Aerospace and defense organizations look to advanced test and measurement equipment to support both legacy and cutting-edge systems.
Innovation in aerospace and defense technologies happens at an exponential pace, as does development in test and measurement technologies, says Jeremy Haynes, electronic warfare (EW) business lead at Keysight Technologies Inc. in Englewood, Colo. "While companies are focused on developing the next generation of military [and aerospace] electronics, they must ensure their effectiveness prior to being used in an operational setting," driving demand for test equipment.
"Having innovative test and measurement solutions can allow an engineer to identify and fix problems early in the development of a new technology; oftentimes, waiting until the end of the product life cycle can prove to be cost prohibitive," Haynes says. "By investing in the correct [test] solutions, you can reduce cost and, most importantly, reduce risk to your projects."
Engineers use test and measurement solutions throughout the entire product life cycle, from modeling and simulation on a research and development (R&D) bench to flight testing and operational applications, Haynes explains. As an example, he says, Keysight's test and measurement technologies "are deployed in such diverse applications as measuring parametric values of power amplifiers to simulating advanced electronic warfare (EW) scenarios for next-generation warfighters."
Given the diversity of electronics and missions, aerospace and defense organizations increasingly are enticed by scalable, flexible test tools. With that in mind, Keysight engineers designed the N9952A FieldFox 50-gigahertz (GHz) handheld microwave analyzer as a tool to span the application space, whether a companion tool to an R&D bench or advanced measurement science deployed into an operational scenario, Haynes adds.
"Look for the increased utility in your test and measurement equipment rather than dedicated assets to serve a single function," says Darren McCarthy, aerospace & defense technical marketing manager at Rohde & Schwarz America (R&S) in Beaverton, Ore. For example, he says, as a standalone product, the R&S FSW signal and spectrum analyzer can provide RF and microwave performance analysis for radar transmitters using optional software for pulse, chirp, continuous wave (CW), or frequency-agile signal analysis.
The R&S SMW200 vector signal generator can test radar receivers or, in a multichannel configuration, it can test and calibrate beam-steering antenna and direction finding systems. In combination, the FSW and SMW200 can perform power and flexible functional test of the radar itself; a radar echo generator can be used to calibrate a radar, validate functionality, and verify DSP and settings of the radar configurations.
Mitigating obsolescence
Obsolescence mitigation is driving increased investment in test equipment. "Most military and aerospace programs run for years, and companies must keep the technology fresh so that they can add new capabilities, plus address the obsolescence issues that always crop up," says Gary Tilley, director of sales and business development at Astronics Test Systems in Irvine, Calif.
"With the current budget restraints, weapons systems such as B-52 or A-10 [military aircraft] are commonly required to extend their anticipated lifetime," Tilley explains. "This shifts focus away from investing in test solutions for new weapons systems toward investments for maintaining the aging fleet by solving the obsolescence issues on a much more frequent rate."
Obsolescence is an important driver of test equipment updates, Tilley says. "Companies can come and go, and products can come and go, but end users need to stay current to keep the equipment running. Customers are continually looking for intelligent ways to accomplish this. Military and aerospace companies and programs also are continually refreshing the systems they have. Most customers would rather add a capability to an existing system rather than build a new system, if possible."
Capabilities and eCASS
Military and aerospace organizations worldwide are simultaneously maintaining current equipment and driving toward more complex, sophisticated systems - growing the need for more capable test and measurement equipment.
"As we put new technology in the field, we need to upgrade our test capability to stay ahead of that new technology," says Tilley, who commends U.S. Naval Air Systems Command (NAVAIR) engineers for their work on the Consolidated Automated Support System (CASS), and new electronic stations known as eCASS.
"NavAir refreshed the technology as they transitioned from the older system to the newer system for testing aircraft and weapons on carriers. The organization maintained backward compatibility as a requirement, enabling the eCASS stations to leverage the test program set from the older CASS program," Tilley explains.
Engineers at the Lockheed Martin Corp. Rotary and Mission Systems segment in Orlando, Fla., are assisting the Naval Air Warfare Center Aircraft Division in Lakehurst, N.J., with the upgrade, maintenance, and support of U.S. Navy combat avionics test equipment. Lockheed Martin engineers will provide performance-based logistics (PBL) maintenance and support for as many as 400 CASS avionics test stations and 150 Reconfigurable Transportable CASS (RTCASS) stations. CASS, the Navy's standard automatic test equipment (ATE) family supporting electronics on naval aircraft, is designed to help warfighters troubleshoot and repair aircraft assemblies at sea or ashore and return the avionics to service quickly.
A more modern version of CASS, eCASS test equipment includes: radio-frequency systems, self-maintenance and test calibration operational test program sets, calibration equipment kits, shore installation kits, ship installation kits, test program sets development suites, high-power mission equipment kits, and electro-optic mission equipment kits. Lockheed Martin delivered the first modernized eCASS station in late 2014 to support all the aircraft in the Navy's fleet, including the F-35 Lightning II joint strike fighter (JSF).
"New technology is required to fully test any new systems, such as the JSF," Tilley says. "New weapons, aircraft, and other systems are coming online all the time, and they bring new and growing demands." As an example, he says, the Federal Aviation Administration's (FAA's) Next Generation Air Transportation System (NextGen) will require all new test capabilities for aircraft avionics systems as the world moves from analog, ground-based aircraft communications to satellite-based, digital aircraft communications. "The test requirements will change, requiring more digital instrumentation than analog instrumentation. In essence, it will flip the switch on test requirements to a new set of completely different parameters."
NextGen testing
Test and verification of avionics hardware and software systems are integral to ensuring the safety and efficiency of aircraft in U.S. National Airspace System (NAS), as well as virtually all air traffic management/air traffic control (ATM/ATC) infrastructures worldwide. Aerospace and defense firms rely on modern software analysis, test, and verification tools to ensure the safety and help speed the availability, certification, and deployment of myriad safety- and mission-critical airborne systems and platforms.
Atlantic Inertial Systems Limited, part of aerospace system and component manufacturer UTC Aerospace Systems, in Plymouth, England, adopted the CodePeer static analysis tool from AdaCore, with headquarters in New York and Paris, to perform a software test of its TERPROM digital terrain system for military transport aircraft. AdaCore products have helped to field and maintain a range of critical space, commercial avionics, military, and ATM/ATC systems, officials say.
Atlantic Inertial Systems engineers will use CodePeer to facilitate the certification, by authorities such as the FAA and European Aviation Safety Agency (EASA), of UTC Aerospace Systems' TERPROM terrain referenced navigation software, which enables the TERPROM system to provide precise, reliable, and predictive ground proximity warnings.
CodePeer automates the review and validation of Ada source code, helps detect potential errors early in product development, and automates several verification activities. The availability and functionality of such software test tools are credited with saving both time and money, especially compared to manual code review procedures, as well as providing "deep insight into potential issues and automating parts of the DO-178B verification process for the certification of software in airborne systems," officials say.
"Sound static analyzers allow code reviews to be significantly more effective and less time consuming than traditional manual methods," says Cyrille Comar, AdaCore president and a member of the SC205 (DO-178C) Working Group. "This automation is a major new trend in the verification of critical software."
AdaCore officials are seeing growth in the use of advanced static verification solutions, such as the company's CodePeer and SPARK Pro, says Martyn Pike, technical account manager at AdaCore in the United Kingdom. "Model-based design is clearly having an impact in the embedded systems development world, particularly through products like Simulink and Stateflow. AdaCore's QGen qualifiable code generator for [MathWorks] Simulink and Stateflow models brings software test technology such as coverage testing and testing through processor emulation to the model verification arena. The use of model-based design will hopefully continue and allow system-level verification technologies to flow down into software verification and vice versa.
"Test solutions are not always about dynamically testing the software and many properties of the software can be verified statically, allowing for early detection and removal of bugs and vulnerabilities, even before a single line of code is executed. Strive for automation and put in place a continuous integration process so bugs and vulnerabilities can be detected as early as possible," Pike recommends.
Safe, accurate air navigation
Engineers at prime contractor Moog in East Aurora, N.Y., used test and measurement equipment from Rohde & Schwarz (R&S) to help solve important measurement challenges, explains McCarthy of Rohde & Schwarz America.
Moog engineers selected the R&S EDS300 distance measurement equipment (DME)/pulse analyzer as a standard test solution for research & development, manufacturing, and field deployment of the company's MM-7000 series navigation aids, including the Moog MM-7000 advanced, full-service Tactical Air Navigation System (TACAN) and DME Beacon-Transponder, which are designed to provide the precise, reliable civil and military aircraft navigation vital to ensure international aviation safety.
The R&S EDS300 remote-controlled level and modulation analyzer can be deployed for the continuous monitoring, recording, and analysis of pulsed terrestrial navigation signals, while R&S EDS300 TACAN software includes measurement functions for analyzing signals from TACAN stations.
"The R&S EDS300 has the performance and sensitivity we need in the lab and manufacturing environment, plus it offers a robust and compact design for field testing the air interface of the MM-7000," says Moog Director of Engineering Achim Soelter. "The R&S EDS300 is an integrated test solution that enables Moog to have a standardized test process for verifying the performance of our TACAN and DME products at all stages."
Flight test and FAA requirements
Oregon-based aviation service providers Erickson Inc. and Helicopter Transport Services (HTS) are conducting flight tests of their jointly designed and developed advanced composite main rotor blades (CMRB) for the S-64 Aircrane and CH-54 Skycrane heavy-lift helicopters used globally for fire suppression and emergency response.
The new rotor blades are designed to increase aircraft performance at high elevations and temperatures, as well as increase fuel efficiency and reduce manufacturing and maintenance costs. Erickson engineers are conducting helicopter flight tests with the goals of perfecting the rotor blade design and achieving airworthiness certification and operation approvals. Flight testing is expected to span several months and certification is expected by the end of 2016.
"We use a suite of National Instruments data acquisition and recording equipment that utilizes a hybrid [Microsoft] Windows XP operating system and LabVIEW [system design] software," says Ian Gibson, chief engineer and FAA Powerplant Designated Engineering Representative (DER) at Erickson Inc. in Medford, Ore. "All our flight test parameters are fed into this equipment."
A custom-built data gathering and telemetry system, designed and manufactured to Erickson's specifications by Advanced Telemetrics International (ATI) of Spring Valley, Ohio, facilitates the transmission of flight test data from the rotating sensors affixed to the blade, rotor heads, and both main and tail and drive shafts. VGO engineers in Portland, Ore., instrumented the composite main rotor blade.
"We have over 100 recorded data channels, 45 of which are wireless telemetered by the ATI equipment," Gibson says. "With the exception of the instrumented main rotor blade, Erickson has designed and installed all the various data channel sensors which include strain gages, linear and rotary potentiometers, accelerometers, and ARINC 429 data stream pick-offs.
"For calibration purposes, the instrumentation package including the ATI telemetry was built up in our lab space and used to ensure accurate readings from the strain gages. Calibration loads were typically applied using Erickson-designed and -manufactured custom fixtures and load cells; but, where the instrumented hardware was small enough, we utilized a calibrated Instron tensile test machine to apply the required loads," Gibson continues.
Erickson engineers are working closely with the FAA's Fort Worth, Texas, Rotorcraft Directorate to capture test data to ensure the safety and enhanced performance of the new blade, and enable the successful certification of the composite main rotor blades. Flight testing ranges from the initial hover flight (collecting blade, rotor head, tail rotor, and other levels of strain) to company flight envelope expansion (to prove handling qualities are appropriate and as expected), FAA-sanctioned flight strain survey (the data from which will in part be used to specify loadings for the full-scale fatigue test article) through to performance testing at low- and high-density altitudes that will provide the data to publish flight manual performance limitations.
The plethora of rotating instrumentation required for these tests proved challenging, despite Erickson's extensive experience with flight tests. ATI provided the bespoke equipment to bridge the dynamic-to-static interface.
"For all the sensors installed, the environment is extremely challenging. The levels of vibration, while significantly reduced by the new blade, and exposure to dynamic environments were and still are a challenge," Gibson says. "Where strain gages are in areas only accessible by significant disassembly - for example, the gearbox main shaft - we installed and calibrated redundant sensors to account for any possible loss during the test program. Up to this point in time, we have had very few sensor failures, and none in areas requiring disassembly. The CMRB strain gages that are exposed to sunlight, high-g loading, and intense aerodynamic forces have been extremely robust."
Incorporating this equipment onto the airframe and, in particular, installing the data acquisition unit into the cockpit has turned the S-64 aft piloting station into a flight test engineer's (FTE's) office, Gibson says. The FTE runs the equipment, monitors test parameter alarms, and coordinates with the flight crew to navigate through each flight test card.
"The use of reliable and easy-to-use instrumentation is the key to successful flight test," Gibson says. "Loss of a test card's worth of data results in re-flight that is expensive and inefficient. If the FTE can run the system easily in the challenging environment of a helicopter cockpit, your data is that much more reliable and in need of far less re-testing." (For more on Erickson Inc.'s composite main rotor blade and flight testing, visit Intelligent-Aerospace.com.)
NAVAIR needs
The Naval Air Warfare Center Aircraft Division (NAWCAD) at Patuxent River Naval Air Station, Md., is opening a new operations center for NAWCAD's Atlantic Test Ranges (ATR) to support simultaneous test operations for current and future naval aviation programs, including unmanned systems and live, virtual, constructive (LVC) battle space environments.
"The new operations center will help us meet the requirements of future major Navy programs, reduce scheduling conflicts, and provide more secure information-processing capability for our test ranges. That, in turn, supports delivering new systems to the fleet faster," says Rear Adm. Shane Gahagan, NAWCAD commander.
NAWCAD's Atlantic Test Ranges provide full-service support of testing and training for naval aviation aircraft and aircraft systems throughout their service life. The 17,000-square-foot addition to the existing ATR facilities at Patuxent River Naval Air Station will include secure, multipurpose mission test cells built to support current and future flight test programs, such as the MQ-25A Stingray, Next-Generation Jammer, Next-Generation Air Dominance platform(s), and the Unmanned Aircraft Common Control Station, along with system-of-systems interoperability efforts, officials say.
"ATR is always pushing to remove constraints and provide the capabilities that naval aviation test programs need," says Robert Vargo, ATR director. "I'm excited because this facility will provide well into the future the capacity and capability to get the mission accomplished on time. In short, this addition allows us to support the future now."
In July 2016, Rohde & Schwarz won a potential $1.56 million NAVAIR contract for as many as 338 Model R&S RTE1054 digital oscilloscopes. Digital oscilloscopes acquired through the five-year, indefinite-delivery/indefinite-quantity contract will support the Department of the Navy Metrology and Calibration (METCAL) program, fulfilling NAWCAD's oscilloscope requirements.
The Naval Air Warfare Center Aircraft Division supports the research and development, engineering, test, and evaluation of all Navy and Marine Corps air vehicle systems and trainers, as well as manages test ranges, test facilities, laboratories, and aircraft necessary to support the fleet's acquisition requirements.
NAVAIR METCAL equipment funding is used to procure Calibration Standards (CALSTDs) and ancillary equipment for aviation fleet intermediate calibration activities, fleet training activities, and Aviation Navy Calibration Laboratories (NCLs) to support aviation organizational- and intermediate-level maintenance assets.
Electronic warfare
Investment in test and measurement is growing at a modest rate for the aerospace and defense sector, says Keysight's Haynes. "However, certain segments are seeing much larger growth than others. With the military's focus on dominating the electromagnetic spectrum, we see significant growth in the electronic warfare and signal intelligence segments."
Giga-tronics Inc. EW and Radar Test Solutions Director Armand Pantalone in San Ramon, Calif., is seeing an uptick in advanced signal generator (ASG) adoption, and a rapidly growing need for advanced signal analyzers in aerospace and defense. Multiple radar and EW defense contractors are using Giga- tronics' line of agile, coherent, wideband RF synthesizer/RF upconverter products to generate complex radar and jammer signals for radar and EW system stimulation, integration and test, and evaluation, he says.
"NAVAIR, Raytheon Integrated Defense Systems (IDS), and Lockheed Martin Aerospace use our product line extensively," Pantalone says. "Raytheon IDS uses a set of eight signal generators with our coherent system architecture to generate simulated radar targets, plus sending RF uplinks and processing RF downlinks in a sophisticated real-time, closed-loop hardware in the loop (HWIL) test facility dedicated to the integration and test of a well-known air defense system utilizing a missile interceptor with a radar seeker."
At the same time, "Lockheed Martin Aerospace uses the signal generator as an RF upconverter and the signal analyzers as an RF downconverter in its Modular Adaptable Radar Simulator (MARS) to do completely closed-loop testing of EW systems," Pantalone adds. "Raytheon IDS also chose both the signal generator and signal analyzers as the heart of its new EW simulator upgrade to the long-established Radar RF Target Generator and HWIL facility for testing surveillance and tracking functions of an air and missile defense radar system."
Giga-tronics' product engineers are developing an integrated test suite, called the Threat Emulation System (TEmS), for NAVAIR in Point Mugu, Calif. The TEmS presents a multichannel, independent, and programmable "multi-ship" dense radar environment threat emulator to stimulate the systems under test, Pantalone explains. "For this program, we partnered with Lockheed Martin's Aerospace group to develop the ability for the client and end user to script some dense target and threat environments that are tactically realistic with a very user-friendly software interface. That integrated system and solution is on track to ship before the end of 2016."
RF test
System complexity continues to grow and drive the need for more sophisticated test equipment. Aerospace and defense organizations have a need for "more and more sophistication and complexity in creating more tactically realistic test environments for radar and EW systems," Pantalone says. It is no longer enough, he says, for an engineer to compare test and measurement equipment solely based on figures such as performance specifications on a data sheet or price.
"Performance parameters like frequency coverage, spectral purity, phase noise, etc. are all well-known and have to be considered no matter what you're looking at or for," Pantalone admits. Yet, in RF test today, "there is a new paradigm, where the operational and program concerns reach way beyond just mere technical parameters and they all must be considered."
In fact, Pantalone recommends considering all major concerns, including operational and technical characteristics, as well as taking a holistic view of test. "Mil/aero engineers and engineering managers shouldn't just think of selecting test and measurement equipment as parts, but to think of the big picture now that fully designed and fully integrated test solutions and test environments exist and are commercially available."
One wideband solution that works across several programs or the company's product line makes a lot of sense versus "narrow-banded" and purely custom designs that support only one program, each having their own design costs, risks, and delivery/time-to-capability schedules/timelines, Pantalone says.
Measuring performance
Engineers at RF-Lambda, a manufacturer of passive and active RF and microwave components and subsystems in San Diego needed test and measurement instruments capable of delivering a high degree of accuracy and repeatability to help solve real-world measurement challenges.
They selected Rohde & Schwarz to provide the R&S ZVA vector network analyzer and R&S FSW signal and spectrum analyzer after an in-depth analysis. The measurements evaluated performance parameters that are essential for optimizing the performance of RF-Lambda's components and modules for end users.
RF-Lambda's product testing faces tough measurement challenges on a daily basis due to performance requirements such as high dynamic range and linearity, low noise floor, high peak to average ratios, and ultra-wide frequency bandwidth. Engineers selected several of the company's components for comparative tests: Model RFDAT0118G8A and RFDAT0040G5A digital control step attenuators, Model RFPSHT450M1D8 digital step phase shifter, RLNA00M50GA high-gain low-noise amplifier (LNA), and a custom transmit/receive module for an airborne application at 67 GHz.
RF-Lambda engineers were having difficulty achieving repeatable measurements of phase continuity over the full bandwidth of the attenuator and phase shifter components. They worked with Rohde & Schwarz engineers who made the same measurements using the R&S ZVA vector network analyzer, which was able to make measurements that represented the true performance of the components across the measurement band.
With the R&S ZVA, RF-Lambda engineers were able to adjust phase and amplitude in very fine increments, which is important when testing digital controllable step attenuators and phase shifters widely used in orthogonal frequency division multiplexing (OFDM) and phased array radar systems. At the same time, the very low noise floor of the R&S FSW signal and spectrum analyzer enabled the design team to measure phase noise performance of the transmit/receive module directly and at frequencies up to 67 GHz, eliminating the need for corrective noise cancellation techniques, external mixers, and a separate, dedicated phase noise test system, officials say.
"By evaluating [the Rohde & Schwarz instruments] using measurement challenges we were actually facing, their superior characteristics became all the more evident," explains RF-Lambda Director of Engineering Michael Liu. "In addition, the Rohde & Schwarz technical support team was very responsive and helped us optimize our test results."
Radio communications
As military radios evolve into more complex systems, the need escalates for sophisticated portable testing solutions, affirms Tilley of Astronics Test Systems. Field testing is an area of growth in aerospace and defense, as is at-platform testing for communications systems on aircraft, he says.
The Australian Department of Defense invested in a new tactical radio system; yet, they did not have a solution to test the radios in the field and shipping radios back to a depot for testing is time consuming and expensive, Tilley says.
Seeking a faster turnaround, they purchased the Astronics CTS-6000 radio test sets. "These portable devices provide more than 12 synthetic test instruments in a single tablet-sized device, making it easy to perform tactical radio testing at the operational level. Today, more than 100 units are deployed, and their technicians are being trained on the devices both in the classroom and in the field," Tilley adds. "By bringing the test system to the point of use, the Australian DOD expects to save time, cost, and reduce frustrating 'no fault found' errors."
U.S. Marines pack test systems on trucks for portability. Astronics' VIPER/T test system is used in the field to test anything from laser sights on weapons to Javelin missile electronics. Astronics Test Systems assisted the Marines in modernizing this legacy system, Tilley explains. "After a trade study and analysis, Astronics provided an updated configuration for the test equipment, which included upgrading the digital test capability, a modernized controller, some analog instruments such as a digitizer, and other equipment. The Marines will be rolling out a fresh, updated solution in the coming year for a Foreign Military Sales (FMS) requirement."
Mission-critical systems test
Military personnel understand well the importance of reliable, capable communications. It is not surprising, then, that defense departments worldwide insist on accurate test solutions to ensure communications equipment is functioning as intended.
An undisclosed international military organization has selected the GENASYS mixed-signal test system platform from Marvin Test Solutions in Irvine, Calif., to assure the mission readiness of audio, video, and communications systems and other critical electronics on state-of-the-art armored infantry vehicles. Marvin Test won a contract to deliver multiple TS-321 test stations, as well as test programs, spares, and training.
The GENASYS platform is designed for mission-critical electronics applications - at the board, box, or system level - such as satellite payloads, platform management systems, armament electronics and subsystems, and flight management and control systems, officials say.
"GENASYS offers a compact, flexible, scalable system designed to address the complex current and future test requirements of military and aerospace applications," says Stephen Sargeant, CEO of Marvin Test Solutions and a retired U.S. Air Force major general. "Designing a system with future upgradeability in mind provides the ideal solution for customers whose test requirements evolve with every new advance in technology."
The future of military radio likely lies in long-term evolution (LTE), the commercial cellular market's 4G mobile communications standard. U.S. Department of Defense (DOD) officials are investigating the feasibility of LTE and LTE-Advanced technologies to modernize military communications. "As the U.S. DOD begins to research and adopt commercial LTE technologies for tactical radio purposes, our R&S CMW500 has been readily adopted for many of these advanced research needs," says McCarthy of Rohde & Schwarz.
Forward momentum
Aerospace and defense organizations are increasingly replacing test systems that have gone obsolete, after being fielded for decades, with modern, expandable test solutions - and doing so to save money, says Marvin Test Systems' Sargeant.
"At some point, the cost of sustaining older, obsolete equipment gets to be a number that's too large to continue to fund," Sargeant explains. Aerospace and defense organizations, especially prime contractors, are hitting that threshold and are looking for a test solution that can meet current specs, capture a decade or more of requirements, and offer the modularity, scalability, and flexibility to support future applications and requirements.
Aerospace and defense officials are looking for a test platform that can "overcome the legacy problems of cost, time, and less-than-efficient use of engineers to keep the system running," Sargeant says. Two defense primes have moved to Marvin's GENASYS platform, using its software tools to transition their test plan sets (TPSs).
"TPSs are extremely expensive to create from scratch; [our software] enables engineers to clean up those TPSs to make them more efficient. They are using their engineering talents to refine and build TPSs rather than putting money and effort into maintaining [a legacy] platform," Sargeant says. "Especially in a time of fiscal constraint, companies need a test solution to meet requirements, grow with them as their requirements grow, and overcome issues with obsolescence they've had for decades."
Portability and future proof
Tilley and his colleagues at Astronics Test Systems advise customers "to 'design with headroom,' which is to design so that your test technology can evolve as your system technology grows in the future," he says. "We also suggest customers keep in mind the value of synthetic test instruments.
"Synthetic instruments can form a block of technology to provide many different functions without buying say, up to 12 cards with 12 different functions. So, consider synthetic first as a way to save technical complexity, size, weight, and cost," Tilley suggests.
Astronics, in collaboration with National Instruments, introduced several new PXI test instruments this year, including a rubidium, a pulse generator, and a new digital test instrument - designed to provide familiar, fast development paths for legacy and new military and aerospace programs. The new releases "carry backward-compatible test sets so that they can be used to upgrade older VXI systems with fresh, new, PXI-based technology," Tilley says.
"The challenge of lowering cost and preserving legacy investment in the face of rapid technology change requires industry collaborations for success and attention to software compatibility," says Luke Schreier, director of automated test product marketing at National Instruments (NI) in Austin, Texas. "The NI and Astronics collaboration preserves technology investment for our mutual customers and fosters innovation."
Digital subsystems continue to play a crucial role in most aerospace and defense test platforms, adds Brian Price, executive vice president and general manager at Astronics Test Systems. "With the introduction of these new Astronics PXI Express products, engineers can now expand on today's test platforms to support tomorrow's military and aerospace requirements and maintain their original TPS investments."
The new digital subsystem includes the latest parallel digital, serial, and bus protocols, while also taking advantage of the PXI platform's high speed, small size, and lower cost. "These PXI instruments round out our line of VXI instruments so that we can continue supporting the aerospace and defense automated test systems of yesterday, today, and tomorrow," Price says.
Future functionality
Aerospace and defense professionals will need far more sophistication, complexity, and capability to fulfill far more test needs and requirements in much smaller, more affordable, off-the-shelf, integrated solutions and individual products, Giga-tronics' Pantalone predicts.
Customers are always looking to make testing equipment smaller, more functional, and more cost-effective, says Astronics' Tilley of the future of test and measurement. Astronics Test System engineers put portability and connectivity at the forefront of everything they design, he says, and deliver features like over-the-air-testing and synthetic instrumentation in new systems.
"Much like the fact that today you can hold a spectrum analyzer in one hand and buy that unit for $10,000 or less is just what we will have and are driving to for the future for more applications in the RF test space. We already have and will continue to develop incredibly capable and integrated, agile, coherent, wideband RF radar and EW system test and measurement suites that fit in single racks and even in man-portable carry cases," Pantalone explains.
"These commercial off-the-shelf (COTS) solutions operate in real time and in closed-loop fashion and can support multiple programs across multiple radar bands in a single product," Pantone adds. "These products are already modular and scalable, with their capability only limited today by the processing power controlling the units, and at a fraction of the cost of the far less capable and larger test instruments and behemoth test suites of days gone by."
Too often engineers and engineering managers get focused on a single key attribute when selecting test and measurement equipment, admits Keysight's Haynes. "It used to be a key specification, but today it is more often price. I encourage the companies that we work with to evaluate the total cost of ownership and view it as an investment to reduce risk and cost to the project. A good evaluation should take into consideration the entire life of the solution with respect to not only capital cost, but support and reliability."
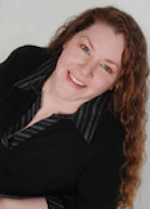
Courtney Howard | Executive Editor
Courtney, as executive editor, enjoys writing about all things electronics and avionics in PennWell’s burgeoning Aerospace and Defense Group, which encompasses Military & Aerospace Electronics, Avionics Intelligence, the Avionics Europe conference, and much more. She’s also a self-proclaimed social-media maven, mil-aero nerd, and avid avionics geek. Connect with Courtney at [email protected], @coho on Twitter, and on LinkedIn.