DARPA picks RadiaBeam Technologies for ways to test radiation-hardened 3DHI next-generation electronics
ARLINGTON, Va. – U.S. military researchers needed new testing methods for radiation-induced single-event effects (SEE) of high-reliability next-generation electronics. They found their solution from RadiaBeam Technologies LLC in Santa Monica, Calif.
Officials of the U.S. Defense Advanced Research Projects Agency (DARPA) in Arlington, Va., announced a $10.6 million contract to RadiaBeam on Monday for the Advanced Sources for Single-event Effect Radiation Testing (ASSERT) project.
In the 4.5-year ASSERT program, RadiaBeam experts will develop new capabilities for SEE testing of 3D heterogeneously integrated (3DHI) electronic components and circuits, and seeks to transform today's radiation-hardened electronics design process to enable rapid deployment of next-generation electronics for space and nuclear warfare applications.
DARPA officials say they expect to make several contract awards for the ASSERT program, so more announcements can be expected.
Related: The quest for commercial-performance electronics in space
Goals for RadiaBeam include generating energetic particles with penetration as deep as 5 millimeters in silicon with high-radiation-relevant linear energy transfers and beam diameters of less than 0.2 microns. Several contract awards are expected.
RadiaBeam engineers will take-on one ASSERT program technical area for 3DHI radiation-hardened technologies which addresses two technical challenges: deep penetration depths in 3DHI components with space-radiation linear energy transfers; and charge tracks with fine spatial resolution. Proposals must respond to both technical challenges.
Radiation effects threaten electronic systems from three main natural sources: galactic cosmic rays; charged particles trapped by planetary magnetic fields; and solar particle events.
Artificial radiation sources like particle accelerators, reactors, and nuclear weapons also pose threats to electronic systems. Electronics are susceptible to upset, degradation, and failure from total ionizing dose; displacement damage dose; and the instantaneous response to single ionizing particles, such as SEE, which threaten the reliability of the U.S. nuclear arsenal, spacecraft, avionics, and terrestrial systems such as computer server farms and autonomous vehicles.
Linear energy transfer is a key SEE test parameter and measures the energy deposited per unit length as an energetic particle travels through a material. Space-radiation linear energy transfers fall in the range of 0.1 to 100 MeVcm2/mg.
Today, the principal method for SEE testing in the U.S. relies on heavy-ion sources that produce large-diameter beams for part- and board-level radiation qualification of electronics. These sources produce relatively large beam spot areas ranging from a few square centimeters to as large as 60 square centimeters with penetration depths to hundreds of microns.
Emerging advanced electronics are complex and integrated than previous generations, and can combine digital, analog, and optical functions using 3D topologies and several material types. 3D components are expected to reach several millimeters in vertical extent with a complexity and level of integration that will make it difficult, if not impossible, to de-package and disaggregate into parts to perform radiation testing using current heavy-ion sources.
SEE testing of integrated components will require an irradiation source that provides a combination of multi-millimeter penetration depths, space-radiation-relevant linear energy transfers, and fine spatial resolution and control to provide the linear and angular precision necessary to probe sensitive areas and to isolate faults.
Related: Radiation hardening meets smart satellites
Current SEE testing is unable to meet all of these requirements simultaneously, necessitating new sources to qualify next-generation microelectronics for nuclear and space applications that require high reliability in radiation environments.
The process of testing with ion beams is slow and laborious, and problems worsen with the increasing complexity of electronics. As a result, ASSERT sources must be compact and cost-effective so they can be incorporated into the development process.
In this way, radiation qualification will be integrated throughout the design and fabrication flow, with ASSERT sources providing the means to identify radiation design flaws rapidly and to facilitate swift correction and design optimizations. A key program goal is to reduce the time from design to radiation-qualified component by a factor of 10. DARPA researchers particularly are interested in technologies like short-pulse relativistic electron beams and ultrashort pulse X-rays.
For more information contact RadiaBeam Technologies online at https://radiabeam.com, or DARPA at www.darpa.mil.
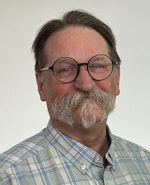
John Keller | Editor-in-Chief
John Keller is the Editor-in-Chief, Military & Aerospace Electronics Magazine--provides extensive coverage and analysis of enabling electronics and optoelectronic technologies in military, space and commercial aviation applications. John has been a member of the Military & Aerospace Electronics staff since 1989 and chief editor since 1995.