Advanced hypersonics munitions and aircraft: industry shows it's up to the challenge
Developing enabling technologies for hypersonic flight -- or the ability to move at speeds of Mach 5 or faster -- is one of the highest research priorities at the U.S. Department of Defense (DOD). The pressing need for hypersonics comes from a perception that the U.S. military may be behind Russia and China in developing hypersonic technologies, so defense officials are all-in on research and development to bring this about.
There's good reason for the attention. Hypersonic munitions are unlike any other weapon, in that they can move at Mach 5, or even faster. The central issue is warning time; a missile traveling at five times the speed of sound is going about 3,800 miles per hour.
That's more than a mile per second. Target a ship at sea from 100 miles away with such a hypersonic missile, and that ship's crew has less than two minutes to detect, identify, and track the incoming missile, and then bring defensive weapons to bear and fire. Count to 105, and that's all the time that ship has to defend itself -- only if it has sufficient sensors and weaponry, and only if everything works right.
A hypersonic missile traveling at Mach 5 could reach a target 20 miles away in about 21 seconds. It would take a subsonic anti-ship missile more than four minutes to land an attack from 20 miles away. Viewed in these terms, hypersonic munitions are the weapons of the future.
Hypersonic development
There are a wide variety of high-visibility DOD projects to develop hypersonic technologies. Some of these projects involve propulsion to accelerate munitions and aircraft to speeds approach Mach 25, or 19,181.7 miles per hour. Some involve lifting bodies able to sustain those kinds of speeds without disintegrating, and some involve ruggedizing electronic and electro-optical components and subsystems to operate through the extremes in shock, vibration, and heat of hypersonic flight.
The Hypersonic Air-breathing Weapon Concept (HAWC) of the U.S. Defense Advanced Research Projects Agency (DARPA) in Arlington, Va., is developing technologies for a scramjet-powered hypersonic air-launched cruise missile project. In tests, the scramjet propelled the missile faster than Mach 5, or about 3,300 miles per hour.
HAWC technologies are expected to go into future hypersonic production missiles to be carried aboard aircraft like the B-1 strategic bomber, the F-25 joint strike fighter, and perhaps even the F/A-18 jet fighter-bomber. Successful HAWC test flights happened in 2021, 2022, and 2023.
Lockheed Martin Corp. in Bethesda, Md., is leading several hypersonics research and development projects. Programs under contract include:
-- the U.S. Air Force's Air-launched Rapid Response Weapon (ARRW), which combines critical high-speed flight technologies and accelerates the weaponization of air-to-ground hypersonic strike capabilities;
-- the U.S. Navy's Conventional Prompt Strike (CPS) weapon system and the U.S. Army's Long Range Hypersonic Weapon (LRHW), which use a common hypersonic all up round; and
-- the U.S. Navy's Hypersonic Air-Launched Offensive Anti-Surface Warfare (HALO) system.
CPS is a hypersonic boost-glide missile development and test program that provides longer range, shorter flight times, and high survivability against enemy defenses.
The ARRW program seeks to mature critical technologies to high speed flight, and accelerate the weaponization of hypersonic strike capabilities. The hypersonic weapon is being designed to travel at 3,800 miles per hour.
LRHW project
LRHW, meanwhile, will leverage the common hypersonic boost glide all up round and, in partnership with the US Navy's CPS program, introduce a new class of ultrafast and maneuverable long-range missiles with the ability to launch from ground mobile platforms.
Just last summer the U.S. Army awarded a $428.3 million four-year order to Leidos Dynetics Technical Solutions (DTS) in Huntsville, Ala., to develop prototype glide bodies for hypersonic weapons that could see applications across all U.S. military services. The Common-Hypersonic Glide Body (C-HGB) prototypes. DTS is a wholly owned subsidiary of Leidos Dynetics.
The Army three years ago awarded a $352 million contract to DTS to produce the first commercially manufactured set of C-HGB systems. DTS is working with Lockheed Martin Corp. to support integration and prototyping of the new C-HGB, which is expected to be available across military services to provide commonality to air, land, and sea hypersonic weapons.
Lockheed Martin Corp. is working with the Army on multi-year hypersonic weapons development in support of the Army's focus on long-range precision-strike missiles.
Lockheed Martin is prime contractor for the Long-Range Hypersonic Weapon (LRHW) systems integration project. The Lockheed Martin-team will develop and integrate a land-based hypersonic strike missile prototype in partnership with the Army Hypersonic Project Office.
The Lockheed Martin LRHW team includes DTS; Integration Innovation Inc. (i3) in Huntsville, Ala.; Verity Integrated Systems in Huntsville, Ala.; Martinez & Turek Inc. in Rialto, Calif.; and Penta Research Inc. in Huntsville, Ala.
The LRHW prototype will capitalize on the C-HGB and introduce a new class of ultrafast and maneuverable long-range missiles with the ability to fire from mobile ground launchers. Hypersonic munitions travel at speeds at least as fast as Mach 5, or five times the speed of sound.
Hypersonic strike weapons are a key aspect of the Army's Long Range Precision Fires (LRPF) effort to develop long-range artillery-delivered munitions able to fire as far as 187 miles, as well as the national security strategy to compete with and outpace potential enemies in hypersonics.
HALO project
HALO enables carrier-based aircraft to conduct stand-off strikes against high-value surface threats. It penetrates near-peer air-defense systems to defeat high-value surface threats, so the Navy can operate in and control contested battles paces.
The Navy is ready to approach industry to develop a new hypersonic munition that can be launched from carrier-based aircraft for attacking enemy surface ships and shore installations. The Hypersonic Air-Launched Offensive Anti-Surface Warfare (OASuW) (HALO) Weapon System, if successful, may replace or augment a variety of today's anti-ship missiles.
Preliminary development of HALO has been handled by Lockheed Martin Corp. and by Raytheon Technologies Corp. (RTX) in Tucson, Ariz. HALO likely will augment or replace current carrier-based anti-ship missile systems like the Long Range Anti-Ship Missile (LRASM), Harpoon, and Penguin missiles. Hypersonic missiles typically will be for attacking high-value targets like enemy capital ships, command posts, or forward-staging areas.
The HALO hypersonic weapon should have early fielding by 2029, and first operational capability by 2031. Only eligible prime contractors who have experience with carrier-based hypersonic weapons development -- like Raytheon and Lockheed Martin -- will have access to the upcoming HALO solicitations.
HALO engineering and manufacturing development (EMD) will design, develop, and test this weapon system, including the HALO all-up-round; system security; operational test and evaluation; and moving the HALO system into production. More information is online at https://sam.gov/opp/af555b72c98b424bbccc0141302daa46/view.
Additional hypersonic projects are in progress throughout the U.S. military services.
HACM program
The HAWC program gave rise to the U.S. Air Force Hypersonic Attack Cruise Missile (HACM) program to create a scramjet-powered hypersonic missile as an operational weapon. HACM contractors include Raytheon Technologies Corp. in Arlington, Va., and Northrop Grumman Corp. in Falls Church, Va. Future HACM munitions will go aboard aircraft such as the Boeing F-15EX and F-15E Strike Eagle jet fighter bombers.
Raytheon and Northrop Grumman are working under terms of a $985.3 million order announced in September 2022 to develop one of the first hypersonic cruise missiles to be in the U.S. inventory.
The hypersonic operating environment involves heavy exposure to shock, vibration, heat, and thermal shock, so its guidance and navigation technologies must be specially hardened to withstand such severe operating conditions.
The HACM hypersonic missile will have scramjet engines, which use high vehicle speed to compress incoming air forcibly before combustion, which enables sustained flight at hypersonic speeds. By traveling at these speeds, hypersonic weapons like HACM can reach their targets more quickly than similar traditional missiles, and potentially evade air defenses.
Raytheon and Northrop Grumman have worked together since 2019 to develop, produce, and integrate Northrop Grumman's scramjet engines onto Raytheon's air-breathing hypersonic weapons.
The HACM project incorporates enabling technologies from other research projects. In 2020, the Air Force joined Australia in a multi-year project called the Southern Cross Integrated Flight Research Experiment (SCIFiRE) to develop air-breathing hypersonic cruise missile prototypes. The Air Force awarded three 15-month SCIFiRE contracts in June 2021 to Boeing Co., Lockheed Martin Corp., and Raytheon to complete preliminary designs of a hypersonic cruise missile.
The HACM program will bring the Raytheon SCIFiRE prototype design into production for fighter aircraft integration, and deliver two leave-behind assets with operational utility. Through SCIFiRE, the U.S. and Australia will continue collaborating on HACM design and development, including using Australian test sites for the initial all-up-round flight tests. The Air Force plans to deliver a HACM capability with operational utility by 2027.
Hypersonic aircraft
Today's hypersonic research initiatives are not limited only to missiles. the U.S. National Aeronautics and Space Administration (NASA) Glenn Research Center in Cleveland has awarded contracts collective worth $5.1 million to The Boeing Co. and Northrop Grumman Corp. for the High-Speed Endoatmospheric Commercial Vehicle Conceptual Design Study and Technology Roadmaps Development project.
NASA is seeking to develop enabling technologies for high-speed commercial transports able to fly at speeds between Mach 2 and Mach 5 that could enter service as early as the 2030s. Mach 3 to Mach 5 represent speeds between 1,535 and 3,836 miles per hour.
The Boeing Defense, Space & Security segment in St. Louis won a $2.6 million contract, and the Northrop Grumman Aeronautics Systems segment in Palmdale, Calif., won a $2.5 million contract.
These studies will identify key technology needs and opportunities to enable high-speed commercial passenger aircraft. Specific speed, passenger count, range, and allowable technology readiness level has yet to be negotiated.
NASA’s Hypersonic Technology and Commercial Supersonic Technology projects fall under the NASA Advanced Air Vehicles Program, which will lead efforts to develop an environmentally sustainable civilian high-speed aircraft.
Hypersonic flight isn't new
There's a widely held perception that hypersonic flight is a recent innovation, and that its enabling technologies represent the cutting-edge of development. Nothing could be farther from the truth, experts say. The U.S. Air Force-NASA North American X-15 rocket-powered experimental aircraft first broke the Mach-5 hypersonic barrier nearly 63 years ago on 23 June 1961.
That aircraft flew experimental flights for nearly a decade from 1959 to 1968, and for its day set speed and altitude records and crossed the edge of outer space. That plane's fastest speed was Mach 6.7 (5,140.7 miles per hour) during a flight on 3 Oct. 1967. Later on, the NASA Space Shuttle flew as fast as Mach 25 as it re-entered the Earth's atmosphere. Aeronautical and electronics engineers have had more than six decades to apply the lessons learned since the first hypersonic flights. They've shown that it can be done.
"There's a lot of hype in hypersonics," says Andrew Knoedler, a program director for the adaptive communications and sensing product line at the BAE Systems Electronic Systems segment in Nashua, N.H. "There was a lot of hype over the last five years, maybe longer, that hypersonics is really, really hard. I think we need to do our deliberate engineering as we have done before. Many of these lessons learned can be applied to hypersonic munitions and manned aircraft." Knoedler also has experience with the Air Force and DARPA on hypersonics research projects.
Ruggedizing electronics for hypersonics
Hypersonic aircraft and munitions must withstand environmental extremes in temperature, shock, and vibration. The electronics for communications, navigation, guidance, and sensors must have the ability to operate through the shock of launch, vibration from the buffeting the munitions experience while traveling through the turbulent atmosphere at high speeds, the high temperatures of friction through the atmosphere, and the temperature shock of moving rapidly from high to low altitudes.
Several research projects are in progress to help the electronics in hypersonic vehicles operate reliably in these kinds of difficult conditions. One particular challenge is to enable commercial-grade cutting-edge electronic technologies to function aboard hypersonic vehicles so that these new designs can be reliable and affordable.
Lockheed Martin officials say the biggest challenge when developing hypersonic munitions are the effects speed has on the system. Going greater than Mach 5 speeds bring multi-faceted heat related challenges. For example, you're not just managing the heat for the flight vehicle externally, but our engineers also are challenged to keep the internal capability of high-speed objects functioning throughout that heat load.
Last fall the Northrop Grumman Mission Systems segment in Linthicum Heights, Md., won a $9.2 million DARPA contract for the Miniature Integrated Thermal Management Systems for 3D Heterogeneous Integration (Minitherms3D) project. Minitherms3D seeks to develop scalable thermal management technologies to help control heat in future electronics architectures that involve 3D heterogeneous integration (3DHI) chip stacks.
The Minitherms3D program seeks to revolutionize 3DHI thermal management and significantly reduce thermal resistances within the 3D stack and external to the stack of 3DHI systems, while increasing volumetric heat removal. The project seeks thermal management technology scalable to an arbitrarily large number of high-power tiers in 3DHI chip stacks. Northrop Grumman will handle the program's 18-month first phase. Program goals include 3D stacking of five tiers with total heat dissipation more than 6.8 kilowatts with the heat rejection system limited to less than 0.006 cubic meters.
Continued rapid growth of compact high-performance microsystems is limited by inadequate integrated thermal management, including acquisition of heat from 3D integrated circuits, to the heat's transport and ultimate rejection to the ambient environment. For example, the state of the art in 3DHI in high-performance computing typically uses one tier of logic and several tiers of high-bandwidth memory. Stacking of logic is currently limited to low-power tiers.
Three-dimensional (3D) stacking of several tiers of high-power logic and other functional blocks, including radio frequency devices, offers significant advancement in future microsystems, but today is infeasible because of insufficient in-plane and out-of-plane heat acquisition from each tier, and poor thermal isolation between functional blocks.
The Minitherms3D project has two technical challenges: reducing thermal resistances within the 3D stack; and reducing thermal resistance external to the 3D stack. Reducing thermal resistances within the 3D stack involves increasing in-tier heat transfer without increasing tier thickness. Regions of average heat flux more than 150 Watts per square centimeter along with localized hot spots more than 1 kilowatt per square centimeter in 3DHI tiers simultaneously must be managed thermally to maintain acceptable chip temperatures.
DARPA HOTS
In March DARPA announced a $10.9 million contract to Ozark Integrated Circuits Inc. in Fayetteville, Ark., for the High Operational Temperature Sensors (HOTS) program to design electronic components for extremely hot environments for future hypersonics and jet engine applications. The HOTS program will develop a technology for high-bandwidth high-dynamic-range sensing that operates at temperatures of 800 degrees Celsius and hotter.
Many commercial and defense systems such as hypersonic aircraft and missiles, automotive, jet engine turbine, and oil-and-gas systems experience thermal environments beyond the capability of today’s high- performance physical sensors, DARPA researchers explain. Yet today's state of the art typically cannot operate in temperatures higher than 225 C because of intrinsic limitations to their complementary metal oxide silicon (CMOS) materials.
DARPA wants chip designers at Ozark Integrated Circuits to develop a pressure sensor module with an integrated transducer and signal-conditioning microelectronics, as a demonstration of electronic components that could withstand the high temperatures of hypersonic missiles and aircraft, or for internal use in advanced jet engines.
While wide-bandgap materials like silicon carbide (SiC) or gallium nitride (GaN) have potential for use at high temperature due to their significantly lower intrinsic carrier concentration, today they do not support sensor microelectronics with high bandwidth and large dynamic range at high operating temperature for useful lifetimes.
At high temperatures these materials can crack because of their coefficients of thermal expansion. They also can leak current because of the increase in thermal carriers. HOTS will be a 36-month program broken into two phases.
To overcome these kinds of thermal limitations, HOTS seeks to overcome three key technical challenges: achieving long lifetime and large bandwidth transistors at high temperature; achieving a high-sensitivity transducer at high temperature; and integrating a high operating temperature sensor without degrading performance.
Electronics design challenges
Lockheed Martin officials say the primary enabling technologies for hypersonics are advanced high-temperature materials made from complex combinations of constituent compounds and elements. Company engineers are adapting these materials to aeroshells for vehicles such as for hypersonics.
Lockheed Martin engineers are learning how to take these exotic materials and create manufacturing processes that can produce them reliably by bringing together engineering across design, test, design for manufacturing, and design for producibility.
They key to designing electronics that can withstand the environmental challenges of hypersonic flight involves applying past lessons learned, as well as common-sense engineering, says BAE Systems's Knoedler.
"Look at the Space Shuttle. It had two different trajectories -- getting into orbit for 10 to 15 minutes above Mach 1. Coming back it starts at Mach 25, and goes down to zero. A lot of those challenging conditions already have been figured out. In some situations you get a blackout, when the air ionizes, and you get a lot of interfering electricity around the vehicle itself. We make sure to place the antennas in the right places and choose the right frequencies."
The first space shuttle flights did not involve satellite navigation with the Global Positioning System (GPS), but later flights had GPS navigation through technology upgrades. "They had to put those antennas in the right spots so they were not affected by the environment as much," Knoedler says. "There always will be some ionization around the vehicle; it's just about antenna location. That's where the analysis comes in, a good understanding of the atmosphere where you will be at a certain time, and the trajectories. We have very good models of that."
Hypersonic flight also has a similar challenge dealing with shock and vibration. "We need to know where those shocks might interfere with your other shocks, and this has to do with the vehicle geometry," Knoedler says. "You have to understand shocks; you need to understand your thermal environment, when you get heating on the outside of the vehicle, and you have to manage the heat in that environment."
Sometimes design tradeoffs in hypersonic vehicles involve the right choice of materials to survive high temperatures. "The trajectory you want the vehicle to fly through will determine your thermal profile," Knoedler explains. "The Space Shuttle designers chose a ceramic for the heat-resistant tiles, and they had to design antennas to work with that ceramic."
Just above hypersonic speeds, for example, designers might be able to use traditional materials that are not made from exotic composites, such as a metal alloy that might survive that particular trajectory. Yet at upper hypersonic speeds near Mach 10, designers might have to make decisions about blending a metal alloy and composite materials, or not use metal at all.
"They are trying to make technology tradeoffs at the higher heat load of a hypersonic vehicle's trajectory," Knoedler explains. "They can manage the heat on the outside, and determine how that heat transfers from the outside to the inside of the vehicle, which leads to the internal thermal environment and how long you can last at a particular level."
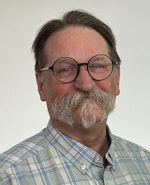
John Keller | Editor-in-Chief
John Keller is the Editor-in-Chief, Military & Aerospace Electronics Magazine--provides extensive coverage and analysis of enabling electronics and optoelectronic technologies in military, space and commercial aviation applications. John has been a member of the Military & Aerospace Electronics staff since 1989 and chief editor since 1995.