in spacecraft where electrostatic discharge (ESD) events can damage electronics and scuttle the mission. It has been reported that 54 percent of spacecraft anomalies/failures are caused by electrostatic discharging and charging.
In April 2010, for example, the Galaxy 15 telecommunications satellite wandered from its geosynchronous orbit. Reports suggest that spacecraft charging caused the anomaly. Fortunately, a workaround allowed the mission to continue. Worse off was the Advanced Earth Observing Satellite 2 (ADEOS-II), which lost power in October 2003. Forensic research identified that charging by high-energy auroral electrons was followed by a discharge event between power cables. The satellite was never recovered.
An electrostatic charge can build up in any kind of wire and cable insulation. On Earth, a material can become e- lectrically charged when electrically dissimilar materials rub together. In wires and cables used in spacecraft, a static charge can be created by the impact of charged particles on the material. Space is filled with charged particles that can induce a charge in materials. Satellites in geosynchronous orbits and deep space missions are particularly susceptible because of higher charge density in GEO and deep space.
The use of high-resistivity dielectric materials and electrically separated surfaces in conjunction with the connected conducting surfaces of the spacecraft frame promote various forms of spacecraft charging. When the charge builds up in wire and cable of electrical interconnection systems, a sudden discharge can damage connected logic circuits, electronic instruments, and computer chips.
The primary factors that determine the speed and size of an electrostatic discharge are the material's ability to hold a charge (capacitance) and its ability to reduce the flow of electrons (resistance).
There are two ways to handle these factors in wire and cable. One solution employs metallic shielding to create a path that promotes electron flow, which dissipates the charge. The other strategy is to make the insulating materials dissipative, which suppresses the charge build-up.
Read the rest of the exclusive Intelligent Aerospace article by TE Connectivity (www.te.com) at http://bit.ly/2oNzDTr.
MIL-STD-1553B in avionics
The landscape of avionics architectures has shifted through the decades from analog to digital system implementations with increased software complexities. As the subsystems of the aircraft grow, so do the complexities in the communications between them. Speed, reliability, safety, cost, and quality of service are all factors that are taken into consideration when choosing a particular data networking standard. The present evolution in technology and data networking - of which MIL-STD-1553B has been and is still a major component - offers a wide variety of options for modern day aircraft.
Increased data throughput requirements for high-definition video and camera services far exceed what MIL-STD-1553B theoretical maximums are, approximately 200 megabits per second. Efforts have been made to provide enhanced speed MIL-STD-1553B, which may still serve some purposes on commercial aircraft. Moreover, technologies such as Ethernet, are more likely to succeed in meeting the latest throughput demands of commercial and, possibly, military avionics.
Read the rest of the exclusive Intelligent Aerospace article, by MilesTek (www.milestek.com), online at http://bit.ly/2oXa6pr.
Company List
Amphenol
Wallingford, Conn.
www.amphenol.com
Carlisle Interconnect Technologies
St. Augustine, Fla.
www.carlisleit.com
Delphi
Washington
www.delphi.com
Esterline
Bellevue, Wa.
www.esterline.com
Fischer Connectors
Alpharetta, Ga.
www.fischerconnectors.com
HIROSE Electric
Downers Grove, Ill.
www.hirose.com
ITT
Cannon Irvine, Calif.
www.ittcannon.com
LEMO USA
Rohnert Park, Calif.
www.lemo.com
MilesTek
Denton, Texas
www.milestek.com
Molex
Lisle, Ill.
www.molex.com
ODU-USA
Camarillo, Calif.
www.odu-usa.com
Omnetics Connector
Minneapolis
www.omnetics.com
Pasternack Enterprises
Irvine, Calif.
www.pasternack.com
Smiths Interconnect
Stuart, Fla.
www.smiths.com
TE Connectivity
Berwyn, Pa.
www.te.com
TT Electronics
Perry, Ohio
www.ttelectronics.com
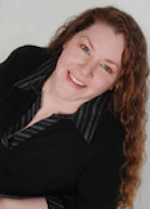
Courtney Howard | Executive Editor
Courtney, as executive editor, enjoys writing about all things electronics and avionics in PennWell’s burgeoning Aerospace and Defense Group, which encompasses Military & Aerospace Electronics, Avionics Intelligence, the Avionics Europe conference, and much more. She’s also a self-proclaimed social-media maven, mil-aero nerd, and avid avionics geek. Connect with Courtney at [email protected], @coho on Twitter, and on LinkedIn.