Electronics technicians long have relied on accurate test and measurement equipment to see if anything is amiss before something can “go wrong” with potentially mission- or life-threatening consequences. As equipment becomes more and more packed with technology, failure points grow, and reliable and accurate test and measurement become even more vital.
In addition, flightline crews today must do more with fewer people; the switch from analog to digital helps to make that possible, says retired U.S. Air Force Maj. Gen. Stephen Sargeant, who is the CEO of Marvin Test Solutions (MTS) in Irvine, Calif.
“Most militaries have fewer people doing work today compared to the number of people doing the same work 30 years ago,” Sargeant says. “You need to get more accurate and rapid results in their hands so that fewer people can actually perform at the same level or even a higher level than when there were more people on the flightline. The more sophisticated test equipment that’s easy to use can enable a smaller force to be just as or even more lethal. That’s good news for everybody.”
Increased lethality and reliability are bad news for the enemy, but fewer required people on the flightline means lower risk of losing our servicemen and women, which is great for the men and women in uniform who serve and those that lead them.
“Sending fewer Airmen to deploy to support the flightline can be good news if they have the right tools,” says MTS’s Sargeant. “It can be good news for their commanders, and it can be good news for taxpayers if the Airmen have the right tools. I think efficiency and effectiveness are important based on what we’re hearing from the warfighters closest to the airplanes who are responsible for ensuring their weapons are going to work properly.”
Sargeant notes that because fewer Airmen are necessary to ready aircraft for battle, tailored force packages can go to far-flung locales with fewer logistical hurdles.
“This allows lethal, more compact deployed units around the world than the traditional large unit or wing deployments,” Sargeant says. “Instead of taking 24 to 48 airplanes into a fully established base with all the infrastructure to support the number of people that it would traditionally take to support that many airplanes — now they may just take a couple of ‘these’, and a couple of ‘those,’ and put them forward in a place like Guam or Poland.”
Sargeant says one armament test and maintenance device on the flightline getting positive feedback from maintainers is MTS’s MTS-3060A SmartCan Universal Armament Test Set for smart and legacy weapons-enabling armament systems.
In addition to JDAM and AMRAAM emulation, the MTS-3060A also tests the functionality of armament during preload testing and tests gun systems. The SmartCan also possesses audio and video signals to assist in troubleshooting. The MTS-3060A SmartCan also contains a built-in-test (BIT) that provides verification of major circuits.
“It’s a test set that is handheld and weighs approximately four pounds, yet it combines large-box technology typically carried by two or three people to the flightline,” Sargeant says. “It is in the shape and size of some of the more obsolete, legacy flightline test sets that could only do stray voltage and continuity. We not only put that large-box capability in a small hand-held shape and size, but also ruggedized it.”
Sorting through the noise
Timothy Harris, application engineer, in the RF & microwave division at electronics distributor Pasternack Enterprises, in Irvine, Calif., says today’s test and measurement equipment puts a lot more power — and analysis — in the hands of the people who need it on the flightline.
“Advanced instrumentation facilitates not just precise and accurate evaluation of performance, but also often delivers application-specific analysis where previous generations provided only raw data, leaving end-users to develop complex solutions,” says Pasternack’s Harris. “In some cases, results that previously could only be obtained with a rack of instruments, costly, custom automation, and highly-capable operators can be reliably, easily, delivered by a single benchtop instrument.”
Harris continues, “A case in point are high-performance residual phase noise measurements for which many aerospace companies historically relied on one or two employees capable of squeezing accurate results from exceedingly difficult measurement systems. As the deliverable tools evolve, they provide insight and evaluation more reliably and accurately, facilitating R&D and assessment and screening of fielded systems.”Trends in test and measurement technology is boosting capabilities in frequencies, bandwidth, linearity, accuracy, precision, embedded analysis, reliability, and product support, Harris reports. In addition, the engineer says that military and aerospace test and measurement equipment must stand up to extreme environments.
“New functional capabilities and generational performance advancements for RF components intersect with the ongoing requirement in mil-aero to reliably operate under extreme environmental conditions over long periods of time with little or no intervention or maintenance,” Harris says. “As a result, system engineering allocates little or no room for error in test and measurement results. As a result, instrument designers and manufacturers compete aggressively over incremental advantages in capability, precision, and accuracy.”
Earlier this spring, Pasternack began offering tunnel diode detectors with test and measurement in mind. The 26 models of tunnel diode detectors have rugged Germanium planar construction and operate over octave and broadband frequencies that range from 100 MHz to 26 GHz. They are available in positive and negative video output polarities and offer dynamic range with efficient low-level signal detection. Another of these tunnel diode detectors are the added benefit of an extremely fast pulse response rise time of 5 nanoseconds typical.
More flight, fewer tests
Patrick Quinn, senior product line manager for data acquisition at Curtiss-Wright Corp. in Davidson, N.C., says that accurate test data will enable aircraft to take to the skies sooner at a lower cost.
“You’ve got to have accurate data because you’ve got to basically reduce the number of flight tests; actually doing more test flights, the more cost (there is),” Quinn says. “Well, thankfully, the pressure we see everywhere — where it’s military or commercial — they see driving down the actual test program schedules which reduces some flights ... They really want highly accurate measurements to validate their test models.”
It was a sentiment echoed by Curtiss-Wright Defense Solutions public relations director John Wranovics. Curtiss-Wright Defense Solutions is based in Ashburn, Va.
“The most critical thing in this application space is the cost of flights,” Wranovics says. “So, anything that delays air time, that keeps the airplane on the ground, or causes it to need to be re-flown for tests add huge amounts of cost and complexity and adds risk. So, everything that we do is done to optimize time in the air and to avoid time on the ground.”
In addition to the people in the civilian and military aerospace sector who demand accurate test results on the flightline, there is also a push to get more out of their test and measurement equipment.
“The real trend is to reduce the size and weight, and then get more data out,” says Curtiss-Wright’s Quinn of flightline test equipment. “Then, get more data out and increase the channel counts per card.”
Quinn notes that when technology allows for more power in smaller devices, issues can and do arise. Size, weight, and power (SWaP)-minded designers seek to find a balance.
“There are problems when you go faster and smaller,” such as managing system heat, Quinn says. “So, we have (engineers) design in really good thermal behavior on temperature monitoring and pyro monitoring into all our boxes.”
With SWaP and accurate, speedy, and reliable data transfer in mind, Curtis-Wright announced an expansion in August of the company’s Axon data acquisition unit (DAU) lineup.
The Curtiss-Wright AXN/ABM/401 is a 24-channel ARINC-429 bus monitor parser and packetizer that supports 500 megabit-per-second throughput to enable flight test instrumentation (FTI) applications to handle a growing amount of data. It also supports higher parser slot count and has new filtering rules to optimize data capture from ARINC 429 busses.
On the line
Test and measurement experts at Abaco Systems in Huntsville, Ala., extended their company’s range of portable avionics devices for test and simulation, flightline, and development in August when they unveiled the ARINC 664-compatible RCNIC-A2PA-TB and multiprotocol RAR15XF-TB that supports as many as four channels of MIL-STD-1553 and 18 channels of ARINC 429 on one device. Both devices feature Thunderbolt 3 interfaces, which limits neither the performance nor the flexibility of avionics databus adapters. Thunderbolt 3 moves data at four times the speed of the highest-speed USB connection, and drastically lowers latency.
The Abaco RAR15XF-TB is one of the highest-density portable MIL-STD-1553 and ARINC 429 avionics databus test device available. It delivers as many as four channels of 1553 and 18 channels of ARINC 429 in an extremely portable device. Its on-board firmware, large data buffers, and a high-level API are integrated to provide flexibility in monitoring and generating ARINC databus traffic.
The RCNIC-A2PA-TB is a dual-port ARINC 664 interface for monitoring, generating, or analyzing full-bandwidth AFDX/ARINC 664 Part 7 protocol traffic. Abaco’s pipeline architecture makes the most of packet throughput using parallel controllers and DMA transfers, thereby avoiding the bottlenecks of CPU-based interface.
Seeing is believing
The ARINC 818 video interface and protocol standard was developed to create uniform parameters and manage high-bandwidth, low-latency, and uncompressed digital video transmission. Great River Technology Inc. in Albuquerque, N.M., offers the Avionics Digital Video Bus for ARINC 818 test and measurement. This system helps users address what happens when cockpit displays fail in the air well before catastrophe occurs.
“In a safety-critical system; pilots need to know that the display is good, or they need to be looking at alternative sources of information in the cockpit, says Paul Grunwald, chief systems architect at Great River. “Not only do they have to work, they have to fail correctly.”
“The Xf Tuner can be used to drive the display to exercise timing and do fault injection,” says Great River’s Grunwald. “A lot of displays, when receiving bad input, will freeze or lock up, usually at a point when the pilot doesn’t recognize the issue. The Xf Tuner can inject errors to verify failure modes. One of the important things in regard to testing is to inject faults and make sure the pilot is aware of what happens on the other end of the link. Whatever output the pilot is looking at can then fail in a deliberate fashion.”
In addition to error injection options, the Xf Tuner from Great River has link rates as fast as 4.25 gigabits per second, and allows protocol adjustments in real time.
“You, as an engineer, can set-up the link rate, frame rate, resolution, timing, color depth, and exercise your receiver to meet the necessary parameters,” Grunwald says.
For the ARINC 818 transmitter design, Great River offers its third-generation video and protocol analyzer (VPA III). If using the latest Velocity card from Great River, its VPA III can analyze any video format.
“The VPA III is a receiver that allows you to examine the ARINC 818 stream down to the bit level,” Grunwald says. “We handle both ends of the link from an engineering standpoint.”
Great River’s VPA III is able to use the protocol profile for automatic checks of line timing, video frame timing, video resolution, number of bytes per avionics digital video bus frame, as well as other parameters.
Old with the new
Electronics designers and aircraft flight crews must be able to count on their critical electronics to work when they need them most, says David Vondran, senior product marketing manager at Astronics Corp. in East Aurora, N.Y. “Accuracy is important because the equipment used in this sector can make the difference between mission success or failure, even life or death in some cases,” Vondran says.
“The information that our test solutions provide to the user is ultimately used to decide whether or not a piece of equipment can be used or deployed, he says. “IfAstronics experts are trying to build test and measurement equipment that not only can ensure system accuracy, but also that can test cutting-edge technology as well as legacy systems.
“We are seeing more demand for portability and more complete capabilities that can test legacy and modern electronics,” Vondran says. “This then drives the need to incorporate modular instrumentation in order to future-proof our solutions, thus extending the life of our customers’ investments.”
Military radios and other communications devices are examples. “Tactical radios are trending towards increasing complexity, which imposes automation on the maintenance workflow in order to keep the test instrumentation easy to use,” Vondran continues. “Furthermore, tactical radios often return no-fault-found (NFF) results. This determination means the problem likely is in the network (and not the tactical radio). Having portable tools will become more important in the future of field test to solve the complexity not only in tactical radios, but the networks they serve.”
The Astronics ATS-3100 RTS and the CTS-6010 radio test sets exemplify the trend to blend legacy and modern systems, Vondran says. “Both solutions are aligned with these trends, offering solutions where they’re needed most, with capabilities to test any radio that the user may choose for the mission. Both solutions are part of the Astronics family of portable platforms, which can be configured per our customers’ requirements.”
The ATS-3100 RTS is a PXI Express-based, benchtop, software-defined system that can test radios like the Raytheon AN/ARC-231, Collins Aerospace AN/ARC-210, and L3Harris AN/ARC-201. The ATS-3100 RTS and the portable CTS-6010 share a common software.
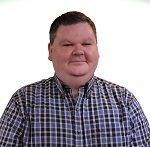
Jamie Whitney
Jamie Whitney joined the staff of Military & Aerospace Electronics and Intelligent Aerospace. He brings seven years of print newspaper experience to the aerospace and defense electronics industry.
Whitney oversees editorial content for the Intelligent Aerospace Website, as well as produce news and features for Military & Aerospace Electronics, attend industry events, produce Webcasts, oversee print production of Military & Aerospace Electronics, and expand the Intelligent Aerospace and Military & Aerospace Electronics franchises with new and innovative content.