Technologies to ruggedize electronics for hypersonic flight are ready today for aircraft and munitions
THE MIL & AERO COMMENTARY – Hypersonic flight for crewed and uncrewed aircraft, as well as smart missiles, is one of the Pentagon's top priorities to keep pace with technological developments in hypersonics in Russia and China. It follows that hypersonics would represent the most cutting-edge enabling technologies, but that would be wrong.
That fact is that U.S. developments in hypersonics -- or the ability to fly at speeds in excess of five times the speed of sound -- have been in progress now for more than six decades since a U.S. Air Force-NASA North American X-15 rocket-powered aircraft with test pilot Robert White at the controls first took an aircraft hypersonic.
White flew the X-15 experimental aircraft at Mach 5.27, or 4,043.5 miles per hour, on 23 June 1961 after being dropped from a B-52 mothership. It wouldn't be the last manned hypersonic flight in those days. Less than two months later another X-15 flight reached Mach 5.21 on 12 Sept. 1961.
The X-15 would fly hypersonic 110 more times before the program wound-up in 1968, reaching a maximum speed of Mach 6.7, or 5,140.7 miles per hour, on 3 Oct 1967. The speed record set by a manned aircraft that day -- more than half a century ago -- never has been broken.
Suffice it to say that hypersonic flight isn't new.
The longevity of U.S. research in hypersonic flight is significant because of the many technological lessons learned, ranging from aircraft propulsion, lifting body design, and electronics that can operate through environmental extremes like temperature, shock, and vibration.
The bottom line is nearly all -- if not completely all -- of the technologies necessary to ruggedize electronic components and subsystems for hypersonic flight already has been developed and mostly likely perfected.
Microprocessors, general-purpose graphics processing units (GPGPUs), field-programmable gate arrays (FPGAs), power control and conditioning chips, solid-state memory, and many others have been developed that can work through the rigors of hypersonic flight.
Thermal-management techniques, ranging from conduction and convection cooling, to more exotic air-flow-through technologies, and even to liquid-cooling to keep components from exceeding their temperature-design parameters have been developed and deployed.
Techniques are in use not only to keep critical electronics cool, but also to detect when systems start to exceed parameters and throttle-back performance to avoid component damage or destruction.
Packaging is available to shield even somewhat fragile advanced commercial-grade electronic components from damage due to shock, vibration, heat, cold, humidity, and thermal shock. Generations of electrical and aeronautical engineers have had plenty of time to develop what they need for navigation, guidance, situational awareness, timing, targeting, and other capabilities for the next generation of hypersonic munitions.
So where do we go from here? When it comes to electronics, it's not so much a technology-development problem as it is a technology-integration problem. How to systems integrators put together today's electronics, packaging, and thermal management technologies for tomorrow's hypersonic munitions and aircraft?
The answer, essentially, is they already have most if not all of the electronic technologies that they need to meet the design challenges of new hypersonic systems. So what does this all mean for the future of hypersonic munitions and aircraft?
It's closer than you might think.
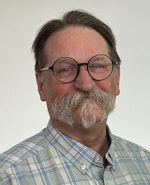
John Keller | Editor-in-Chief
John Keller is the Editor-in-Chief, Military & Aerospace Electronics Magazine--provides extensive coverage and analysis of enabling electronics and optoelectronic technologies in military, space and commercial aviation applications. John has been a member of the Military & Aerospace Electronics staff since 1989 and chief editor since 1995.