AI, machine learning driving embedded bus-and-board development
While the best defense agency assets likely will remain the men and women in uniform in the near future, the U.S. Department of Defense (DOD) experts have their eyes on the cutting edge as they look to leverage the incredible computing power at their disposal by integrating artificial intelligence (AI) and machine learning to help warfighters dominate the battlefields of tomorrow.
When asked what the design and technology-based trends in bus-and-board embedded computing architectures for military and aerospace applications are, industry experts say it hinges on size, weight, and power consumption (SWaP), cooling the increasingly-powerful systems, and enabling AI and machine learning.
Defense customers still are trying to solidify how best to harness and apply AI for military use, says Jim Shaw, executive vice president of engineering at Crystal Group Inc. in Hiawatha, Iowa.
“You’re seeing the need for hardware that can go do these types of functions. The military is still trying to figure out what they are doing with artificial intelligence,” Shaw says. “They have plans to go in and do maintenance and medical applications in theater. The real emphasis is on getting the combat solutions and how to augment the soldiers’ perceptions as the person is under that pressure and getting situation awareness handed to the soldier or small crew. It’s about getting them informed.”
There are four trends in the bus-and-board embedded world, says John Bratton, product marketing director for Mercury Systems in Andover, Mass. Those include SWaP; straight-forward performance; an increasing emphasis on open-system architectures and interoperability; and increased features, capabilities, and applications.
Cutting edge while cutting costs
Companies like Crystal and Mercury use increasingly powerful components that are commercial-off-the-shelf (COTS) as they develop the systems of tomorrow.
“There’s more impetus on acceleration in changes than ever before,” Bratton says. “It’s becoming a more commercial base. Smart everything — artificial intelligence, machine learning, platform control — we’re seeing that in more converged boxes. More things going into the same box; not just the processing ability, but the need to make it secure.”
Standards also are playing a big part in today’s military electronics designs. “We’re seeing an emergence of the government, the DoD, in driving standards. SOSA [Sensor Open Systems Architecture] is the classic example, Mercury’s Bratton continues. “They’re doing it for affordability, but they’re also doing it for interoperability and scalability. From a performance point of view, we’re finding that these innovations ... need efficient cooling — liquid cooling. At the same time, more and more cloud-like applications and you can put all of those capabilities on the smallest platform.”
Keeping cool
The more computing power you pack into an enclosure, and in on-the-ground military or other extreme temperature, dust, water, or space applications, those systems are almost assuredly in a ruggedized box or sealed enclosure which makes heat dissipation difficult.
Shaun McQuaid, Mercury’s director of product management, explains that liquid cooling systems not only would help mil-aero components beat the heat, but also that the more compact, heat-rich systems would spur innovation from industry in liquid cooling technology.
“What is driving the trend with liquid cooling — you need to dissipate more energy,” McQuaid says. “Systems that have cooling are looking to leverage that. The tech that drives liquid cooling, the drip sensors and things like that to build a liquid cooled system that is deployable.”
Crystal’s Shaw says his company also is working hard to maintain computing power inside an increasingly hot and crowded enclosure.
“The biggest challenge there is the size of the package has to be relatively small, but the power of the package is relatively large,” remarked Shaw. “That’s what my guys and gals are working on now. Most everything we build is purpose built. Heat transfer technology to take heat away from CPUs and GPUs. The challenge is really doing that effectively while keeping the size of the box manageable.”
A rugged design also is important, Shaw says. “The other thing you’ve got to consider is put all of this together that can take a nearby explosion and IED [improvised explosive device] hit and the shock and vibration has to be stellar. We’re primarily focusing on the Army applications.”
Rugged servers
Mercury’s Ensemble LDS3517 Xeon D embedded server with support for field-programmable gate arrays (FPGAs) and switched mezzanine card (XMC) modules marries a server-class Intel processor with the Xilinx UltraScale family of FPGAs in the 3U OpenVPX form factor. Mercury handles cooling for Intel’s Xeon D processors using VITA 48 standard approaches that involve convection, conduction, air-flow-by, or air-flow-through.
“VPX — it’s the most rugged out there — is a good choice,” Bratton says. “They optionally have embedded security in them, so they can be deployed anywhere. Everything about them should be trusted, from the code, to who has access to them, to where they’re made, and where the components come from.”
Mercury officials say their Ensemble LDS3517 is a balanced and affordable building block for radar, electronic warfare and mission processing applications with tight SWaP requirements. The Ensemble LDS3517’s Xeon D processor has a peak performance of 410 billion floating point operations per second (gigaFLOPs), with 16 gigabytes of DDR4 system memory, with an expansion to 32 gigabytes planned.
“Commercial trends are being mirrored back into defense,” says Mercury’s McQuaid. “Not only in the federated approach, but also in the areas of artificial intelligence and machine learning. The components that enable this and optimize this, from Intel that are optimized for artificial intelligence and machine learning are put into our product line and support this mission. We look at GPU [graphics processing unit] architecture and optimize and secure those and do all of that under open standards SOSA and on the software side.”
In a more robust air-flow-by configuration, the server can operate in temperatures from -40 to 60 degrees Celsius. With the conduction cooled option, the LDS3517 can operate up to 71 C.
The Mercury Systems EnsembleSeries HDS6605 6U OpenVPX scalable Xeon-SP blades feature a 1.9 GHz, 22-core Xeon SP (Cascade Lake) server-class processor that also meets open-system architecture, high computing power, and robust thermal management.
With 96 to 192 gigabytes of on-board DRAM, the processing power of these blades is suited to next-generation radar, electro-optical/infrared (EO/IR) and complex image intelligence (IMINT), AI, machine learning, deep learning, and converged sensor applications.
The HDS6605 complies with VITA 48.7 standard with the air-flow-by cooling option as well as VITA 48.4 with its open-standard liquid-flow-through cooling option.
Rugged, embedded
Crystal Group officials unveiled their company’s RE1529 rugged embedded computer early this year, which features COTS technologies in a compact, rugged enclosure for challenging applications, harsh conditions, and extreme environments, including vibration-intense helicopter applications. The RE1529 is designed and tested to meet or exceed MIL-STD-810 and comply with Export Control Classification Number (ECCN) 5A992.
The Crusta RE1529 is manufactured with lightweight composites and delivered with Xeon D multi-core processors, up to 128 gigabytes of ECC DDR4 RAM, nine internal 7 or 9-millimeter SATA solid-state drive (SSD) bays, and flexible I/O in a rugged package measuring 6 by 15.4 by 9.6 inches and weighing 7.5 pounds.
“Providing server-class performance in a compact, embedded footprint, our latest rugged embedded computer, the RE1529, couples a 16-core Intel Xeon D processor with data storage capacity in a customizable, scalable system to meet both current and future requirements,” Shaw says. “The RE1529 is designed and tested for SWaP sensitive applications including airborne and transit case use with a minimal foot print, wide range voltage inputs. The system is virtually maintenance free with top performance in harsh conditions including temperature extremes, high shock and vibration, high humidity, high altitudes, and dust.
C4ISR in mind
Kontron America Inc. in San Diego announced its SOSA-aligned VX305H-40G 3U OpenVPX single-board computer this past spring. The single-board computer (SBC) uses the Intel Xeon-D microprocessor and 40/10 Gigabit Ethernet networking in a package that is compatible with the U.S. Army Command, Control, Communications, Computers, Intelligence, surveillance and Reconnaissance (C4ISR) / Electronic Warfare (EW) Modular Open Suite of Standards (CMOSS) standard.
Designed to the VITA 65 slot profile SLT3-PAY-1F1F2U1TU1T1U1T-14.2.16 compute-intensive embedded computing board profile, the VX305H-40G combines the computational power of the 12-core Intel Xeon D-1559 processor with several high-performance data pipes, including a 40 Gigabit Ethernet data plane, a second 10 Gigabit Ethernet data plane, a 10 Gigabit Ethernet control plane, and an 8-lane PCI Express Gen 3 expansion plane port.
Other features of the VX305H-40G include a Kontron-designed VITA 46.11-compatible intelligent platform management controller (IPMC) to provide systemwide health management, sequenced system power-up, and temperature/power/performance management to handle image processing and other signal processing applications.
Made for security
Aitech of Chatsworth, Calif., has released its C877 SBC, which provides standard Intel CPU security features (TXT, AES-NI, etc.), as well as an on-board TPM 2.0, and SSD options, and has expanded security protection from AES256 encryption, quick erase, and secure erase features. Aitech has also included several customized security features with its AiSecure board architecture, which includes tamper detection and options for board security features and encryption that can be customized in the optional Xilinx Zynq UltraScale+ FPGA.
The C877 is designed with a high-bandwidth bus architecture and an assortment of on-board I/O interfaces, with an XMC site for additional I/O options. The board is available in air- and conduction-cooled versions.
The rugged 3U VPX single-slot SBC has a trio of Intel CPU options including a pair of Xeon D processors, as well as a Pentium D-1519 option, and can accommodate up to 32 gigabytes of DDR4 RAM. The Aitech SBC supports Linux, Windows, and VxWorks operating systems.
Up in the air
New Wave Design & Verification in Minneapolis has its eyes on the skies with its V1142 quad-port 1394b-AS5643 PMC/XMC FPGA card suitable for embedded avionics and avionics test platforms. New Wave Design & Verification’s card uses only one FPGA chip for high port density, with an emphasis on SWaP. This on-board FPGA provides bus control, diagnostics information, interface choices, and customization options not previously available.
The V1142 offers four front-panel transformers coupled with 1394b ports, as well as eight rear-panel non-transformer coupled ports. The host interface is Gen2 x4 PCI Express. The V1142 is available in air and conduction-cooled XMC form factors and is VITA 42.2 and 61.0 compliant. New Wave notes that the V1142 can be reloaded with the following IP cores: 1394b PHY, 1394b OHCI Link Layer, 1394b GP2Lynx Link Layer, and the 1394b AS5643 Offload Engine.
Going further, sooner
The U.S. Air Force is looking to take AI and machine learning a bit further — and higher — in the next five years as the military branch announced this spring that it would be spending nearly $100 million to shrink the size, weight, and power consumption of embedded computing systems suitable for avionics. The Air Force is looking beyond AI and machine learning into creating a deep learning system for the cockpit.
In its solicitation, the Air Force noted it was “Seeking innovative research to develop advanced efficient computing architectures and systems, as well as robust algorithms and applications, in order to achieve orders of magnitude improvement in size, weight and power, for deploying robust artificial intelligence and machine learning capabilities in an embedded computing environment.”
While trends in embedded bus-and-board systems are starting to show what’s possible in AI and ML, the DOD, unsurprisingly, is eyeing lassoing the power of machine learning and will no doubt drive trends in that sector in the coming years.
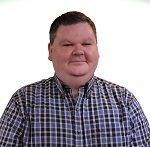
Jamie Whitney
Jamie Whitney joined the staff of Military & Aerospace Electronics and Intelligent Aerospace. He brings seven years of print newspaper experience to the aerospace and defense electronics industry.
Whitney oversees editorial content for the Intelligent Aerospace Website, as well as produce news and features for Military & Aerospace Electronics, attend industry events, produce Webcasts, oversee print production of Military & Aerospace Electronics, and expand the Intelligent Aerospace and Military & Aerospace Electronics franchises with new and innovative content.