Air Force asks Northrop Grumman to use 3D printing and additive manufacturing for hypersonic test items
ARNOLD AIR FORCE BASE, Tenn. – U.S. Air Force hypersonics experts needed a company to use 3D printing and additive manufacturing to fabricate test components to test enabling technologies for hypersonic missiles and aircraft. They found their solution from Northrop Grumman Corp.
Officials of the Air Force Test Center at Arnold Air Force Base, Tenn., announced a potential $9.8 million five-year contract last week to the Northrop Grumman Propulsion Systems & Controls segment in Elkton, Md., for the Additive Manufacturing to Improve Test and Evaluation of Hypersonic Vehicles project.
Northrop Grumman will use 3D printing and additive manufacturing to create advanced hypersonic test facility components and test articles for the Hypersonic Aerothermal and Propulsion Clean-Air Testbed (HAPCAT) facility in Ronkonkoma, N.Y.
Related: NASA creates institutes to research 3D printing and quantum tech for climate endeavors
The HAPCAT facility produces harsh conditions to simulate the environment a hypersonic vehicle will experience in flight, such as high temperatures and pressures.
Northrop Grumman will use 3D printing and additive manufacturing to build test articles able to withstand such conditions. Active cooling techniques like internal water passages also are necessary to manage the thermal loading of the hypersonic vehicle test components.
The 3D printing and additive manufacturing capability for HAPCAT also would support testing at other U.S. military facilities that produce harsh conditions, such as the J-5 clean-air facility at Arnold Air Force Base, Tenn.; the arc heater facilities at the NASA Ames Research center in Mountain View, Calif.; and the Aerodynamic and Propulsion Test Unit (APTU) at Arnold Air Force Base, Tenn.
Related: Boeing HorizonX ups investment in aerospace-quality, 3D-printed metal parts
Northrop Grumman also will use 3D printing and additive manufacturing to fabricate and repair facility components and test articles. Air Force experts want Northrop Grumman to develop technologies to develop and demonstrate 3D printing and additive manufacturing capability for HAPCAT and other military hypersonic facilities.
The 3D printing and additive manufacturing capability will provide reduced manufacturing times, increased facility availability, and improved support to military hypersonic weapon system ground testing, Air Force officials say.
On this contract Northrop Grumman will do the work in Ronkonkoma, N.Y., and should be finished by May 2028. For more information contact Northrop Grumman Propulsion Systems online at www.northropgrumman.com/space/propulsion-systems, or the Air Force Test Center at www.aftc.af.mil.
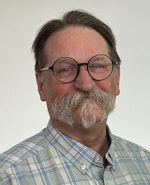
John Keller | Editor-in-Chief
John Keller is the Editor-in-Chief, Military & Aerospace Electronics Magazine--provides extensive coverage and analysis of enabling electronics and optoelectronic technologies in military, space and commercial aviation applications. John has been a member of the Military & Aerospace Electronics staff since 1989 and chief editor since 1995.