Demand for access to space — for communications, surveillance and reconnaissance, remote sensing, internet access, and space experimentation — never has been higher than it is today, and is expected to grow through the foreseeable future. Satellites are under construction ranging in size from softballs to 18-wheel tractor-trailer rigs, as potential sponsors ask for high performance, relatively low costs, and quick turnaround.
As this demand puts advanced electronics at a premium for space, there still are environmental constants that no one can change. Chief among these is the radiation that occurs naturally in space. Orbiting electronics must be able to withstand bombardment of radioactive particles at different levels, based on their intended orbits. This means that today’s space electronics must be high-performance, radiation tolerant, and affordable.
While some semiconductor designers have found ways to alter commercial electronics designs to boost their radiation tolerance, there still are established integrated circuit manufacturers with long histories of designing special radiation-hardened parts for the most demanding space applications.
It all boils down to balancing requirements for electronics performance, costs, mission durations, and the radiation environment of chosen orbits. Low-Earth (LEO) orbit, for example, can be among the most benign space environments for radiation. High-altitude geosynchronous Earth orbit (GEO), on the other hand, can be among the most severe. High-altitude polar orbits can be the harshest radiation environments of all.
Low-cost parts
One of the biggest applications drivers in today’s space electronics market is so-called “new space,” which describes commercial endeavors to create large constellations of inexpensive small satellites for uses like cell phone communications and internet access. In this market cost is king. In addition, requirements for resistance to orbital radiation effects often can be relaxed because of relatively short mission durations.
“Radiation hardened and radiation tolerant are two different things,” explains Jerry Festa, space product line manager for the Curtiss-Wright Corp. DefenseGoing with radiation-tolerant, rather than pure commercial parts, in space applications has its price. Radiation-tolerant parts typically cost about five times the cost of the COTS parts on which they are based. Still, they are far less expensive than radiation-hardened-by-designed parts, which sometimes can be 100 times the price of pure commercial parts.
“Cost is a factor, and some applications are willing to live with less reliability, where it might be acceptable to lose one percent of your data over a mission,” Festa says. “There is room for both.”
New-space applications, in particular, are sensitive to parts costs. “We are seeing with the small-satellite and new-space markets a trend toward trying to qualify COTS components due to their being less expensive than the full-up rad-hard design,” says Malcolm Thomson, president and general manager of Radiation Test Solutions Inc. in Colorado Springs, Colo.
“This is driven by cost per kilogram, and reduced mission lengths,” Thomson says. “A lot of the new players are launching LEO constellations with hundreds or thousands of satellites with five-year mission lengths. That drives the need for radiation tolerance that costs less. It’s a simple matter of economics: if they could afford to build thousands of satellites at millions of dollars each, they probably would do that, but they can’t.”
The market for affordable radiation-tolerant parts is so promising that even some of the industry’s longtime rad-hard-by-design companies are plunging in. Enter Renesas Electronics Corp. in Milpitas, Calif., which through acquisitions assumes the legacy of rad-hard stalwarts Harris Semiconductor and Intersil.
“We are continuing the convergence of compromise in the interest of cost, and still meeting our reliability requirements,” says Josh Broline, director of marketing and applications at the Renesas manufacturing center in Palm Bay, Fla. “We launched a low-cost radiation-tolerant plastic package integrated circuit a few years ago. We are coming out with solutions that are in the middle, to give some cost savings, yet still with the reliability that space designers need.”
A key consideration for designing affordable radiation-tolerant parts is where to make the compromises, Broline says. “We don’t necessarily have the NASA processor or FPGA [field-programmable gate array], but we have the power management that has to power those systems reliably. We need to have robust solutions, and our engineers are trying to figure that out.”
Test and enhancement
Among the approaches for producing space electronics components that blend affordability and capability is screening and testing to uncover those commercial-“We are on the test side, and can upscreen or do any value-add for the customer,” says Marti McCurdy, owner and CEO of Spirit Electronics in Phoenix. “We offer a high-value proposition, and only operate in the mil-aero sector.”
Sprit Electronics experts take their direction from their customers, who are trying to match anticipated operating environments, orbits, and mission durations with the most appropriate technologies. “We take a non-radiation-hardened component, because the customer doesn’t want to invest in that kind of a product,” McCurdy says. “We do screening and qualification to MIL-STD-883 Group E, and we do this as a service and as an add-on to drive our test floor.”
Matching technologies to operating environments is a core part of their business. “We screen for application-specific use,” McCurdy says. “We have somebody with launch equipment, and their mission might be 10 minutes. They could have four times the redundancy in parts, and still save a lot of money. When we talk about screening, it really is about how much insurance do they want? We can calculate the risks of 10 minutes of exposure to space radiation.”
The radiation test industry also is seeing a transition from parts-level to systems-level testing. “In the test world, we are starting to move away from component-level and into the systems world,” McCurdy says. “The commercial world has been in this area for a few years now, and the aerospace and defense market is just getting there now.”
As far as their customer base is concerned, McCurdy says demand for space electronics appropriate for low-Earth orbit is dominating, but needs for higher levels of radiation tolerance for higher orbits are not going away. “LEO is captivating the market, but GEO is still out there. There is a fine line between customers doing radiation tolerance, and the commercial companies putting up a constellation of tens to hundreds of satellites that are doing data mining. It’s all about data collection.”
For some commercial space companies considering short-duration missions, the risk might be worth it to have no radiation hardness or upscreening at all. When every dollar and every ounce of weight count, then using pure-commercial parts has its benefits. Experts say that commercial space is so new that reliable models of risks of on-orbit failures have yet to be crafted.
“Our specialty is in radiation testing,” says Radiation Test Solutions’s Thomson. “In new space we see companies that do radiation testing. We have seen a lot of growth because we are qualifying commercial parts to see how radiation tolerant they are. You don’t really know until you test.”
This kind of testing can be the key to balancing on-orbit capability and risk. “You have a lot of very large technology companies, such as social media companies, competing in this game that still need radiation testing to deploy a reliable constellation of satellites,” Thomson says. “They can select from a much larger set of components than can traditional spacecraft manufacturers. They may evaluate five or six different memory manufacturers to see which one might meet their mission requirements.”
Build to suit
For some space missions, simply testing for radiation tolerance is not enough; sometimes enhancements are necessary. “In some cases we have value-add,“Our approach seeks to improve radiation with the combination of hardware and software. The hardware approach starts from existing silicon, and we add screening and qualification. What is new is we add a layer of software on top of the hardware layer, and a hardware intelligent memory controller.”
The combination of software implemented in an FPGA and radiation-tolerant memory controller, perform error correction such that “we qualify the hardware, and the software makes it immune to single-event upsets,” Dargnies says.
Curtiss-Wright also is involved in systems enhancements to improve radiation tolerance for space. “There are several ways you can make a design radiation tolerant to single-event latchups and single-event upsets like a bit flip,” explains Curtiss-Wright’s Festa. “There’s no way to determine when a single-event effect will occur; you have to correct for these issues.”
One way that Curtiss-Wright engineers mitigate single-event latchups is the company’s Smart Backplane, which has parts designed for radiation hardness for critical functions such as monitoring for power changes to embedded computing modules. The company’s Smart Backplane mitigates single-event latchup by detecting changes in the current into an embedded computing module. If that current drifts out of its present range, then the system resets the power to that module, and in so doing clears the memory and any lingering single-event latchup.
“We use FPGAs, so the reset is very quick,” Festa explains. You only lose one second of data in each module. The Curtiss-Wright Smart Backplane has beenRadiation tolerance also is becoming an issue for commercial passenger and cargo aircraft that must operate at high altitudes for long-duration flights. In these applications charged particles can be as much of a threat as they are in space.
Curtiss-Wright engineers have found that today’s commercially developed multicore processors are particularly well-suited for radiation tolerance in commercial aviation. “In our air data product the chip geometries are very small and might be susceptible to a single-event upset,” explains Paul Hart, Curtiss-Wright’s chief technology officer for avionics products.
“For every layer of execution there is a comparison,” Hart explains. If there is a difference, you could surmise that a single event has occurred, and then you would do a memory self-test. We can have strategies to have duplicate cores, and instead of having a compare function for every line of code, you would have a comparison for every parameter you are running. This is a factor of high-criticality in avionics for passenger aircraft, so you need a mitigation strategy — particularly when using fly-by-wire systems.”
Demanding applications
For many demanding space applications — particularly those intended for high orbits and long-duration missions — upscreening and enhancements doesn’t fit theIncreasingly, these applications also require some of the highest capabilities available in electronics. “We need spacecraft that can control themselves so they don’t crash into other satellites, and to reposition themselves for communications. For this we have a need for artificial intelligence,” says Paul Armijo, aerospace and defense business sector manager at GSI Technologies Inc. in Sunnyvale, Calif.
“We have developed an AI chip for space that is radiation tolerant to enable artificial intelligence, data fusion, automatic target recognition, and for recognizing weather events.” The AI chip is single-event latchup immune to 100 kilorads of total-dose radiation exposure.
Today’s sensor-intensive satellites require a lot of on-board processing because satellite uplinks and downlinks simply do not have the bandwidth for exchanging so much data with ground stations. “Satellites have so many sensors that it becomes untenable to push that data down to Earth, process it, and then tell the vehicle what to do,” says GSI’s George Williams, the company’s director of data science. “That data could be optical imagery or synthetic aperture radar; these are massive data sets.”
Demands for increased processing power on orbiting satellites will continue to grow, Williams says. “Five or ten years ago it became so easy and cheap to store data, but the challenge remains of making that data actionable. That has ushered in this new age of AI and machine learning. We need to take a data-driven approach to getting at that data.”
It’s a never-ending appetite for computing power among satellite systems integrators. “Satellites are getting smaller, and need high performance,” says Anton Quiroz, CEO and co-founder of Apogee Semiconductor LLC in Plano, Texas.
Apogee manufactures radiation-tolerant as well as radiation-hardened electronics components. The company offers radiation-hardened complementary metal oxide semiconductor (CMOS) products, and is applying some of those rad-hard processes to commercially developed electronic components for radiation tolerance.
“We have been able to release a new family of components by leveraging commercial foundries to make them radiation tolerant,” Quiroz says. “We can mix 5-volt parts with newer parts, and we need a part that bridges the gap between the old technologies and new technologies, between 1.8-volt parts and 5-volt parts. In that product family is a voter,” Quiroz continues. “Even though it has triple-redundancy, we still need a rad-hard part that will vote on what is going on.”
Apogee engineers have developed the ability to fine-tune the radiation-tolerance levels of their company’s components, which helps the company serve a wide variety of radiation needs. “We have parts that are capable of 30 kilorads total ionizing dose performance, but we are developing a 300-kilorad part for the government geosynchronous market,” Quiroz says. “It doesn’t change the design difficulty too much. We can hit the standard geosynchronous levels; if you can hit the government market, you can hit the commercial market.”
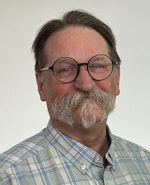
John Keller | Editor-in-Chief
John Keller is the Editor-in-Chief, Military & Aerospace Electronics Magazine--provides extensive coverage and analysis of enabling electronics and optoelectronic technologies in military, space and commercial aviation applications. John has been a member of the Military & Aerospace Electronics staff since 1989 and chief editor since 1995.