DARPA asks industry for MEMS gyros rugged enough for positioning and navigation in fast unmanned vehicles
ARLINGTON, Va. – U.S. military researchers are asking industry to develop tiny gyros and accelerometers able to withstand the structural rigors of fast maneuvering unmanned vehicles to improve precise positioning and navigation.
Officials of the U.S. Defense Advanced Research Projects Agency (DARPA) in Arlington, Va., issued a disruption opportunity last month (DARPA-PA-24-04-03) for the Nimble Ultrafast Microsystems (NIMBUS) project.
Fast uncrewed vehicles
One goal of the NIMBUS project is to design micro-electro-mechanical systems (MEMS) gyros and accelerometers that can help uncrewed vehicles operating in the air, on land, or in the water maneuver quickly without G-forces damaging or destroying these MEMS devices.
Warfighters in the field must make rapid course corrections that require positioning or dead reckoning with accuracy and speed, DARPA researchers explain. In such cases, fast sensor resolution is critical to enhance the sensors’ scale-factor to achieve high accuracy.
NIMBUS aims to demonstrate tethered resonant systems that operate just below the mechanical fracture velocity of the MEMS. Today’s MEMS oscillators are limited to a maximum velocity of five meters per second because of fabrication, anchor design, transducer defects, and chaotic motion caused by non-linear mechanical springs.
NIMBUS performers will co-design the fabrication process such that select performers will improve on their approaches to achieve velocities greater than 200 meters per second.
Technology advances
The last two decades have seen technology advanced in MEMS devices for commercial positioning and navigation applications, yet have not been able to provide military navigation in GPS-denied environments with hand-held devices.
NIMBUS performers must address velocities to the fracture velocity limit of poly-silicon, and achieve velocities exceeding the limits of poly-silicon, and reach the fundamental velocity limits of single-crystal materials such as silicon, silicon carbide, or similar materials.
Five factors have played a prominent role preventing high velocities on tethered chip-scale microsystems: inefficient transducers, weak anchors, micro cracks and their propagation, nonlinear chaotic behavior of the oscillating proof-mass, and material fatigue.
NIMBUS phase-one will demonstrate tethered microsystems with velocity greater than 65 meters per second -- the fracture velocity of poly-silicon -- and show wafer-scale yield of greater than 50 percent.
200 meters per second
The second phase will achieve a velocity greater than 200 meters per second with a wafer-scale yield of greater than 70 percent to study material fatigue and fracture.
Improving sensor velocity and momentum by 40X will result in superior sensor performance, researchers say. If a commercial off-the-shelf gyroscope today can resolve the rotation rate of the Earth in 10 minutes, for example, a NIMBUS-enhanced gyroscope could do that job in less than a minute.
Companies interested should submit responses no later than 20 Dec. 2024 to the DARPA Broad Agency Announcement Portal online at https://baa.darpa.mil.
Email questions or concerns to Sunil Bhave, the DARPA NIMBUS program manager, at [email protected]. More information is online at https://sam.gov/opp/4ecb49f774784c0ea5e538348a3b6368/view.
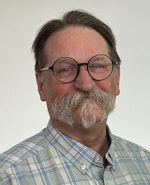
John Keller | Editor-in-Chief
John Keller is the Editor-in-Chief, Military & Aerospace Electronics Magazine--provides extensive coverage and analysis of enabling electronics and optoelectronic technologies in military, space and commercial aviation applications. John has been a member of the Military & Aerospace Electronics staff since 1989 and chief editor since 1995.