Military jet fighters, commercial passenger jetliners, military surveillance aircraft, as well as a growing number of unmanned fixed-wing aircraft and helicopters benefit from technologies designed for dual use.
Manned and unmanned military and commercial aircraft share more common technology than ever before. From fuselages to engines and cockpit avionics to connectors, today's commercial and military jets, helicopters, and unmanned aircraft systems (UAS) leverage innovations from a wide variety of markets, including consumer electronics, automotive, industrial, medical, and more.
"Instead of technology migrating from military avionics to the commercial sector, there is significantly more transfer from the consumer electronics world into avionics in general," says Paul Hart, chief technology officer and technical fellow at Curtiss-Wright Avionics & Electronics in Christchurch, England. "For example, traditional MIL-STD-1553 and ARINC 429 databuses are giving way to Ethernet-based networks on aircraft, along with Wi-Fi connectivity. Also CANbus, used in the automotive industry for decades now, has an ARINC standard and is featuring in many new aircraft designs.
"There are also crossover technol- ogies where other industries have invested in technology development that can benefit aerospace," Hart adds. "For example, we are using a sensor technology originally developed for the medical industry to detect ice accretion on an aircraft wing to much higher accuracies than existing technology. We have also evolved versions of our flight test instrumentation for space applications on launch vehicles, spaceplanes, re-entry vehicles, and space stations."
Benefits abound
Collaboration across aerospace and other industries is increasing, and virtually all involved are benefitting.
Military aircraft are leveraging commercial avionics systems and components, and even fuselages. As a result, military programs are able to save development time and money; benefit from commercial economies of scale for reduced costs, increased product availability, and potentially, reduced threat of parts obsolescence; and boost compliance with safety standards and requirements for flying in public airspace.
Simultaneously, commercial aircraft - from airliners to civil and consumer UAS - are harnessing proven rugged military electronics designed for several decades of usable life and for harsh environments.
Devised for dual use
"Many avionics devices and systems are designed for dual use - commercial and military applications - which not only enables shared capabilities and standards, but also helps to drive down development and qualification costs," Mike Madsen, vice president of aerospace integrated supply chain at Honeywell Aerospace in Phoenix, told Military & Aerospace Electronics in 2011. (Read "NextGen is happening now in avionics systems" from the August 2011 issue online at http://bit.ly/1RJ8EQg.)
The trend of engineering dual-use technologies not only endures, but continues to expand. In fact, virtually every leading prime contractor to the U.S. Department of Defense (DOD) designs and develops technologies applicable across myriad markets, including commercial and military aerospace.
Within Honeywell Aerospace's marketing and product management team is "an Aerospace level, cross-functional organization ensuring technology roadmaps are coordinated to support current future requirements in commercial and military business segments," says Tom Hart, vice president defense and space aftermarket at Honeywell Aerospace in Phoenix. Honeywell's military customer base - original equipment manufacturers (OEMs) and aftermarket - is showing "high interest in commercial off-the-shelf (COTS) or military off-the-shelf (MOTS) when possible to reduce non-recurring and recurring" engineering costs.
"Honeywell Aerospace is very interested in dual use where possible. Significant investments are going into product and technology areas for commercial and military use," Hart says. "For example, Honeywell has developed a family of image processing modules (IPM) used in commercial display systems and military display systems where there is a need for increased processing power and throughput, like in a Synthetic Vision System (SVS) and Enhanced Vision System (EVS)." The same family of IPMs is used for high-end military display generator applications, such as the latest-generation F-15 and F-16.
"The Lockheed Martin F-16 is a great example of a legacy fighter with models delivered 30-plus years ago, but from an avionics standpoint is up to today's standard in technology and capabilities," Hart explains. There are many opportunities to work on modern platforms, he says, but also significant opportunities to apply modern systems to upgrade legacy aircraft.
Convergence
The objectives of commercial and military organizations - from airlines to defense departments - are converging. Both segments focus on acquiring advanced hardware and software having low cost and weight, high availability, an upgrade path for the future, and compliance with industry standards and regulations.
"In general, military aviation authorities around the world are adopting commercial - i.e., Federal Aviation Administration (FAA) and European Aviation Safety Agency (EASA) - [standards] in place of mil-specs, which have become quite dated and irrelevant to the technologies used in new avionics designs," says Curtiss-Wright's Hart. For example, "MIL-HDBK-217F, used widely for predicting reliability, has no consideration for software and field-programmable gate array (FPGA) implementations. There are much better techniques in the commercial world to predict reliability of a processor- based hardware system.
"Certification standards are predominantly based on commercial practices," Hart adds. "For example, the process of designing and manufacturing avionics under Part 21G, certifying against FAA/EASA technical standards, and designing installations under the STC or EASA Part 21J process are very clearly defined and have been implemented by the latest generation of aviation professionals. Also many environmental test labs are better equipped and more familiar with RTCA requirements, such as DO-160G 'shake & bake' than traditional MIL-STD-461 (electromagnetic compatibility or EMC) and MIL-STD-810 (environmental qualification) requirements."
"While there are still many unique military requirements, we definitely see commercial standards, such as RTCA DO-178, coming into the military systems, especially where civilian certification is required (e.g., communication, navigation, and surveillance/air traffic management systems)," Honeywell's Hart explains.
Sharing airspace
Airline passenger traffic is up globally, and growing at an average rate of five percent annually, which is increasing competition for access to airspace among operators of virtually all aircraft, whether commercial airliners, business jets, helicopters, unmanned aircraft, or military aircraft.
"As commercial air traffic expands and the skies become busier, military aviation is having to adapt," says Laurent Lenoir, vice president of the mission and function center of competence at Thales Avionics in Toulouse, France. "With fewer routes reserved exclusively for military air traffic, military aircraft increasingly need to meet civil standards in order to fly in commercial airspace."
The military market benefits from great technology advances primarily driven by commercial airline customers in pursuit of lower cost, lower weight, and high performance and reliability, Honeywell's Hart explains. The RDR-4000 IntuVue in Honeywell's weather radar product line, for example, is fielded in commercial and business aviation aircraft and shares the same hardware and 95 percent of the software with the RDR-4000M fielded on military aircraft, including C-17 and multiple C-130 variants.
"We are seeing similar trends in traffic collision avoidance systems (TCAS)," Hart says. "The same hardware is used for commercial and military applications, and a reuse of core software adapted to support unique military functions. We are also using our family of TCAS processors as a core element in sense-and-avoid systems for larger UAS.
"Another area where core technology is used in commercial and military is navigation and, in particular, inertial navigation," Hart adds. "The same core Ring Laser Gyro is used in Honeywell's commercial Laseref inertial navigation family and H-764G family of Embedded GPS and Inertial systems for the military. The same trend is seen and welcomed in many other technology areas."
Hart also sees greater interest in "open architecture systems and standards. The DOD Future Airborne Capability Environment (FACE) initiative is an example of this trend," he says.
FACE features
The FACE approach is "a government- industry software standard and business strategy for acquisition of affordable software systems that promotes innovation and rapid integration of portable capabilities across global defense programs," as defined by The Open Group, a global consortium "that enables the achievement of business objectives through IT standards."
Many suppliers to defense organizations worldwide take part in The Open Group's FACE Consortium, with the goal of delivering modern, capable, and robust avionics to military aircraft and operators in less time and at lower cost than historically possible through traditional methods and proprietary solutions.
Rockwell Collins in Cedar Rapids, Iowa, is a sponsor and founding member of the FACE Consortium. The company is supporting government development of a standard set of interfaces for Required Navigation Performance Area Navigation (RNP RNAV) capability aligned to the FACE Technical Standard.
Under a U.S. Naval Air Systems Command (NAVAIR) contract announced in January, Rockwell Collins will demonstrate its FACE-aligned Flight Management System application on military representative mission computer hardware in multiple configurations. The company's RNP-RNAV application leverages commercial technologies that are currently operational on commercial and tactical aircraft.
"Our open-architecture Flight Management System software is written for fast and affordable integration across a wide variety of avionics systems," says Troy Brunk, vice president and general manager of airborne solutions for Rockwell Collins. "Its RNP RNAV capability provides full civil airspace interoperability while ensuring timely and efficient mission planning and execution."
Rockwell Collins engineers up- graded U.S. Army CH-47F Chinook multi-mission, heavy-lift transport helicopters - already equipped with the Rockwell Collins Common Avionics Architecture System (CAAS) - with RNP-RNAV technology in 2015. The enhanced capability enables Chinook pilots to operate in and around civil airspace with safety benefits previously afforded only to commercial aircraft, officials say.
"RNP-RNAV provides tactical helicopters with full civil airspace interoperability under current flight rules. It eliminates the need to obtain waivers or be limited to non-preferred routing, while ensuring timely and efficient mission planning and execution," Brunk explains. "Our seamless integration of RNP-RNAV capabilities with the Chinook's combat-proven tactical flight and performance management system exemplifies how Rockwell Collins is a leader in bringing open system architecture solutions to our military customers through software-only upgrades."
P-8A production
Officials and engineers at Boeing Defense, Space & Security in Berkeley, Mo., adapted the Boeing Next-Generation 737-800 single-aisle passenger jet for military use, debuting the U.S. Navy P-8A (replacing the P-3C) and P-8I variant for India. The Boeing P-8 Poseidon is a long-range anti-submarine, anti-surface warfare, and intelligence, surveillance, and reconnaissance (ISR) military aircraft intended to combine the performance and reliability of a passenger jet (4,000 Boeing 737 commercial jets flying, with a 99.8 percent dispatch rate) with an advanced mission system designed for maximum interoperability.
The P-8 is reportedly the first military aircraft to be assembled on a commercial aircraft production line. Manufacturing the P-8 at Boeing's 737 assembly facility in Renton, Wash., "leverages the best of Boeing Commercial and Boeing Defense for development and production," officials say.
The P-8 can fly at altitudes as high as 41,000 feet at speeds to 490 knots, self-deploy as far as 4,500 miles from base without refueling, and fly in virtually all flight regimes, including harsh maritime and extended operations in icing environments, for 25 years or 25,000 hours over its usable life. It is powered by dual CFM-56B commercial engines, extends sensor reach to control unmanned aerial vehicles (level 2 control-receive), and enjoys commonality with 737 aircraft to streamline training and maintenance, and ensure parts availability.
The Boeing P-8 Poseidon, growing in popularity and adoption, and is indicative of how many future military aircraft platforms are likely to be approached: integrating advanced commercial and military technologies, as well as engineering and production workflows, toward a singular goal.
Unmanned helicopter
The U.S. Navy's next-generation unmanned helicopter, the MQ-8C Fire Scout, uses a commercial airframe based on a mature helicopter with more than 1,400 airframes produced and over 4 million flight hours, the Bell 407 four-blade, single-engine, civil utility helicopter from Bell Helicopter in Fort Worth, Texas.
Use of a proven commercial airframe translates to readily available spare parts and increased ease of maintenance, officials explain.
The airframe combines with a mature unmanned systems architecture from Northrop Grumman Corp. in Falls Church, Va., to provide ISR, target-acquisition, laser-designation, and battle-management capabilities to tactical users without relying on manned aircraft or space-based assets. "The MQ-8C Fire Scout combines the better of two proven air systems: the reconnaissance, surveillance, and target acquisition architecture of a UAS, and the extended range, payload, and cargo hauling capabilities of the commercially mature Bell 407 helicopter," officials say.
Engineering and production
Technology transfer between market segments and industries extends to engineering design, development, testing, and production workflows.
"The ongoing drive to reduce cost and weight have elevated the importance of 'value engineering' to secure better deals and long-term supply agreements on electronics components and sub-assemblies. Also, there is a trend to use additive manufacturing for less critical, load-bearing parts that were previously fabricated using CNC machining or casting," says Paul Hart, chief technology officer and technical fellow at Curtiss- Wright Avionics & Electronics in Christchurch, England.
Curtiss-Wright Defense Solutions product engineers harnessed additive manufacturing, also known as 3D printing, in the company's first functioning air-flow-through (AFT) chassis based on COTS 3U VPX modules. Curtiss-Wright Technical Fellow Ivan Straznicky demonstrated the 3D-printed plastic chassis integrated with the company's VPX3-1258 single board computer (SBC) and VPX3-716 graphics modules, during January's VITA's Embedded Tech Trends (ETT) embedded computing event in Houston.
The functional 3U AFT chassis demonstrator, supports the new VITA 48.8 Air Flow Through (AFT) cooling standard designed to benefit size, weight, power, and cost (SWAP-C)-constrained platforms, such as rotorcraft and UAS. Curtiss-Wright provides flight recorders with encrypted data storage, air data computers, ruggedized single-board computers, graphics cards, switches, digital signal processor cards, and flight test instrumentation are designed for and used on military and civil aircraft.
"Certainly the lines between engineers working on military and commercial lines has been blurred with probably the only distinction being when a non-national may not be allowed access or be employed on a military program in that nation," Hart says. For example, he adds, dual-use International Traffic in Arms Regulation (ITAR) components are avoided on many European programs and seen as a big risk to the onward export market.
In the end, Hart recommends "engineers and their bosses always be aware that the electronics are not designed for the avionics industry. The art of their trade is designing open-systems architecture that can use electronics developed for the industrial and computing markets for rugged applications, yet define upgrade paths to manage obsolescence and introduce technical refreshes at the lowest cost every five to eight years." Further, he advises, "be prepared to pay top-dollar for an avionics certification expert; they are worth their weight in gold and will save considerable time and money in the long run."
Adds Honeywell's Hart, "We see the future continuing down the current path it is on. With overlapping technology and military platforms adopting more and more commercial standards and systems and technology crossover, it would be great for engineers and engineering managers to get exposure to both areas and use the best standards and processes across the commercial and military market."
Poseidon partnership
The Boeing-led P-8 Poseidon industry team includes Raytheon in Waltham, Mass.; Northrop Grumman Corp. in Falls Church, Va.; Spirit AeroSystems in Wichita, Kan.; GE Aviation Systems in Cheltenham, England; Marshall Aerospace and Defence Group in Cambridge, England; CFMI in Cincinnati; BAE Systems in Nashua, N.H.; and Marotta in Montville, N.J.
CFM International, a 50/50 joint company of Snecma Moteurs and General Electric Company, provides the CFM56-7 commercial engines that have logged more than 30 million flight hours.
Northrop Grumman's Electronic Systems sector provides the directional infrared countermeasures system and the electronic support measures system. Northrop Grumman's Aerospace Systems sector develops data links for the P-8A; the company's Integrated Systems sector supports the mission planning effort.
Raytheon provides the AN/APY-10 radar, which delivers all weather, day/night multimission maritime, littoral, and overland surveillance capabilities, as well as the MK 54 lightweight torpedo.
GE Aviation supplies the Flight Management system, an integrated open architecture that is CNS/ATM compatible with a growth path for upgrades, and a Stores Management system for the electronic control of integrated weapons management.
Spirit AeroSystems builds the 737 aircraft's fuselage and air- frame tail sections and struts in Wichita, Kan.
BAE Systems provides the mission computing and display system (MCDS), flight deck panels, and data diode. "Our mission computer suite is the digital backbone for the P-8A aircraft. It provides an interface to all sensors, communication links, countermeasures, and aircraft subsystems on board," says Gary Rubasch, program director at BAE Systems in Greenlawn, N.Y., where the MCDS is assembled and tested. "Airborne sensors in surveillance aircraft require flexible open-architecture designs that are ruggedized for demanding military needs."
Engineers at the BAE Systems Electronic Systems segment in Nashua, N.H., selected LCR Embedded Systems Inc., a manufacturer of backplanes and ruggedized integrated chassis in Norristown, Pa., to supply the chassis that houses mission computer systems on-board the P-8A. LCR is expected to deliver 13 different chassis assemblies for the P-8 program past 2020 as the U.S. completes its P-3 to P-8A fleet transition, officials say.
Best of both worlds
"Cockpit solutions for commercial airliners and military aircraft are obviously very different, partly due to the physical space available, but there's a lot of overlap between the underlying technologies," says Laurent Lenoir, vice president of the mission and function center of competence at Thales Avionics in Toulouse, France. "Thales designs modular systems with an open architecture that can achieve civil certification as well as meet the specific requirements of tactical missions."
Lenoir cites the Airbus A400M Atlas, a four-engine turboprop military transport aircraft, as a prime example. "This plane is designed with an Integrated Modular Avionics (IMA) suite that meets civil standards, and we added a host of specific military features and functions, such as data encryption, to ensure a high level of security," he says, noting that Thales does the same for helicopters and UAS.
The A400M features a full glass cockpit, common in Airbus commercial aircraft, and aircraft systems based on those in the A380 double-deck, wide-body, four-engine commercial jet airliner, but modified for military missions. In fact, it is designed with dual technologies that meet civil airspace certification standards and military specification (mil-spec) requirements.
"This platform uses the latest technology from Airbus civil aircraft, including a glass cockpit and side-stick controllers for the fly-by-wire flight control system. Unlike commercial airlines, it uses head-up displays as primary flight instruments, enhanced by large multifunction displays and, on some models, by the Enhanced Vision System, which uses a camera to assist pilots," officials say.
Thales supplies systems used in the A400M cockpit (head-down and head-up displays, control display system, and flight management system) and throughout the aircraft's avionics (IMA suite, multimode navigation, electrical systems, and utilities such as door management systems).
The A400M is the first military aircraft to be fitted with the IMA suite, developed for the A380 and tailored to the specific requirements of the A400M, according to Thales officials. "The IMA has been adapted to meet military criteria for resistance to higher vibration levels, higher electromagnetic compatibility, and a critical lightning protection system. Through its IMA platform, Thales has halved the number of parts required.
"Integration of the Thales-designed Control Display System (CDS) on the A400M marks the first time that interactive and reconfigurable screens are used on a military transport aircraft," officials describe. The CDS features eight interactive LCD screens that are sunlight-readable, compatible with night vision goggles, and derived from the system developed for the A380 commercial airliner. Additionally, they say, the A400M is the first Airbus aircraft to be pre-fitted with the HUD.
Thales developed the A400M's Flight Management System, the human-machine interface between the pilot and aircraft systems, to offer "most of the functionality associated with a top-level commercial airliner, combined with the specific functions required for tactical missions," Thales officials explain. As a result, they add, the A400M can fly missions with fewer crew members than are needed on other types of military airlifters, and it is compliant with civil air traffic standards for efficient insertion into civil air traffic and at commercial airports.
Head-mounted display for civil pilots
Thales Group officials and engineers in Toulouse, France, focused on designing and developing dual-use technologies, debuted what they are calling the first civilian head-worn display, the TopMax, at the 2015 National Business Aviation Association (NBAA) convention and exhibition, in Las Vegas last November.
The head-worn display for civilian pilots leverages Thales' experience in civil/military applications and military helmet-mounted sight display (HMSD) and head-up display (HUD) development, officials say. "The result is TopMax is a lightweight head-worn display that bridges the technological gap between a military HMSD and a civilian HUD."
First demonstrated at Paris Air Show 2015, TopMax is designed to combine the low-visibility take off/landing functions, Enhanced Flight Vision, and Synthetic Vision capabilities of a fixed HUD, with the 360-degree field of view, total eye-out functionality, and head-tracking system for target designation and cueing functions of an HMSD.
"This evolution allows a civilian pilot to look at objects like 3D traffic to better understand their position and, in some cases, like waypoints, select them for inclusion in the FMS as direct destinations, in the same way a military pilot can select targets visually for inclusion in targeting operations," officials say. "Both [commercial and military pilots] face challenges such as approach and landing at smaller airports with low visibility conditions and require a high level of situational awareness in a highly flexible operational context."
"Being inspired by our military applications to produce innovative products for the civil market is part of our DNA, but in TopMax we believe to have developed true game changer.," says Gil Michielin, Thales executive vice president of avionics.
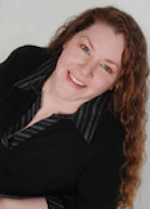
Courtney Howard | Executive Editor
Courtney, as executive editor, enjoys writing about all things electronics and avionics in PennWell’s burgeoning Aerospace and Defense Group, which encompasses Military & Aerospace Electronics, Avionics Intelligence, the Avionics Europe conference, and much more. She’s also a self-proclaimed social-media maven, mil-aero nerd, and avid avionics geek. Connect with Courtney at [email protected], @coho on Twitter, and on LinkedIn.