Embedded computing sensor and signal processing meets the SWaP test
NASHUA, N.H. - Electronic sensors are ubiquitous in defense, aerospace, and commercial systems, ranging from weapons seekers to smart phones, and the use of sensors is expected to grow as electronics size, weight, power consumption, and cost (SWaP-C) continue to drop.
On the face of it, that sounds sound great. The U.S. military is developing networks of sensors to give commanders eyes and ears everywhere from the seabed to space in efforts maintain a high state of global vigilance.
Practically, however, that means intelligence analysts are drowning in data, which makes distilling actionable intelligence out of oceans of data a difficult, costly, and time-consuming task. The answer to this dilemma lies in new generations of sensor and signal processing computers that bring capabilities like artificial intelligence (AI), parallel processing to the fore to tame the data monster and render mountains of data into assets rather than adversaries.
Mountains of sensor data
“We are experiencing a huge increase in the amount of data throughput our customers are requiring,” says Jim Tierney, vice president of defense and aerospaceThis creates challenges in packaging and interconnects. “As more data over an increasing number of connections grow within such a tight space, the density of wire harnesses increases, which runs the risk of insulation compression failures, especially in extreme environments when the system is enduring rugged conditions. This can cause signal integrity issues and potential failures, which is not an option,” Tierney continues.
One challenge that Atrenne engineers have faced involves unmanned aerial vehicles (UAVs). “We work with a drone manufacturer that is acquiring data from cameras, both visual optics and IR, and displaying to a ground-based computer a topographical video of a landscape from over 60,000 feet in the air,” Tierney says.
“Pointing out threats and opportunities in real-time, troops are more aware of the situation when occupying unknown territories,” Tierney continues. “The data load and processing requirements are massive. Between the shock and vibration caused by take-offs, landings, and turbulence, plus temperature and pressure variants, the embedded bus architecture and associated I/O medium needs to match the impedance characteristics to ensure flawless performance in moving the increased data required by today’s leading-edge ISR platforms.”
Challenges of ever-increasing amounts of sensor data are not expected to go away anytime soon. “Platforms are giant vacuum cleaners of the RF spectrum,” says Shaun McQuaid, director of product management at sensor-processing specialist Mercury Systems in Andover, Mass. “That means we’re seeing the amount of data expand so significantly, that commercial technology is being leveraged to handle those data streams.”
Essentially that involves repackaging commercial data centers and high-performance networks as rugged embedded computing systems for aircraft, surface ships, submarines, land vehicles, and spacecraft — even for platforms as small as UAVs. This imposes difficult challenges on systems designers to deal not only with SWaP-C, but also with electronics cooling and thermal management; A/D and D/A converters; and finding the right mix of heterogeneous computer architectures that consist of central processing units (CPUs), field-programmable gate arrays (FPGAs), and general-purpose graphics processing units (GPGPUs) to handle the growing demands of sensor and signal processing.
“Where we have been is like setting up a home network on the platform,” Mercury’s McQuaid explains. “Today it is like setting up a small business on the platform, and doing a bit more. Where we are going is a true data center on the platform, with all the cloud computing infrastructure developed in the commercial world up at the front end doing AI and pre-pruning of all that sensor data.”
Moving processors to the antenna
One of the primary ways that computers can deal with data overload is by preprocessing as it comes into RF and optical antennas. This involves digitizing the incoming analog signal as soon as possible, and performing some digital processing on the data before sending it on to heavy-duty processors elsewhere on the platform or on the network.
“They are digitizing right at the aperture now,” says Marc Couture, director of C5ISR product management at the Curtiss-Wright Corp. Defense Solutions divisionThe job often is more difficult than it sounds. “We are seeing this distributed architecture more and more where sensors are on a mast, and we see local RF and signal processing happening right there at the antenna,” says Rodger Hosking, vice president of Mercury Microelectronics, a wholly owned subsidiary of Mercury Systems (formerly Pentek) in Upper Saddle River, N.J. “We are eliminating a lot of noise and other things that can be picked up by RF cables.”
Think of a data stream with noise, irrelevant information, and other extraneous material already eliminated before the data moves on to main processors. “Sometimes the DSP [digital signal processing] functions can do some local DSP functions that will reduce the amount of data that has to be sent down to the host,” Hosking says.
Although the notion of moving pre-processors closely to antennas isn’t exactly new, what is changing is the size of the pre-processors. “We were talking about a processing system next to the antenna, and now we are talking about that processing system resolved to a chip, where it used to be a couple of cards in a box,” says Mercury’s McQuaid. “It can be done on a chip, and that is a SWaP win. It also eliminates the problem of RF cabling from antenna to box, and gets it closer to the commercial model: routing and switching.”
Shrinking the size of preprocessors next to antennas has other design implications, as well. “As we get it closer and closer to the antenna, it frees-up size, weight, and power elsewhere in the system,” McQuaid says. “Now those spaces are being filled with other digital processing equipment.”
Influential applications
So what does all this capability bring to the table? “Application-wise, things like radar, EW [electronic warfare] image processing, and EO/IR [electro-optical andAnother potential application is intelligence, surveillance, and reconnaissance (ISR) with unmanned aerial vehicles with onboard sensors and sensor processors. “If you have a drone exploring a warfighting region, with these types of processors, this drone will be able to pick up signals to see what’s down there at the RF spectrum, and redirect its mission and concentrate over regions with interesting features,” says Mercury Processing’s Hosking.
In addition, this kind of processing could enable several users on a network to use the same deployed sensor for different kinds of intelligence gathering. “One sensor could be distributed across a network to multiple users,” Hosking says. “SIGINT [signals intelligence], radar, and image processing applications all could operate over network links using that broadband infrastructure. That will get it done.”
Among the opportunities that advanced and networked sensor and signal processing capability provides is a growing use of artificial intelligence, otherwise known as AI, as well as machine learning for military applications. Data center-like embedded computing for digital signal processing can enable onboard processors to make decisions based on what their sensors perceive, learn from their experiences, and then share that information with other platforms in the area.
“I feel strongly that artificial intelligence will play a big role in the future,” says Mercury’s McQuaid. “A lot of this DSP horsepower will be tied to AI applications,” echoes Mercury Processing’s Hosking. “AI can be used to make these unmanned vehicles and similar platforms smarter and more efficient.” Adds Curtiss-Wright’s Couture, “The sensors are all about extracting data. The sooner and faster you can do that, the faster you can make decisions.”
Enabling technologies
Among the technology building blocks that are helping enable SWaP-optimized high-performance sensor and signal processing are fast A/D and D/A converters; network switching; diverse microprocessors; next-generation FPGAs that can contain RF circuitry; and high-performance thermal management and electronics cooling.
“The big technical trends that have had a macro effect certainly are A/D and D/A converters,” says Curtiss-Wright’s Couture. “As the sampling frequencies have increased and the bit resolutions have increased, the analog/digital divide narrows, and the digital circuitry is creeping up toward the apertures.”
Echoes Jeff Bateman, product line manager for FPGAs and networking products for Curtiss-Wright Defense Solutions, “The digitization aspect and direct RF conversion can help capture and analyze more of the electromagnetic spectrum.”
New generations of data converters are making the RF spectrum more accessible today than ever before. “You can’t live without some type of RF processing,” says Mercury Processing’s Hosking. “The trend is to make it relatively simple. Now the A/D converters are so wide-bandwidth that you can do more processing after the digitization, which previously might have required sophisticated amplifiers or tuners.”
In addition, the digital processors today offer capabilities that a decade ago couldn’t even be imagined. “With the Intel Xeon processors you have processing engines that can ingest all of this data and do something with it in real time,” says Curtiss-Wright’s Couture. “One of the bigger game-changers is the introduction of GPGPUs. They once were in the sandbox for massive floating-point processing, but now they are bringing in all of the AI that designers need. An EW operator interpreting the data is getting a lot of help now.
“GPGPUs are doing a lot of the heavy lifting, and we are getting into the AI that can identify RF emitters of interest or do imaging processing, so analysts can concentrate on targets of interest that need their attention,” Couture continues.
Now combine general-purpose processors, FPGAs, and GPGPUs in the same system and the capabilities expand exponentially. “We are seeing this kind of heterogeneous architectures, with general-purpose processors, FPGAs, and GPGPUs,” Couture explains. “Different customers and different applications will change the ratios of those components.”
Perhaps the biggest enabling technology in today’s sensor and signal processing, however, involves the latest generation of FPGA systems-on-chip like the VersalThe RF system-on-chip, otherwise known as the RFSOC, “is a huge success for us, and has really changed the game, because it includes the digitizers, the FPGA resources, the ARM processors, and dual-100-Gigabit Ethernet engines,” Hosking says. “That combination of resources has been very effective for distributed architectures.”
Consolidating all those processing resources onto one chip offers huge benefits for system miniaturization, capability, and even for thermal management. “There used to be a lot of discrete parts with a distributed sample clock and trigger,” says Curtiss-Wright’s Couture. Now with it all in the FPGA there are massive benefits. You are not doing that on a printed wiring board and fighting the signal-integrity challenges. The common pool of FPGA logic is all co-located. This type of time difference of signal arrival, all on the same chip, is a big game changer.”
Open-systems standards
Another technology driver with a big influence on today’s sensor and signal processing systems is open-systems standards. Of these, perhaps the most notable is the Sensor Open Systems Architecture (SOSA) standard supervised by The Open Group in San Francisco. SOSA seeks to streamline existing industry standards, such as OpenVPX, to make them accessible for a wide variety of aerospace and defense systems, and help implement a true vendor-neutral design approach.
“SOSA is dominating all the VPX story. I’ve seen only a handful of RFPs and RFIs that were not SOSA related,” says Mark Littlefield, senior manager embedded computing products and system solutions at chassis and networking specialist Elma Electronic in Fremont, Calif.
SOSA “is really all about ease of integration, knowing you can buy these components and it is plug-and-play; it will just works,” Littlefield says.
Other industry standards coming to bear on sensor and signal processing include the small-form-factor VNX standard, which smaller than 3U VPX — circuit board dimensions about the size of a credit card. “With VNX modules you will see new life over the next 18 months, in problems that VPX won’t fit,” Littlefield says.
As an example, he cites the Common Launch Tube for small missiles or UAVs that is about 5.5 inches in diameter. “3U VPX won’t fit; VNX does, but you might need seven or eight VNX problems in that space.”Â
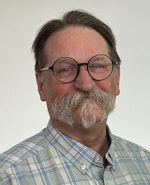
John Keller | Editor-in-Chief
John Keller is the Editor-in-Chief, Military & Aerospace Electronics Magazine--provides extensive coverage and analysis of enabling electronics and optoelectronic technologies in military, space and commercial aviation applications. John has been a member of the Military & Aerospace Electronics staff since 1989 and chief editor since 1995.