DARPA picks SUSTAIN Lab for simulation, test and measurement for evaluating future heavy-lift seaplane
ARLINGTON, Va. – A U.S. military researchers needed realistic ways to test and evaluate a futuristic heavy-lift seaplane and its ability to operate in rough seas for weeks at a time. They found their solution from the University of Miami's Alfred C. Glassell Jr. SUSTAIN Laboratory in Miami.
Officials of the U.S. Defense Advanced Research Projects Agency (DARPA) in Arlington, Va., chose the SUSTAIN Laboratory for the Liberty Lifter Wing over Wave test project.
The SUSTAIN Laboratory -- short for SUrge-STructure-Atmosphere Interaction -- will provide test and measurement of a large-scale aerodynamic model of a canonical wing in ground effect over waves, which is a crucial part of the Liberty Lifter program.
Liberty Lifter aims to design an affordable seaplane able to operate efficiently in ground effect lower than 100 feet above sea surface, fly as high as 10,000 feet, and enable efficient theater-range transport of large payloads at speeds far exceeding existing sea lift aircraft.
Liberty Lifter will use low-cost marine manufacturing to build a seaplane able to operate independently of runways and ports, and able to carry loads of cargo, military equipment, and warfighters as heavy as 100 tons.
It's particularly important for Liberty Lift aircraft developers to use simulation to determine how the aircraft design will behave in and above heavy sea waves, and how the aircraft will behave in ground effect with heavy doses of sea spray. Aurora Flight Sciences Corp. in Manassas, Va., and General Atomics Aeronautical Systems Inc. in Poway, Calif., are working on the Liberty Lifter design.
The SUSTAIN Laboratory will evaluate a large-scale aerodynamic model of a canonical wing in ground effect over waves to help with the Liberty Lifter design.
SUSTAIN will provide the facility to conduct the experiments including the model mount and any necessary instrumentation and data collection systems; provide aerodynamic and hydrodynamic testing and wind and wave generation for the experiments; and calibrate wind and wave conditions to support testing. The lab will conduct these experiments in September and October 2024.
The SUSTAIN laboratory combines a wind tunnel and wave tank to study the effects of high winds and significant sea surface motion on a variety of structures. It has a 23-by-6-by-2-meter test area and a water tank one meter deep. Its wind tunnel can produce winds as fast as 120 knots, and can simulate wave action of high sea states in open ocean conditions.
Liberty Lifter focuses on a seaplane with extended maritime operations in high sea states that is affordable to produce, and that involves complex flight and sea surface controls.
The project's long-range seaplane will provide smooth operations in ground effect in waves that are four to eight feet high. Ground effect describes the added aerodynamic buoyancy produced by a cushion of air below an aircraft moving closely to the ground or surface of the water.
Flight will be smooth while flying over waves as high as eight to 13 feet, with high lift at low speeds to reduce wave impact loads during takeoff and landing in waves from 4 to 8 feet high. The seaplane will accommodate wave impact loads and be able to operate in high-traffic areas. The aircraft should be able to operate at sea for weeks at a time with long periods between land-based maintenance.
DARPA researchers are emphasizing low cost, easy-to-fabricate designs, with Liberty Ship-style manufacturing. The seaplane also should have complex aero and hydrodynamic interactions during takeoff and landing, with advanced sensors and controls to avoid rogue wave impacts.
The Liberty Lifter seaplane should be able to take off and land in waves from four to eight feet high; fly in ground effect above waves from 8 to 13 feet high; fly at altitudes from ground effect to 10,000 feet, and operate for four to six weeks at a time carrying payloads of at least 90 tons.
On-water amphibious payload deployment and retrieval should be via nose and tail ramps; the seaplane should be able to carry at least two U.S. Marine Corps Amphibious Combat Vehicles, and cargo in 20-foot container units.
Liberty Lifter seaplane designers should use high-performance computing and multi-disciplinary analysis and optimization tools to model and analyze complex aerodynamic and hydrodynamic interactions; focus on affordable design and manufacturing approaches; use novel manufacturing approaches; and use industry best practices from commercial high-speed vessels. The program consists of a three-phase developmental cycle with each phase building on the previous phase.
For more information contact the Alfred C. Glassell Jr. SUSTAIN Laboratory online at https://sustain.earth.miami.edu/index.html, or DARPA at www.darpa.mil/program/liberty-lifter.
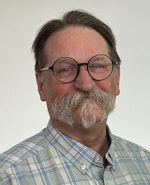
John Keller | Editor-in-Chief
John Keller is the Editor-in-Chief, Military & Aerospace Electronics Magazine--provides extensive coverage and analysis of enabling electronics and optoelectronic technologies in military, space and commercial aviation applications. John has been a member of the Military & Aerospace Electronics staff since 1989 and chief editor since 1995.